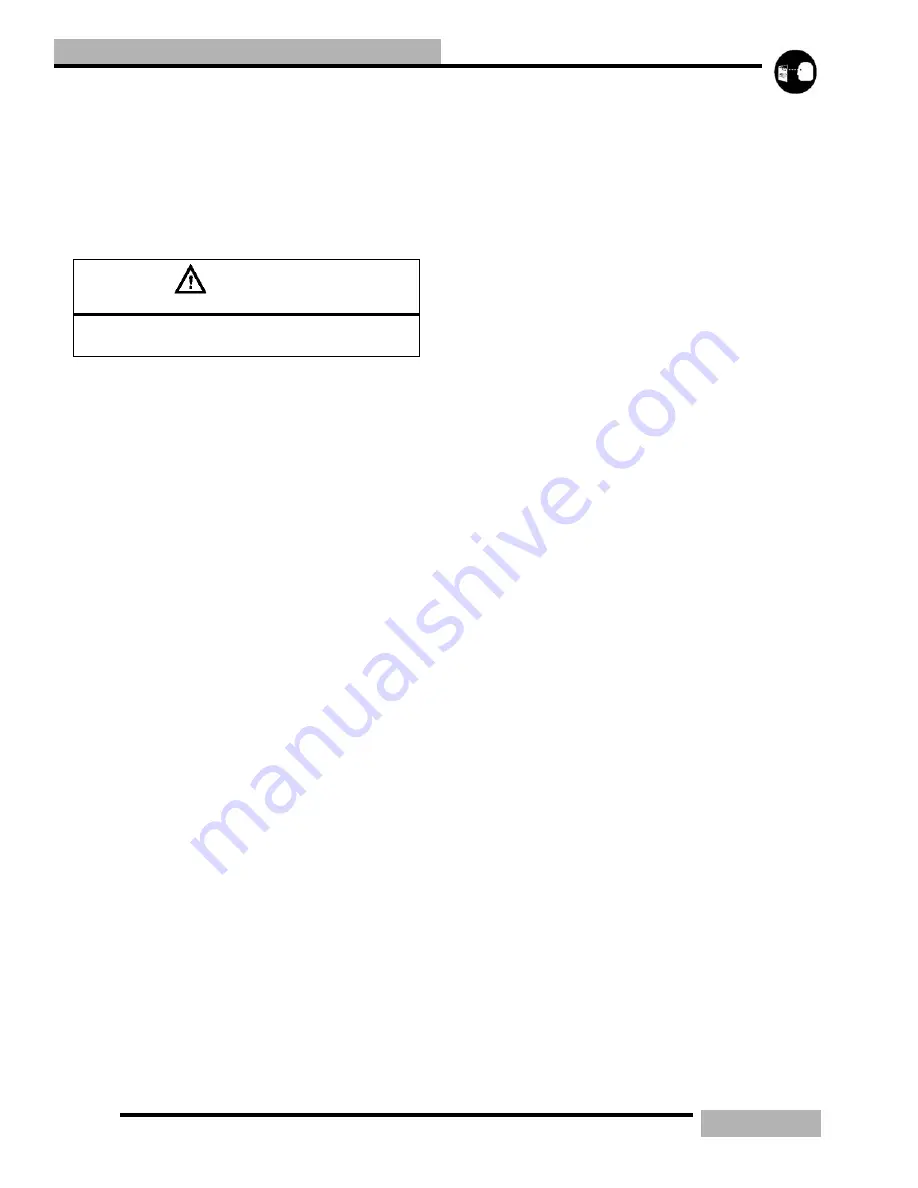
11.26
REAR SUSPENSION
remove as much dirt and grime as possible by scrubbing
with a soft bristle brush. Never pressure wash your shock,
as this can force water and debris inside which will
damage the seals. Dry the shock assembly with
compressed air, if available, or use clean towels.
5.
Use a 3/32" Hex Key to remove the button head screw
from the FOX air valve in the shock body.
6.
Securely clamp Fox Nitrogen Safety Needle in vice.
7.
Insert the Fox Safety Needle squarely into center of gas
valve.
8.
Using a blunt object, depress the air valve core to release
pressure.
9.
When the shock is FULLY DISCHARGED, pull reservoir
away from the Fox Safety Needle in a straight, smooth
motion.
10. Clamp the body end eyelet of the shock securely in vice
with shaft side up.
11. Using the 1 3/8
"
wrench, loosen and unscrew the bearing
assembly from the shock body. If the body cap unscrews
instead of the bearing, that is OK. You will need to remove
both for this rebuild procedure.
12. Clamp the shock in the vice using the body clamp blocks.
If the bearing is still in the body, use the 1 3/8” end wrench
to loosen and unthread the bearing. If the body cap is what
needs removal, use the large crescent wrench to loosen
and unthread the body cap.
13. Remove the shaft assembly from the body tube, and place
on a clean, lint free paper towel. Remove the shock from
the vice and pour shock oil from body tube into a proper
disposal container. Do not re-use old shock oil.
14. Using the handle of the mallet, push the IFP out of the
shock body on to a folded shop towel.
15. Remove the bleed screw from the IFP using the 1/8" T-
Handle
16. Clean the IFP with solvent. Dry with compressed air in a
well ventilated area. If compressed air is not available, dry
parts using clean, lint free paper towels and let sit in a well
ventilated area to allow the solvents to evaporate.
17. Set body assembly aside on a clean, lint free towel.
18. Clamp the shaft eyelet securely in vice with the piston end
up.
19. Using a 9/16" wrench, remove the piston lock nut from the
end of the shaft.
20. Hold the tip of the Phillips Head Screwdriver against the
end of shaft. Hold the piston assembly under the top-out
plate and lift upwards. Slide the piston assembly onto the
shaft of the screwdriver. Pull the Screwdriver away from
shock shaft while supporting the piston assembly. Set this
on a clean, lint free towel. There are many pieces to the
piston assembly, and the assembly order of these pieces is
critical to the proper performance of your shock. This step
ensures that the proper order is kept.
21. Slide bearing assembly off of shaft. Use extreme caution
not to scratch inside of the bearing assembly when passing
it over the threads at end of shaft and set it on a clean, lint
free towel.
22. Remove the bleed screw from the IFP and set them both
on a clean, lint free towel.
FOX PS-5 ASSEMBLY
1.
Using a small pair of snap ring pliers, remove the snap ring
from the bearing housing. Using your fingers, remove the
FIST scraper from the housing. Use a scribe or a dental
pick to remove the o-ring from the inside of the FIST
scraper by "spearing" the seal with the point of the scribe
and pulling it out. Use extreme caution when using a
scribe to remove seals. Always "spear" the seal with the
point of the scribe. Do not wedge the point of the scribe in
behind the seal. This can scratch the surface of the seal
groove which will compromise the performance and
reliability of the shock absorber.
2.
Use the scribe to remove the u-cup wiper and o-ring seals
from the bearing housing. Be careful not to scratch the seal
grooves or the DU bushing that is pressed into the bearing.
3.
Thoroughly clean the FIST scraper, bearing housing, and
piston assembly with solvent. Dry with compressed air in
a well ventilated area. If compressed air is not available,
dry parts using clean, lint free paper towels and let sit in a
well ventilated area, to allow the remaining solvent to
evaporate.
4.
Use a scribe or dental pick to remove the o-ring seal from
the IFP.
5.
Install the new, well lubricated, o-ring into the FIST
scraper. Check to make sure the seal is properly seated,
and is not twisted. If a tool is required to aid in proper
seating of o-ring, use the non-writing end of a pen, or a
similar soft, blunt object, to push it in.
6.
Install the new, well lubricated, o-rings into the bearing
housing. Correct placement of the shaft seal o-ring is in the
groove next to the DU bushing. Check to make sure the
seals are properly seated, and are not twisted. If a tool is
required to aid in proper seating of o-ring, use the non-
writing end of a pen, or a similar soft, blunt object, to push
it in.
7.
Install the new U-cup seal into bearing. U-cup should be
installed so the cupped end is facing the DU bushing
inside of bearing. Check to make sure seal is properly
CAUTION
Point air valve away from face and body when charging
or discharging any shock.
Summary of Contents for SUPERSPORT 2006
Page 48: ...NOTES SPECIFICATIONS 1 48...
Page 55: ...2 7 GENERAL SAE TAP DRILL SIZES METRIC TAP DRILL SIZES DECMIAL EQUIVALENTS...
Page 60: ...2 12 GENERAL SPECIAL TOOLS...
Page 61: ...2 13 GENERAL...
Page 62: ...2 14 GENERAL...
Page 106: ...4 18 CARBURETION...
Page 139: ...6 27 ENGINE 340 550 ENGINE REBUILDING 10 11 3 4 12 13 5 2 14 1 16 15 16 9 17 6 7 8...
Page 156: ...7 12 CLUTCHING 1 1 2 3 4 5 6 7 18 17 10 8 9 13 12 11 15 16 14...
Page 192: ...8 20 FINAL DRIVE...
Page 200: ...10 2 FRONT SUSPENSION STEERING FUSION IQ RMK 600 RMK Fusion 14 78...
Page 201: ...10 3 FRONT SUSPENSION STEERING EDGE RMK Apply Polaris All Season Grease to all zerks...
Page 202: ...10 4 FRONT SUSPENSION STEERING 42 5 EDGE Apply Polaris All Season Grease to all zerks...
Page 203: ...10 5 FRONT SUSPENSION STEERING WIDETRAK Apply Polaris All Season Grease to all zerks...
Page 244: ...11 28 REAR SUSPENSION...
Page 256: ...12 12 CHASSIS HOOD...
Page 282: ...13 26 ELECTRICAL...
Page 288: ...13 32 ELECTRICAL...
Page 289: ...14 1 WIRE DIAGRAM 2006 600 FUSION HO HOOD...
Page 290: ...14 2 WIRE DIAGRAM 2006 HO RMK HOOD...
Page 291: ...14 3 WIRE DIAGRAM 600 HO FUSION RMK CHASSIS...
Page 292: ...14 4 WIRE DIAGRAM 600 HO FUSION RMK CHASSIS CALL OUTS...
Page 293: ...14 5 WIRE DIAGRAM 700 900 ENGINE...
Page 294: ...14 6 WIRE DIAGRAM 700 900 ENGINE AND ENGINE CALL OUTS...
Page 295: ...14 7 WIRE DIAGRAM 700 900 CHASSIS...
Page 297: ...14 9 WIRE DIAGRAM 340 550 FUJI FAN ENGINE CHASSIS...
Page 298: ...14 10 WIRE DIAGRAM 500 FUJI ENGINE CHASSIS...
Page 299: ...14 11 WIRE DIAGRAM 500 600 IBERTY ENGINE CHASSIS...