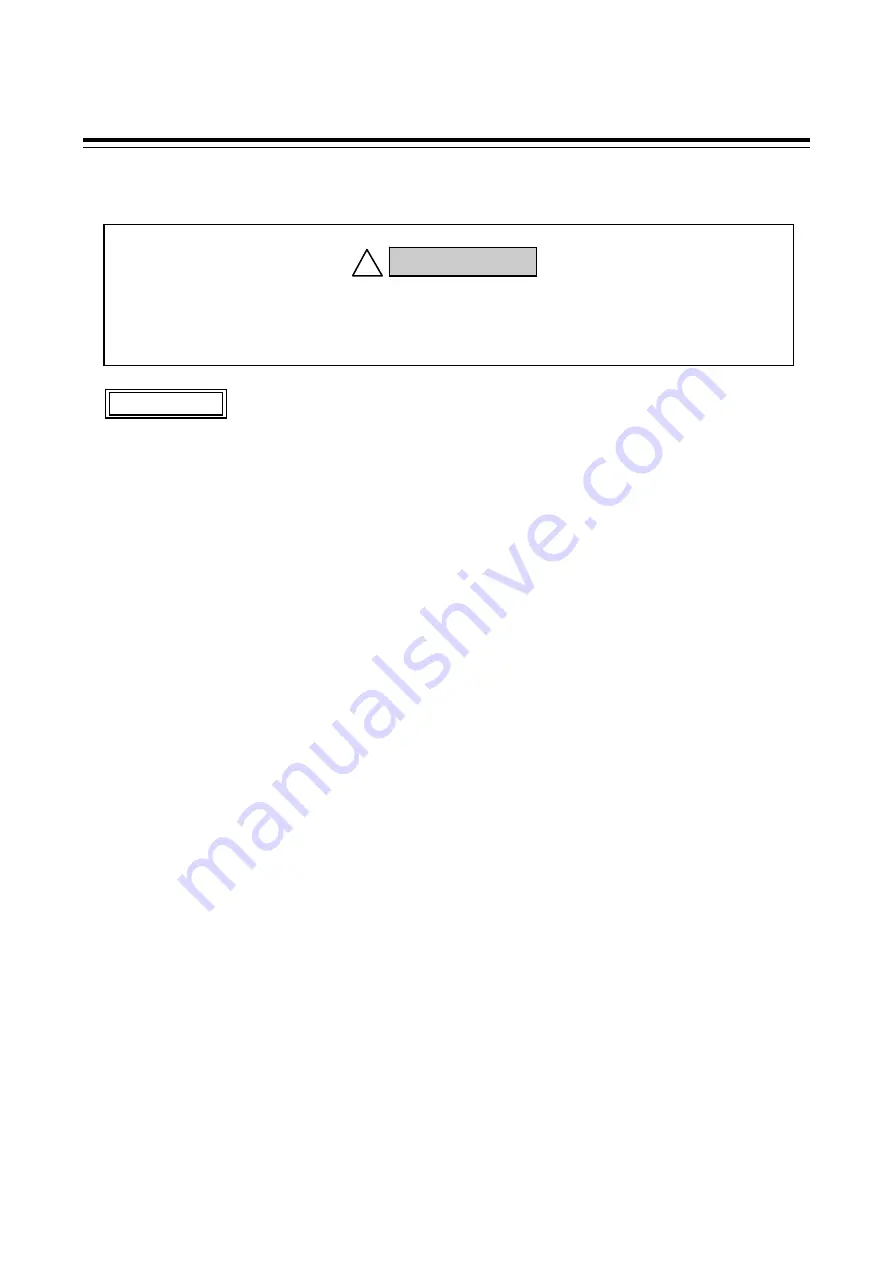
4. WIRING
IMS01J02-E4
27
4.2 Connections
Connect connectors correctly in the right position. If it is forcibly pushed in with pins in
the wrong positions, the pins may be bent resulting in instrument failure.
When connecting or disconnecting the connectors, do not force it too far to right and left
or up and down, but move it on the straight. Otherwise, the connector pins may be bent,
causing instrument failure.
When disconnecting a connector, hold it by the connector itself. Disconnecting
connectors by yanking on their cables can cause breakdowns.
To prevent malfunction, never touch the contact section of a connector with bare hands
or with hands soiled with oil or the like.
To prevent malfunction, connect cable connectors securely, then firmly tighten the
connector fastening screws.
To prevent damage to cables, do not bend cables over with excessive force.
If the instrument is easily affected by noise, use the ferrite core in the both ends of the
communication cable (nearest the connector).
CAUTION
To prevent electric shock or instrument failure, turn off the power before
connecting or disconnecting the instrument and peripheral equipment.
WARNING
!