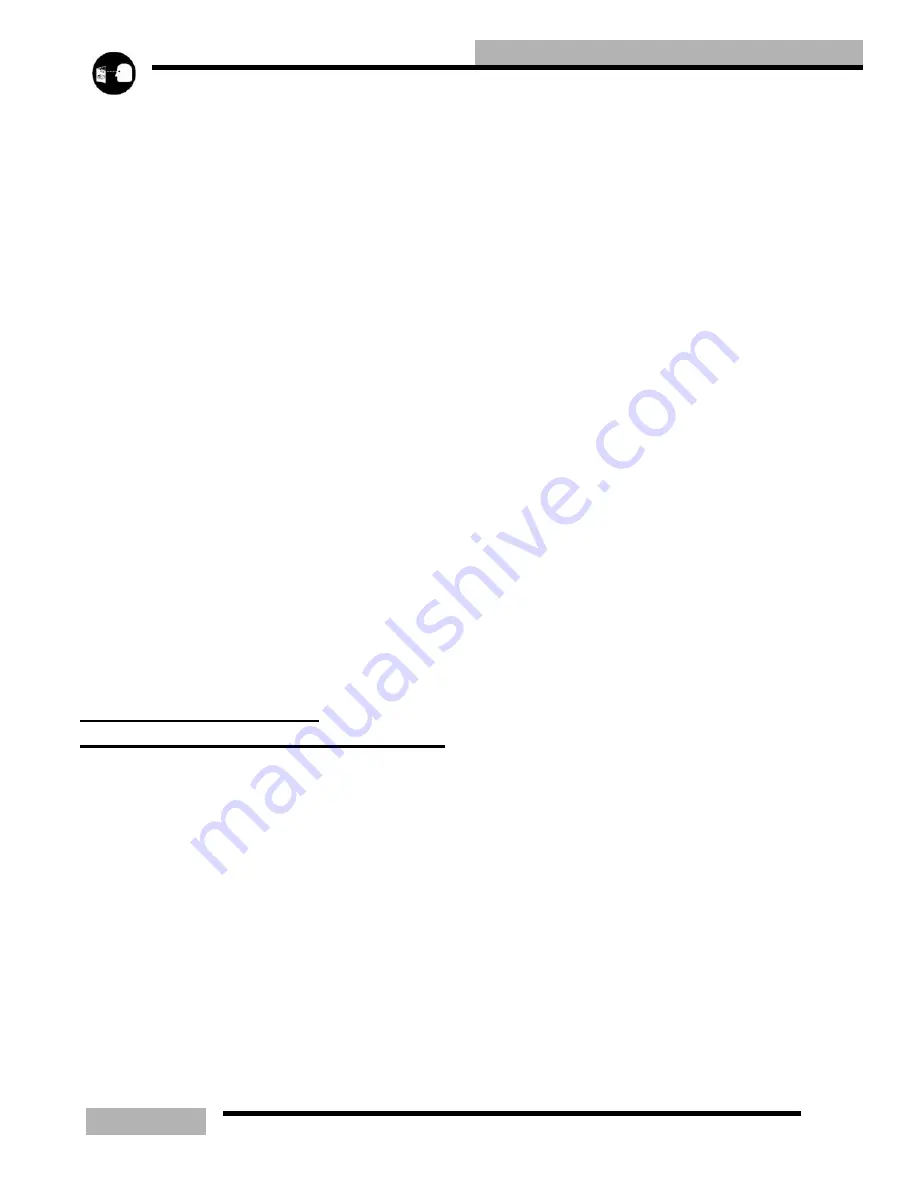
11.3
REAR SUSPENSION
eliminating kickback. The factory setting are usually adequate
for all riders in all conditions.
The rear rear scissor stop (RRSS) couples the movement o the
rear torque arm with the front torque arm and limits the
amount of independent movement between the rear torque arm
and the front torque arm.
Adjusting the RRSS either allows more weight to transfer to
the rear for more traction, or allows less weight to transfer to
the rear, resulting in improved cornering performance. And
adjustment dot is located on the RRSS. This dot id at the
higher end of the scissor stop.
Moving the RRSS to a higher position will reduce weight
transfer, improve chatter bump ride and improve cornering
performance.
REAR TORSION SPRING TENSION
ADJUSTMENT
Rear spring tension adjustments are made by rotating the
eccentric spring block. The block provides three spring tension
positions. This adjustment is easier if the long spring leg is
lifted over the roller and replaced after the block is properly
positioned. Always maintain equal adjustment on both sides.
Torsion springs are much like coil springs, although shaped
differently. The rate of the torsion spring is controlled by the
wire diameter of the spring, and the number of coils. Pre-load
is controlled by the free opening angle. see “TORSION
SPRING ADJUSTMENT” on page 11.5.
REAR SUSPENSION
ADJUSTMENTS AND SETTINGS
REAR SUSPENSION ADJUSTMENT
PROCEDURES
It is a good idea to have customers break the suspension in for
approximately 150 miles (240 km) before fine tuning
adjustments are made.
All settings will vary from rider to rider, depending on rider
weight, vehicle speed, riding style, and trail conditions. We
recommend starting with factory settings and then customizing
each adjustment individually to suit rider preference. The
machine should be methodically tested under the same
conditions after each adjustment (trail and snow conditions,
vehicle speed, riding position, etc.) until a satisfactory ride is
achieved. Adjustments should be made to one area at a time, in
order to properly evaluate the change.
The purpose of the front rear scissor stop (FRSS) is to control
the bump attitude of the rear suspension. As the front torque
arm (FTA) hits the bump, it forces the rear scissor to collapse a
predetermined amount, depending on the FRSS block position.
This accomplishes two important things, it allows a lighter
spring rate on the FTA because it can borrow spring rate from
the rear torsion springs; and it prepares the rear portion of the
suspension for the bump, reducing secondary kick back.
The FRSS is made of a resilient material allowing smooth
action and preventing any suspension component damage.
This unique feature is applied to the EDGE rear suspensions.
Summary of Contents for SUPERSPORT 2006
Page 48: ...NOTES SPECIFICATIONS 1 48...
Page 55: ...2 7 GENERAL SAE TAP DRILL SIZES METRIC TAP DRILL SIZES DECMIAL EQUIVALENTS...
Page 60: ...2 12 GENERAL SPECIAL TOOLS...
Page 61: ...2 13 GENERAL...
Page 62: ...2 14 GENERAL...
Page 106: ...4 18 CARBURETION...
Page 139: ...6 27 ENGINE 340 550 ENGINE REBUILDING 10 11 3 4 12 13 5 2 14 1 16 15 16 9 17 6 7 8...
Page 156: ...7 12 CLUTCHING 1 1 2 3 4 5 6 7 18 17 10 8 9 13 12 11 15 16 14...
Page 192: ...8 20 FINAL DRIVE...
Page 200: ...10 2 FRONT SUSPENSION STEERING FUSION IQ RMK 600 RMK Fusion 14 78...
Page 201: ...10 3 FRONT SUSPENSION STEERING EDGE RMK Apply Polaris All Season Grease to all zerks...
Page 202: ...10 4 FRONT SUSPENSION STEERING 42 5 EDGE Apply Polaris All Season Grease to all zerks...
Page 203: ...10 5 FRONT SUSPENSION STEERING WIDETRAK Apply Polaris All Season Grease to all zerks...
Page 244: ...11 28 REAR SUSPENSION...
Page 256: ...12 12 CHASSIS HOOD...
Page 282: ...13 26 ELECTRICAL...
Page 288: ...13 32 ELECTRICAL...
Page 289: ...14 1 WIRE DIAGRAM 2006 600 FUSION HO HOOD...
Page 290: ...14 2 WIRE DIAGRAM 2006 HO RMK HOOD...
Page 291: ...14 3 WIRE DIAGRAM 600 HO FUSION RMK CHASSIS...
Page 292: ...14 4 WIRE DIAGRAM 600 HO FUSION RMK CHASSIS CALL OUTS...
Page 293: ...14 5 WIRE DIAGRAM 700 900 ENGINE...
Page 294: ...14 6 WIRE DIAGRAM 700 900 ENGINE AND ENGINE CALL OUTS...
Page 295: ...14 7 WIRE DIAGRAM 700 900 CHASSIS...
Page 297: ...14 9 WIRE DIAGRAM 340 550 FUJI FAN ENGINE CHASSIS...
Page 298: ...14 10 WIRE DIAGRAM 500 FUJI ENGINE CHASSIS...
Page 299: ...14 11 WIRE DIAGRAM 500 600 IBERTY ENGINE CHASSIS...