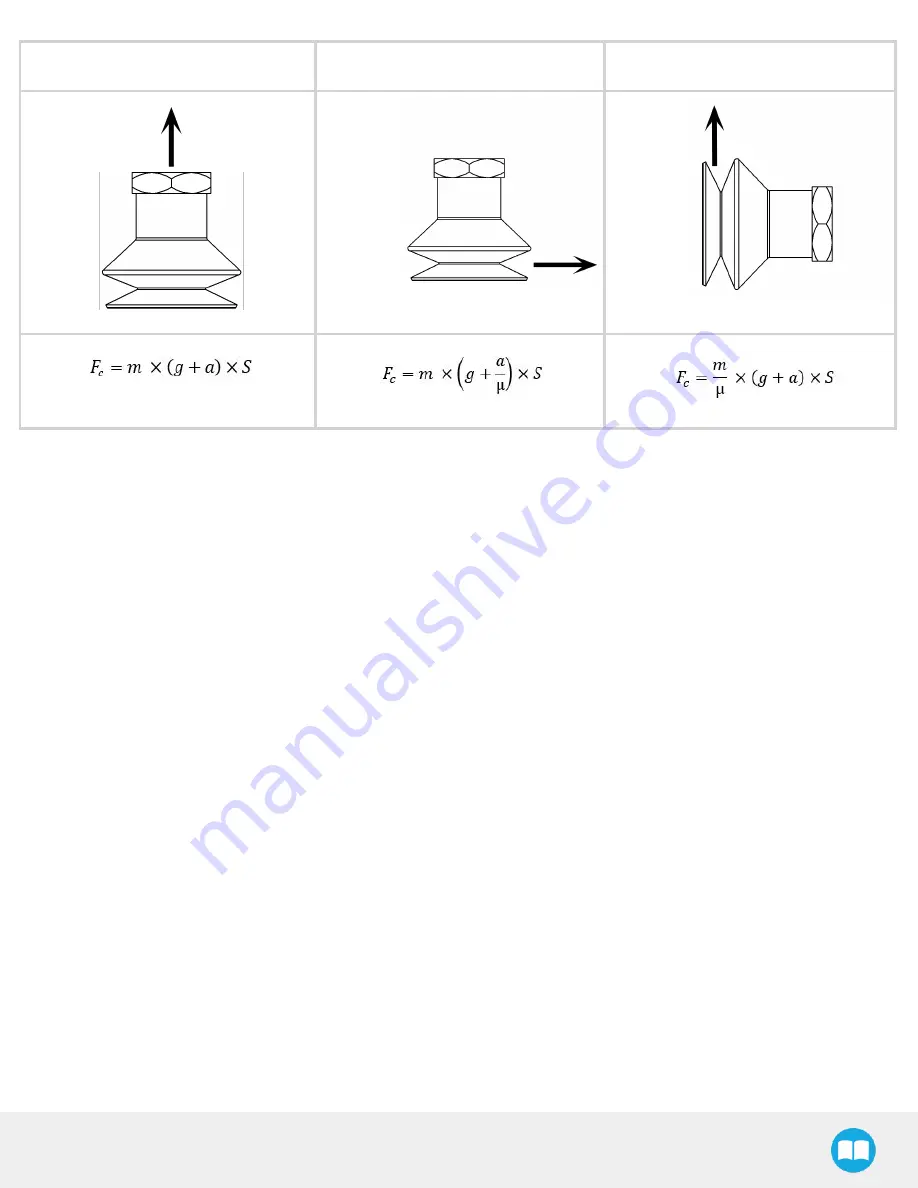
AirPick - Instruction Manual
Case #1
Case #2
Case #3
Where:
l
m = mass (kg)
l
g = gravitational acceleration (m/s
2
)
l
a = robot acceleration (m/s
2
)
l
µ = friction coefficient
l
S = safety factor
The maximum grip strength of the suction cup must always be bigger than the payload (F
p
> F
c
) to guarantee the good grip of the
piece. Robotiq recommends a minimum security factor of 2 in every case. However, a factor 4 is recommended for the next
situations:
l
Low friction coefficient
l
Important robot acceleration
l
Non-uniform surface
l
Porous surface
l
Unequal distribution of the payload in regards to the suction cups
Two categories of material can be lifted by the vacuum gripper: porous and non-porous. A non-porous material is defined as a
material where air leakages are negligible and where it is possible to precisely attain a vacuum percentage between 10 and 80%.
83
Summary of Contents for AirPick
Page 25: ...Fig 3 7 Mounting air nodes suction cups air bolts air nuts on the bracket 25...
Page 27: ...Fig 3 9 Robotiq Vacuum Gripper with pigtail cable and device cable wiring scheme 27...
Page 35: ...Fig 4 1 Vacuum Gripper control logic overview 35...
Page 57: ...7 Click on the New Project icon in the upper left corner of the screen 57...
Page 58: ...AirPick Instruction Manual 8 Enter a name for your program and click on the OK button 9 58...
Page 76: ...Fig 6 5 Minimum and maximum arrangement possibilities of the air nodes position 76...
Page 77: ...AirPick Instruction Manual 6 1 3 Air nodes Fig 6 6 Air nodes dimensions 77...
Page 103: ...AirPick Instruction Manual 12 Appendix Fig 12 1 Pneumatic schema of the AirPick Vacuum Gripper...