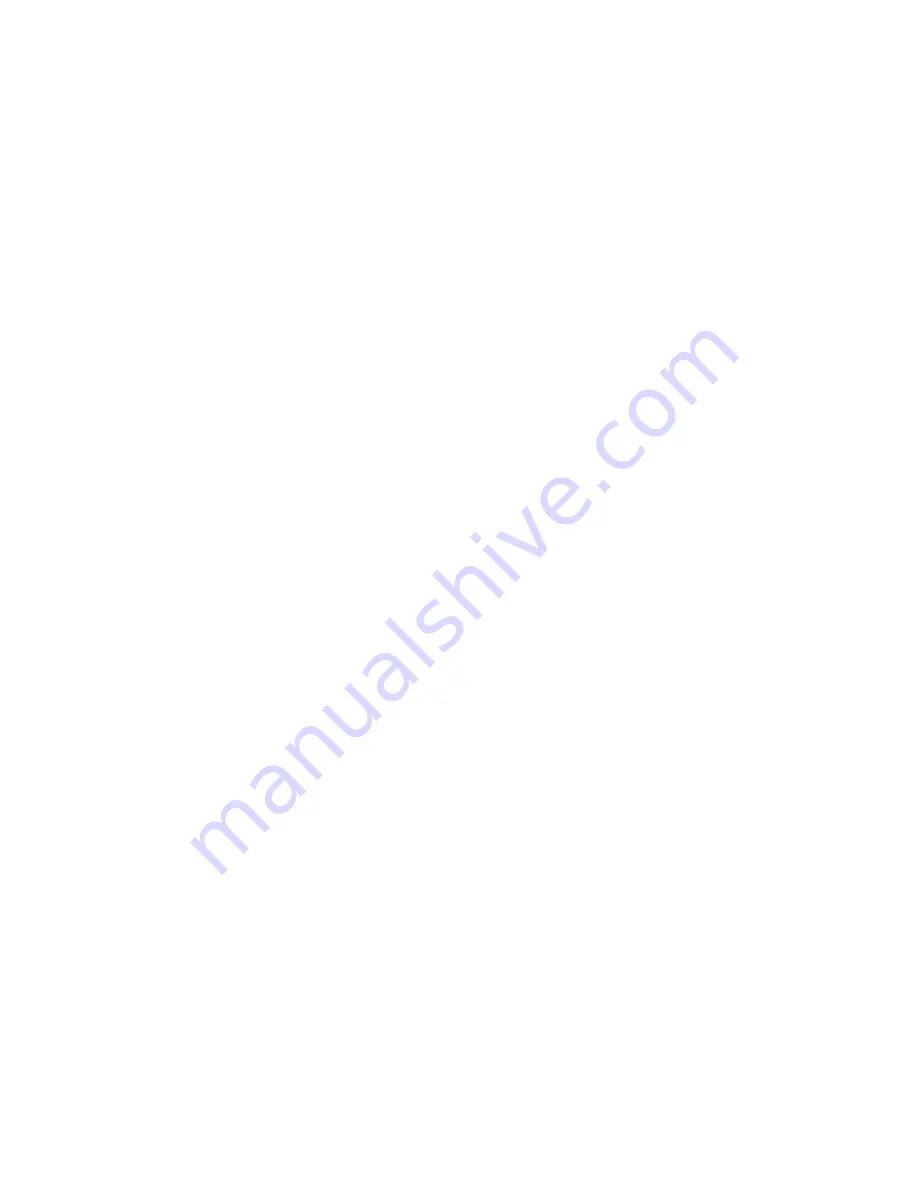
Lynx™ Strain Gage Button Sensors LS‑B‑127‑50/125/500/2000 | Product Manual
48
RJG, Inc.
CALIBRATION
RJG recommends that sensors be calibrated
every year, but the need for regular calibration
depends largely on the accuracy required
for the application and the requirements
of individual quality systems and industry
regulations.
RJG sensors are designed to hold calibration for
operating life. The vast majority stay within a
2% accuracy specification, which is sufficient for
most customer applications.
COMMON FACTORS AFFECTING SENSOR
RECALIBRATION
1.
Required Application Accuracy
Some applications require more accuracy
than others. If using cavity pressure control
on a precise part with a narrow processing
window, it may be important to maintain sensor
calibration to within 1%.
If simply detecting short shots, calibration shifts
of 5% or more may be tolerated. As a point of
reference, a 2% calibration error means that
a cavity pressure of 3,000 psi (207 bar) may
read as low as 2,940 psi (203 bar), or as high
as 3,060 psi (211 bar), which is insignificant
in most applications. For most applications,
calibration accuracy of 2% is more than
sufficient, and is used by RJG as the specification
for repaired sensors.
2.
Quality System Regulations
If US Food and Drug Administration (FDA)
quality system requirements must be met, or
those of other stringent quality systems, sensor
calibration may be required. However, even in
these cases, there is often flexibility to adjust
guidelines to meet the needs of the application.
3.
Sensor Cycle Count
In the most aggressive environments, it takes
at least 100,000 cycles for a sensor to show
significant calibration errors. In more typical
applications, calibration will remain stable for
500,000–1,000,000 cycles. Even then, many
sensors in the field with multiple millions of
cycles show little calibration shift. If a sensor is
in a low volume mold that sees fewer cycles,
the need for sensor recalibration is minimized.
4.
Sensor Load
The higher the peak load on the sensor, the
more the loading nub can wear—and the higher
the potential for calibration shift. Low force
sensors (125‑pound sensors, for example) show
less calibration shift than high force sensors
(2000‑pound sensors); sensors that run at the
lower end of their force range (less than 40% of
full scale) show less calibration shift than sensors
that run at the high end of their range.
5.
Sensor Operating Temperature
The higher the mold temperature, the greater
the potential for calibration shift. Below 212 °F
(100 °C), calibration usually remains stable.
Sensors running at 300–400 °F (150–200 °C)
have a greater potential for permanent
calibration shift over time.
TESTING & CALIBRATION (
continued
)
Summary of Contents for Lynx LS-B-127-125
Page 2: ...PRINT DATE 07 21 2020 REVISION NO 0...
Page 6: ...Lynx Strain Gage Button Sensors LS B 127 50 125 500 2000 Product Manual iv RJG Inc...
Page 8: ...Lynx Strain Gage Button Sensors LS B 127 50 125 500 2000 Product Manual vi RJG Inc...
Page 14: ...Lynx Strain Gage Button Sensors LS B 127 50 125 500 2000 Product Manual 6 RJG Inc...
Page 58: ...Lynx Strain Gage Button Sensors LS B 127 50 125 500 2000 Product Manual 50 RJG Inc...
Page 65: ......