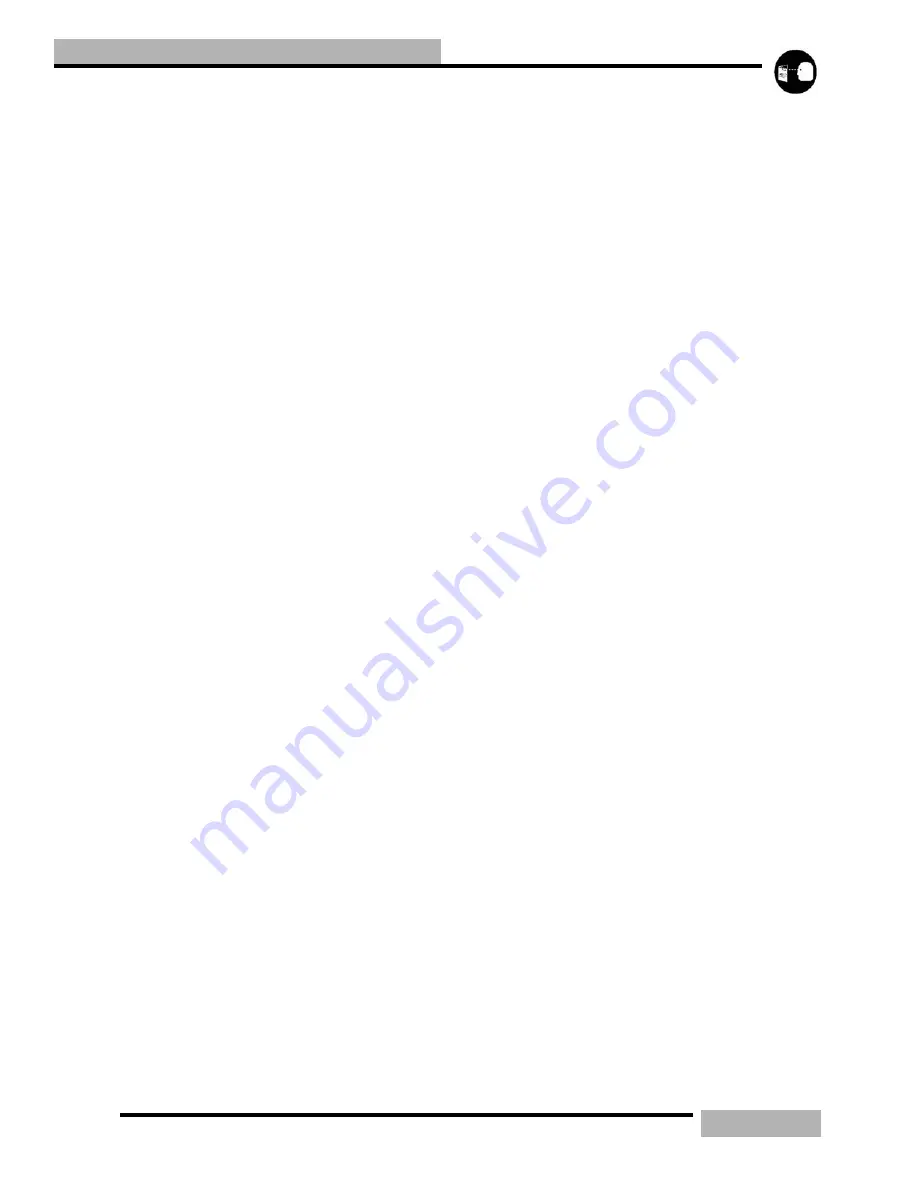
7.8
CLUTCHING
BACK-SHIFTING
Back-shifting occurs when the track encounters an increased
load (demand for more torque). Back-shifting is a function of
a higher shift force within the driven clutch then within the
drive clutch. Several factors, including riding style,
snowmobile application, helix angles, and vehicle gearing
determine how efficient the drive system back-shifts. The
desired engine operating RPM should never fall below 200
RPM when the drive system back-shifts.
FINAL GEARING
The final drive gear ratio plays an important role in how much
vehicle load is transmitted back to the helix. A tall gear ratio
(lower numerical number) typically results in lower initial
vehicle acceleration, but a higher top-end vehicle speed. A
lower gear ratio (higher numerical number) typically results in
a higher initial vehicle acceleration, but a lower top-end
vehicle speed.
Choosing the proper gear ratio is important to overall drive
system performance. Lowering the final drive gear ratio will
compress the MPH scale between the low and high ratio lines,
while raising the final drive gear ratio will expand the MPH
scale between the low and high ratio lines.
When deciding on which gear ratio to use, the operator must
factor in the decision where the snowmobile will be ridden,
what type of riding will be encountered, and the level of
performance the operator hopes to achieve.
Gearing a snowmobile too low for extended high-speed runs
may cause damage to the drive belt and drive system, while
gearing a snowmobile too high for deep-snow, mountain use
may cause premature belt and clutch wear.
Typically, it is recommended to gear the snowmobile with a
slightly higher ratio than the actual top speed the snowmobile
will ever achieve.
1:1 Shift Ratio
A 1:1 shift ratio occurs when the drive clutch and the driven
clutch are rotating at the same RPM. In this mode, the drive
system is at its highest efficiency. Drive system efficiency
falls off past the 1:1 shift ratio.
The mathematical vehicle speed for a given gear ratio at a 1:1
shift ratio is represented in the chaincase gearing charts
located in the Final Drive Chapter.
LOW / HIGH RATIO LINES
The low ratio line is the mechanical position when the drive
belt is all the way down into the drive clutch, and all the way
out on the driven clutch. The high ratio line represents when
the drive belt is all the way out on the drive clutch, and all the
way in on the driven clutch.
Note that the high ratio line is past the ideal 1:1 shift ratio.
DRIVEN HELIX / RAMP
The helix cam is the primary torque feedback component
within the driven clutch, regardless of driven clutch type. The
beginning angle of the helix must transmit enough torque
feedback to the moveable sheave in order to pinch the drive
belt while minimizing belt slip. The flatter or lower the helix
angle, the more side force will be exerted on the moveable
sheave, while the steeper, or higher the helix angle, the less
side force will be exerted on the moveable sheave.
Summary of Contents for SUPERSPORT 2006
Page 48: ...NOTES SPECIFICATIONS 1 48...
Page 55: ...2 7 GENERAL SAE TAP DRILL SIZES METRIC TAP DRILL SIZES DECMIAL EQUIVALENTS...
Page 60: ...2 12 GENERAL SPECIAL TOOLS...
Page 61: ...2 13 GENERAL...
Page 62: ...2 14 GENERAL...
Page 106: ...4 18 CARBURETION...
Page 139: ...6 27 ENGINE 340 550 ENGINE REBUILDING 10 11 3 4 12 13 5 2 14 1 16 15 16 9 17 6 7 8...
Page 156: ...7 12 CLUTCHING 1 1 2 3 4 5 6 7 18 17 10 8 9 13 12 11 15 16 14...
Page 192: ...8 20 FINAL DRIVE...
Page 200: ...10 2 FRONT SUSPENSION STEERING FUSION IQ RMK 600 RMK Fusion 14 78...
Page 201: ...10 3 FRONT SUSPENSION STEERING EDGE RMK Apply Polaris All Season Grease to all zerks...
Page 202: ...10 4 FRONT SUSPENSION STEERING 42 5 EDGE Apply Polaris All Season Grease to all zerks...
Page 203: ...10 5 FRONT SUSPENSION STEERING WIDETRAK Apply Polaris All Season Grease to all zerks...
Page 244: ...11 28 REAR SUSPENSION...
Page 256: ...12 12 CHASSIS HOOD...
Page 282: ...13 26 ELECTRICAL...
Page 288: ...13 32 ELECTRICAL...
Page 289: ...14 1 WIRE DIAGRAM 2006 600 FUSION HO HOOD...
Page 290: ...14 2 WIRE DIAGRAM 2006 HO RMK HOOD...
Page 291: ...14 3 WIRE DIAGRAM 600 HO FUSION RMK CHASSIS...
Page 292: ...14 4 WIRE DIAGRAM 600 HO FUSION RMK CHASSIS CALL OUTS...
Page 293: ...14 5 WIRE DIAGRAM 700 900 ENGINE...
Page 294: ...14 6 WIRE DIAGRAM 700 900 ENGINE AND ENGINE CALL OUTS...
Page 295: ...14 7 WIRE DIAGRAM 700 900 CHASSIS...
Page 297: ...14 9 WIRE DIAGRAM 340 550 FUJI FAN ENGINE CHASSIS...
Page 298: ...14 10 WIRE DIAGRAM 500 FUJI ENGINE CHASSIS...
Page 299: ...14 11 WIRE DIAGRAM 500 600 IBERTY ENGINE CHASSIS...