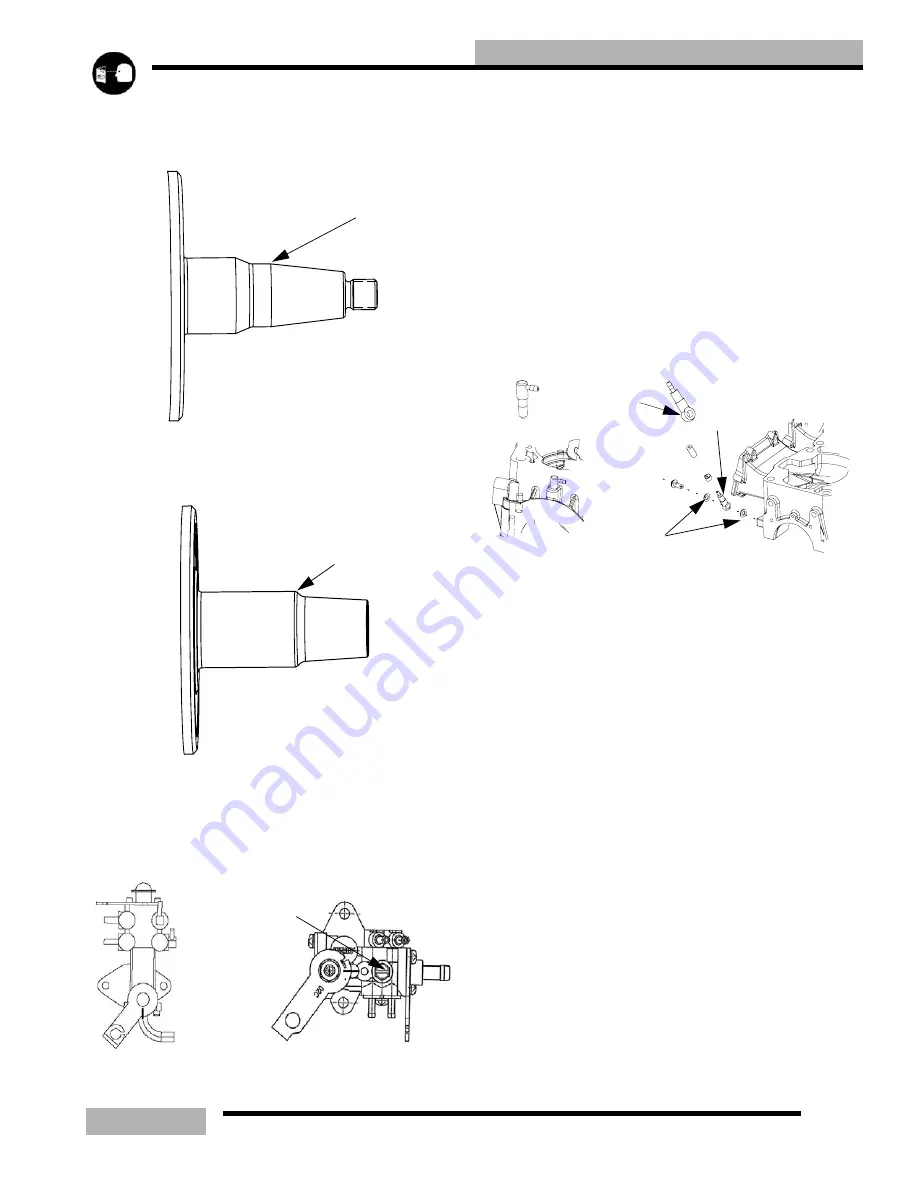
3.13
MAINTENANCE
When checking the crankshaft runout on the
MAG
side. Place
the dial indicator end at 1/2
”
(12.7mm) from the bearing flat
(A).
When checking the crankshaft runout from the
PTO
side.
Place the dial indicator end where the taper starts after the
bearing flat (B).
NOTE: Acceptable crankshaft runout (in a crank
fixture) is 0 - .0015
”
(0 - .04mm) on Liberty
t
engines.
0 - .0025
”
(0 - .07mm) on Fuji engines.
OIL PUMP BLEEDING
1.
To aid in bleeding the air out of the oil lines, fill oil
reservoir with the appropriate Polaris injector oil. This will
add pressure to the oil lines.
2.
Loosen the bleed screw (A). After approximately 30
seconds oil should flow from beneath the screw head. This
will indicate the pump is free of the air.
3.
Tighten bleed screw (A) securely.
NOTE: Any time that the engine is disassembled or
repaired, it is important that the oil supply from the
oil pump be checked and full of oil.
IMPORTANT: The oil pump must always be bled
following any service to the oil injection system or
engine.
FITTING TYPES
VERIFYING CHECK VALVE OPERATION
1.
To check the operation of the fittings, fill the oil reservoir,
bleed the pump.
2.
Remove the check valve (A,B) from the component.
3.
Place the oil line (with check valve) in a safe area where no
moving engine part will make contact with it.
4.
Start the engine and let it idle for approximately 1-2
minuets.
5.
Drops of oil should be visible from the check valve after
the engine has idled 1 to 2 minuets, with a drop occurring
every few seconds.
6.
If oil does not flow from one of the check valves, remove
the oil line from the check valve and repeat step 4, if oil is
present during this test replace the faulty check valve.
NOTE: Valves should open with 2-7 lbs of pressure.
NOTE: Install new sealing washers (C) upon
installation on either side of the banjo check valve.
If oil does not flow with the check valves removed from their
feed lines, check the following
• In line filter blocked
• Air may not be bled from the oil pump
• Feed lines leaking
MAG END
1/2”(12.7
A
PTO END
B
PTO END
A
BANJO TYPE
B
C
Summary of Contents for SUPERSPORT 2006
Page 48: ...NOTES SPECIFICATIONS 1 48...
Page 55: ...2 7 GENERAL SAE TAP DRILL SIZES METRIC TAP DRILL SIZES DECMIAL EQUIVALENTS...
Page 60: ...2 12 GENERAL SPECIAL TOOLS...
Page 61: ...2 13 GENERAL...
Page 62: ...2 14 GENERAL...
Page 106: ...4 18 CARBURETION...
Page 139: ...6 27 ENGINE 340 550 ENGINE REBUILDING 10 11 3 4 12 13 5 2 14 1 16 15 16 9 17 6 7 8...
Page 156: ...7 12 CLUTCHING 1 1 2 3 4 5 6 7 18 17 10 8 9 13 12 11 15 16 14...
Page 192: ...8 20 FINAL DRIVE...
Page 200: ...10 2 FRONT SUSPENSION STEERING FUSION IQ RMK 600 RMK Fusion 14 78...
Page 201: ...10 3 FRONT SUSPENSION STEERING EDGE RMK Apply Polaris All Season Grease to all zerks...
Page 202: ...10 4 FRONT SUSPENSION STEERING 42 5 EDGE Apply Polaris All Season Grease to all zerks...
Page 203: ...10 5 FRONT SUSPENSION STEERING WIDETRAK Apply Polaris All Season Grease to all zerks...
Page 244: ...11 28 REAR SUSPENSION...
Page 256: ...12 12 CHASSIS HOOD...
Page 282: ...13 26 ELECTRICAL...
Page 288: ...13 32 ELECTRICAL...
Page 289: ...14 1 WIRE DIAGRAM 2006 600 FUSION HO HOOD...
Page 290: ...14 2 WIRE DIAGRAM 2006 HO RMK HOOD...
Page 291: ...14 3 WIRE DIAGRAM 600 HO FUSION RMK CHASSIS...
Page 292: ...14 4 WIRE DIAGRAM 600 HO FUSION RMK CHASSIS CALL OUTS...
Page 293: ...14 5 WIRE DIAGRAM 700 900 ENGINE...
Page 294: ...14 6 WIRE DIAGRAM 700 900 ENGINE AND ENGINE CALL OUTS...
Page 295: ...14 7 WIRE DIAGRAM 700 900 CHASSIS...
Page 297: ...14 9 WIRE DIAGRAM 340 550 FUJI FAN ENGINE CHASSIS...
Page 298: ...14 10 WIRE DIAGRAM 500 FUJI ENGINE CHASSIS...
Page 299: ...14 11 WIRE DIAGRAM 500 600 IBERTY ENGINE CHASSIS...