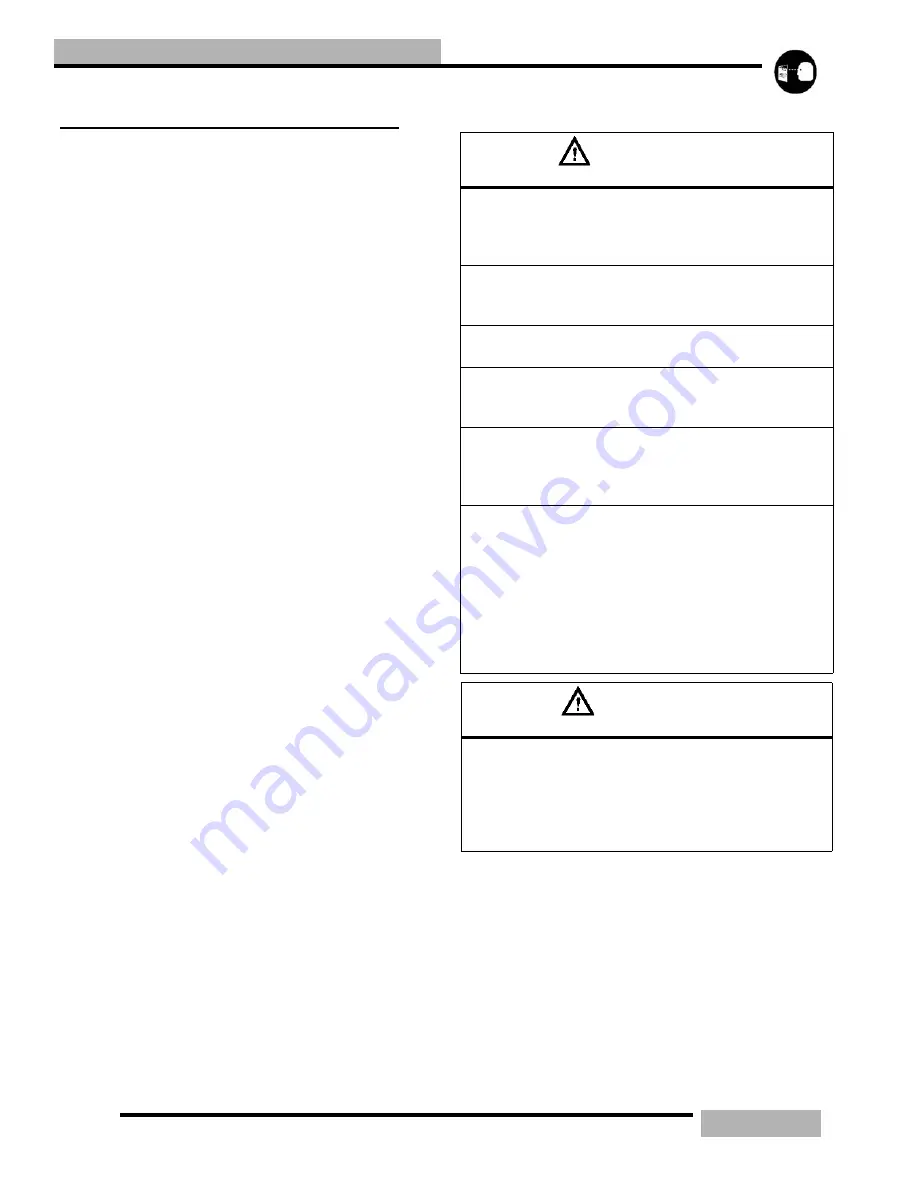
9.2
BRAKES
HYDRAULIC BRAKE SYSTEM
OVERVIEW
The Polaris snowmobile hydraulic brake system consists of
the following components or assemblies: brake lever, master
cylinder, hydraulic hose, brake caliper (slave cylinder), brake
pads, and a brake disc which is secured to the drive line.
When the hand activated brake lever (A) is applied, it contacts
a piston (B) within the master cylinder. As the master cylinder
piston moves inward it closes a small opening called a
compensating port (C) within the cylinder and starts to build
pressure within the brake system. As the pressure within the
system is increased, the pistons (D) located in the brake
caliper move toward the disc and applies pressure to the
moveable brake pads. As the lever pressure is increased, the
braking effect is increased.
The friction applied to the brake pads will cause the pads to
wear. As the pads wear, the piston within the caliper self-
adjusts and moves further outward.
Brake fluid level is critical to proper system operation. A low
fluid level allows air to enter the system causing the brakes to
feel spongy.
COMPENSATING PORT
Located within the master cylinder is a small compensating
port (C) which is opened and closed by the master cylinder
piston assembly. The port is open when the brake lever is
released and the piston is outward. As the temperature within
the hydraulic system changes, this port compensates for fluid
expansion caused by heat, or contraction caused by cooling.
During system service, be sure this port is open. Due to the
high temperatures created within the system during heavy
braking, it is very important that the master cylinder reservoir
have adequate space to allow for the brake fluid to expand.
Master cylinder reservoirs should be filled to the top of the
fluid level mark on the inside of the reservoir, 1/4” - 5/16” (.6
-.8 cm) below lip of reservoir opening.
This system also incorporates a diaphragm (E) as part of the
cover gasket and a vent port (F) located between the gasket
and the cover. The combination diaphragm and vent allow for
the air above the fluid to equalize pressure as the fluid
expands or contracts. Be sure the vent is open and allowed to
function. If the reservoir is overfilled or the diaphragm vent is
plugged, the expanding fluid may build pressure in the brake
system and lead to brake failure.
GENERAL GUIDELINES
Keep these points in mind when bleeding hydraulic brakes:
• The master cylinder reservoirs have limited capacities.
It is easy to empty them during the bleeding procedure.
This introduces air into the system which you are trying
to purge. Watch the reservoir closely and add fluid
when necessary to prevent air from entering the system.
• Apply only light to moderate pressure to the lever or
pedal when bleeding the brake system. Extreme
pressure will cause a surge of fluid through the small
orifices of the brake system when the bleeder screw is
opened and introduce air into the system by means of
cavitation.
WARNING
Contaminated brake discs or brake pads greatly reduce
braking performance and increase stopping distance.
Do not attempt to clean contaminated pads. Replace
them. Clean the brake disc with brake cleaner.
This brake system requires ethylene-glycol based fluid
(DOT 4). Do not use or mix different types of fluid such
as silicone-based or petroleum-based.
Do not use brake fluid taken from old, used or unsealed
containers. Never reuse brake fluid.
Keep brake fluid tightly sealed and out of reach of chil-
dren. Brake fluid can accumulate moisture, reducing it's
effectiveness.
A soft, spongy feeling in the brake lever and/or brake
pedal could indicate a hazardous condition in the brake
system. Do not operate the motorcycle until the failure
in the brake system is corrected.
An unsafe condition exists when air is trapped in the hy-
draulic brake system. Air in the brake hydraulic system
acts like a soft spring and absorbs a large percentage
of the pressure developed by the master cylinder. With-
out this pressure, the braking system cannot develop
full braking force to allow for safe, controlled stops. It is
extremely important to bleed the brakes properly after
any brake system work has been performed or when in-
spection reveals spongy brakes.
CAUTION
Pressure bleeding is not recommended. When fluid
surges through the fittings, it is possible to cavitate the
fluid and create air in the system. In addition, the fluid
stored in a pressure bleeder may be contaminated. Al-
ways use fresh DOT 4 brake fluid from a sealed con-
tainer.
Summary of Contents for SUPERSPORT 2006
Page 48: ...NOTES SPECIFICATIONS 1 48...
Page 55: ...2 7 GENERAL SAE TAP DRILL SIZES METRIC TAP DRILL SIZES DECMIAL EQUIVALENTS...
Page 60: ...2 12 GENERAL SPECIAL TOOLS...
Page 61: ...2 13 GENERAL...
Page 62: ...2 14 GENERAL...
Page 106: ...4 18 CARBURETION...
Page 139: ...6 27 ENGINE 340 550 ENGINE REBUILDING 10 11 3 4 12 13 5 2 14 1 16 15 16 9 17 6 7 8...
Page 156: ...7 12 CLUTCHING 1 1 2 3 4 5 6 7 18 17 10 8 9 13 12 11 15 16 14...
Page 192: ...8 20 FINAL DRIVE...
Page 200: ...10 2 FRONT SUSPENSION STEERING FUSION IQ RMK 600 RMK Fusion 14 78...
Page 201: ...10 3 FRONT SUSPENSION STEERING EDGE RMK Apply Polaris All Season Grease to all zerks...
Page 202: ...10 4 FRONT SUSPENSION STEERING 42 5 EDGE Apply Polaris All Season Grease to all zerks...
Page 203: ...10 5 FRONT SUSPENSION STEERING WIDETRAK Apply Polaris All Season Grease to all zerks...
Page 244: ...11 28 REAR SUSPENSION...
Page 256: ...12 12 CHASSIS HOOD...
Page 282: ...13 26 ELECTRICAL...
Page 288: ...13 32 ELECTRICAL...
Page 289: ...14 1 WIRE DIAGRAM 2006 600 FUSION HO HOOD...
Page 290: ...14 2 WIRE DIAGRAM 2006 HO RMK HOOD...
Page 291: ...14 3 WIRE DIAGRAM 600 HO FUSION RMK CHASSIS...
Page 292: ...14 4 WIRE DIAGRAM 600 HO FUSION RMK CHASSIS CALL OUTS...
Page 293: ...14 5 WIRE DIAGRAM 700 900 ENGINE...
Page 294: ...14 6 WIRE DIAGRAM 700 900 ENGINE AND ENGINE CALL OUTS...
Page 295: ...14 7 WIRE DIAGRAM 700 900 CHASSIS...
Page 297: ...14 9 WIRE DIAGRAM 340 550 FUJI FAN ENGINE CHASSIS...
Page 298: ...14 10 WIRE DIAGRAM 500 FUJI ENGINE CHASSIS...
Page 299: ...14 11 WIRE DIAGRAM 500 600 IBERTY ENGINE CHASSIS...