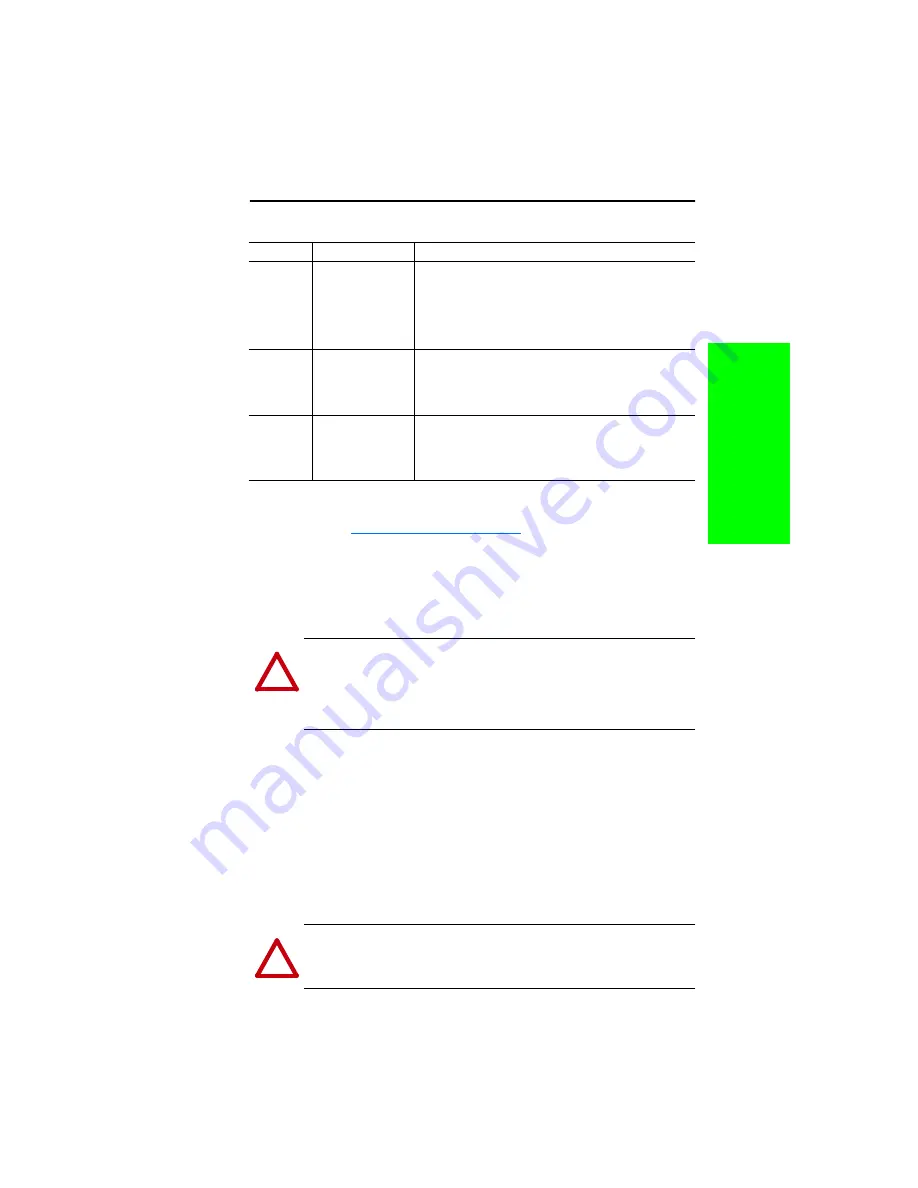
Installation/Wiring
1-9
Table 1.A Recommended Shielded Wire
EMC Compliance
Refer to
Cable Trays and Conduit
If cable trays or large conduits are to be used, refer to guidelines
presented in Wiring and Grounding Guidelines for Pulse Width
Modulated (PWM) AC Drives.
Motor Cable Lengths
Typically, for 480V AC systems, motor lead lengths less than 150 meters
(approximately 500 feet) are acceptable if using an inverter rated motor
with 1600 volt insulation. However, if your application dictates longer
lengths, or if you are using a different motor, refer to Wiring and
Grounding Guidelines for Pulse Width Modulated (PWM) AC Drives
(publication VTAC-IN002) for details.
AC Input Phase Selection (Frames 5 & 6 Only)
Location
Rating/Type
Description
Standard
(Option 1)
600V, 90°C (194°F)
XHHW2/RHW-2
Anixter
B209500-B209507,
Belden 29501-29507,
or equivalent
•
Four tinned copper conductors with XLPE insulation.
•
Copper braid/aluminum foil combination shield and tinned
copper drain wire.
•
PVC jacket.
Standard
(Option 2)
Tray rated 600V, 90°C
(194°F) RHH/RHW-2
Anixter OLF-7xxxxx or
equivalent
•
Three tinned copper conductors with XLPE insulation.
•
5 mil single helical copper tape (25% overlap min.) with three
bare copper grounds in contact with shield.
•
PVC jacket.
Class I & II;
Division I & II
Tray rated 600V, 90°C
(194°F) RHH/RHW-2
Anixter 7V-7xxxx-3G
or equivalent
•
Three bare copper conductors with XLPE insulation and
impervious corrugated continuously welded aluminum armor.
•
Black sunlight resistant PVC jacket overall.
•
Three copper grounds on #10 AWG and smaller.
!
ATTENTION: To avoid a possible shock hazard caused by induced
voltages, unused wires in the conduit must be grounded at both ends.
For the same reason, if a drive sharing a conduit is being serviced or
installed, all drives using this conduit should be disabled. This will help
minimize the possible shock hazard from “cross coupled” motor leads.
!
ATTENTION: To avoid a shock hazard, ensure that all power to the
drive has been removed before performing the following.
Summary of Contents for 9VT201-007HTNNN
Page 1: ...VTAC 9 AC Drive Firmware Version 3 xx User Manual ...
Page 4: ...soc 2 ...
Page 14: ...P 8 Overview Publication 9VT UM001D EN P Notes ...
Page 56: ...1 42 Installation Wiring Publication 9VT UM001D EN P Notes ...
Page 62: ...2 6 Start Up Publication 9VT UM001D EN P Notes ...
Page 130: ...3 68 Programming and Parameters Publication 9VT UM001D EN P Notes ...
Page 150: ...4 20 Troubleshooting Publication 9VT UM001D EN P Notes ...
Page 176: ...A 26 Supplemental Drive Information Publication 9VT UM001D EN P Notes ...
Page 196: ...B 20 Using the LCD OIM Publication 9VT UM001D EN P Notes ...
Page 212: ...C 16 Application Notes Publication 9VT UM001D EN P Notes ...
Page 223: ......