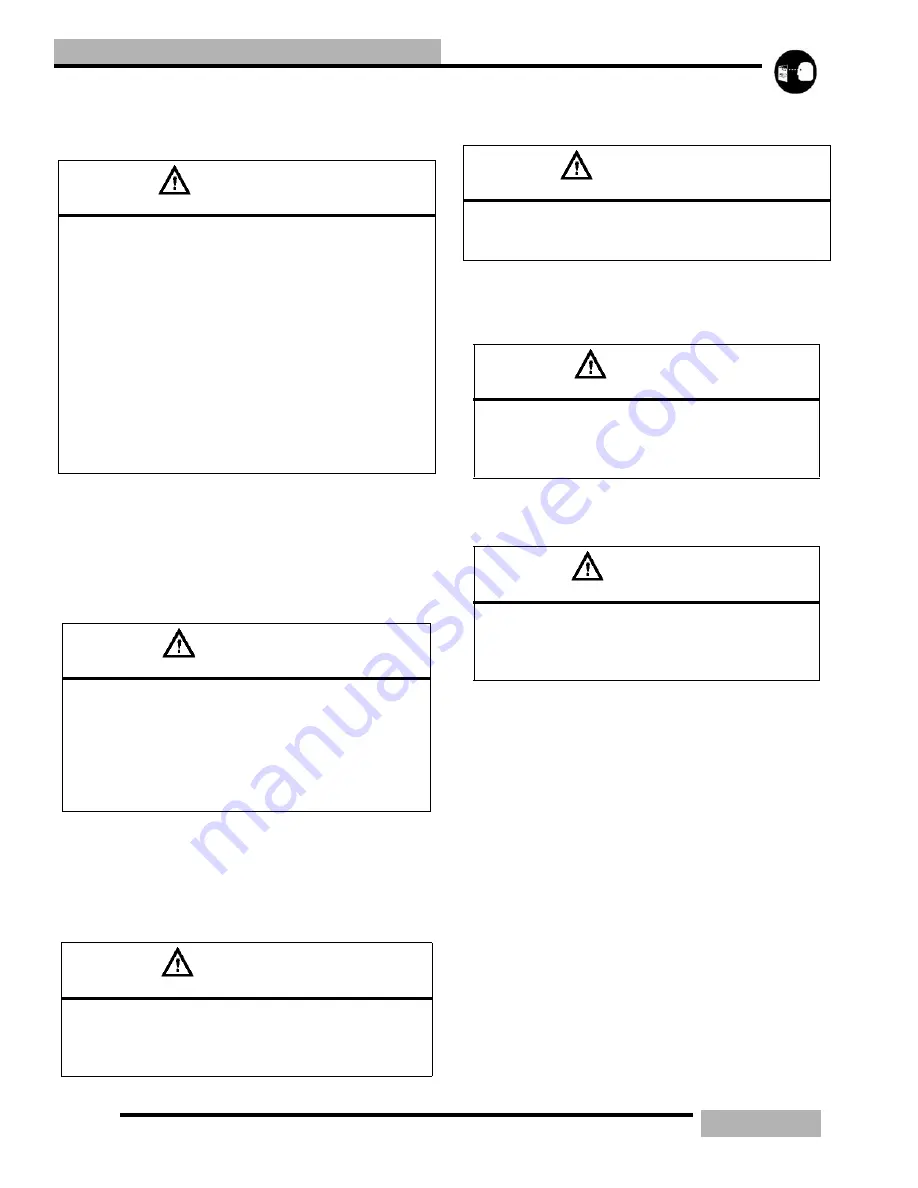
11.24
REAR SUSPENSION
rebuilding are also available. Monotube shocks 9917736,
Remote Reservoir 9917737.
RYDE FX MONO-TUBE SHOCK
DISASSEMBLY
Procedures for the proper disassembly and assembly of
RydeFX gas charged IFP and emulsion mono-tube shock
absorbers.
1.
Remove the shock(s) from the vehicle.
2.
Before unscrewing pre-load springs, measure the
compressed length of the installed spring and mark
position for reinstallation.
3.
If the shock incorporates a spring, remove the spring and
all collateral retainers.
4.
Wash the shock body in parts cleaner; then dry with
compressed air to remove sand and dirt.
5.
Remove bearing, sleeve and/or bushings from lower shock
mount eyelet. Secure the lower mount of the shock in a
vise. The use of soft jaws is recommend to prevent damage
or marks to the shock.
6.
Remove the small button head screw from the pressure
valve assembly.
7.
Depressurize the shock.
8.
Internal Floating Piston Shocks, using a slotted
screwdriver, loosen the pressure valve assembly counter-
clockwise two full revolutions allowing the gas pressure to
fully escape past the pressure valve assembly O-ring.
9.
Emulsion Shocks: With the shock inverted and the piston
rod fully extended, secure the lower mount of the shock in
a vise. Allow a couple of minutes for the gas pressure to
separate from the oil and rise to the top. Using a rag as a
shield to prevent spraying gas and oil; place rag over top
the pressure valve assembly and slowly loosen the valve
assembly with slotted screw driver three full revolutions,
allowing all the gas pressure to escape past the pressure
valve assembly O-ring.
10. Allow all the gas pressure to escape before proceeding
with the removal of the pressure valve assembly.
Pressurized gas and shock oil could eject the valve
assembly from the cylinder resulting in bodily injury.
11. Using a slotted screwdriver, remove the pressure valve
assembly from the lower end mount. Account for an O-
ring.
12. Using an adjustable face spanner (PN PS45262), fully
CAUTION
E
XTREME
CAUTION
SHOULD
BE
OBSERVED
WHILE
HANDLING
AND
WORKING
WITH
HIGH
PRESSURE
SERVICE
EQUIPMENT
.
W
EAR
A
FACE
SHIELD
,
SAFETY
GLASSES
,
AND
EAR
PROTEC
-
TION
DURING
SERVICE
OF
THESE
SHOCKS
. C
ARE
SHOULD
BE
OBSERVED
WHILE
HANDLING
THE
INFLATER
NEEDLE
AND
PRESSURE
GAUGES
. M
AINTAIN
YOUR
EQUIPMENT
AND
KEEP
IT
IN
GOOD
WORKING
CONDITION
. I
F
INJURY
SHOULD
OCCUR
,
CONSULT
A
PHYSICIAN
IMMEDIATELY
. E
XTREME
CLEANLI
-
NESS
IS
OF
UTMOST
IMPORTANCE
DURING
ALL
DISASSEMBLY
AND
REASSEMBLY
OPERATIONS
TO
PREVENT
ANY
DIRT
OR
FOREIGN
PARTICLES
FROM
GETTING
INTO
THE
SHOCKS
.
K
EEP
THE
PARTS
IN
ORDER
AS
THEY
ARE
DISASSEMBLED
.
N
OTE
THE
DIRECTION
AND
POSITION
OF
ALL
INTERNAL
PARTS
FOR
REASSEMBLY
.
CAUTION
B
EFORE
SERVICING
A
GAS
SHOCK
IT
IS
IMPORTANT
THAT
ALL
THE
GAS
PRESSURE
BE
DISCHARGED
FROM
THE
UNIT
.
R
EFER
TO
THE
INSTRUCTIONS
LISTED
BELOW
FOR
THE
PROPER
PROCEDURE
OF
DISCHARGING
THE
GAS
PRES
-
SURE
FROM
A
SHOCK
. P
ROTECTIVE
EYE
WEAR
SHOULD
BE
WORN
TO
AVOID
RISK
OF
INJURY
WHILE
SERVICING
R
Y
-
DE
FX
GAS
CHARGED
MONO
-
TUBE
SHOCKS
.
CAUTION
W
HEN
REMOVING
THE
SPRING
FROM
A
SHOCK
THAT
UTILIZ
-
ES
A
FIXED
LOWER
RETAINER
;
THE
USE
OF
A
PROPER
SPRING
COMPRESSOR
SHOULD
BE
USED
TO
AVOID
RISK
OF
BODILY
INJURY
.
WARNING
W
HEN
USING
COMPRESSED
AIR
TO
DRY
COMPONENTS
,
PROTECTIVE
EYE
WEAR
SHOULD
BE
WORN
TO
AVOID
RISK
OF
INJURY
.
CAUTION
I
T
IS
IMPORTANT
THAT
THE
GAS
SHOCK
BE
RETAINED
IN
THE
VISE
BY
THE
LOWER
MOUNT
. A
NY
OTHER
METHOD
OF
SECURING
THE
CHOCK
BODY
DURING
THESE
PRO
-
CEDURES
MAY
DEFORM
THE
SHOCK
BODY
CYLINDER
.
WARNING
N
ITROGEN
GAS
IS
UNDER
EXTREME
PRESSURE
.
USE
CAUTION
WHEN
RELEASING
NITROGEN
GAS
FROM
SHOCK
. P
ROTECTIVE
EYE
WEAR
SHOULD
BE
WORN
TO
AVOID
RISK
OF
INJURY
.
Summary of Contents for SUPERSPORT 2006
Page 48: ...NOTES SPECIFICATIONS 1 48...
Page 55: ...2 7 GENERAL SAE TAP DRILL SIZES METRIC TAP DRILL SIZES DECMIAL EQUIVALENTS...
Page 60: ...2 12 GENERAL SPECIAL TOOLS...
Page 61: ...2 13 GENERAL...
Page 62: ...2 14 GENERAL...
Page 106: ...4 18 CARBURETION...
Page 139: ...6 27 ENGINE 340 550 ENGINE REBUILDING 10 11 3 4 12 13 5 2 14 1 16 15 16 9 17 6 7 8...
Page 156: ...7 12 CLUTCHING 1 1 2 3 4 5 6 7 18 17 10 8 9 13 12 11 15 16 14...
Page 192: ...8 20 FINAL DRIVE...
Page 200: ...10 2 FRONT SUSPENSION STEERING FUSION IQ RMK 600 RMK Fusion 14 78...
Page 201: ...10 3 FRONT SUSPENSION STEERING EDGE RMK Apply Polaris All Season Grease to all zerks...
Page 202: ...10 4 FRONT SUSPENSION STEERING 42 5 EDGE Apply Polaris All Season Grease to all zerks...
Page 203: ...10 5 FRONT SUSPENSION STEERING WIDETRAK Apply Polaris All Season Grease to all zerks...
Page 244: ...11 28 REAR SUSPENSION...
Page 256: ...12 12 CHASSIS HOOD...
Page 282: ...13 26 ELECTRICAL...
Page 288: ...13 32 ELECTRICAL...
Page 289: ...14 1 WIRE DIAGRAM 2006 600 FUSION HO HOOD...
Page 290: ...14 2 WIRE DIAGRAM 2006 HO RMK HOOD...
Page 291: ...14 3 WIRE DIAGRAM 600 HO FUSION RMK CHASSIS...
Page 292: ...14 4 WIRE DIAGRAM 600 HO FUSION RMK CHASSIS CALL OUTS...
Page 293: ...14 5 WIRE DIAGRAM 700 900 ENGINE...
Page 294: ...14 6 WIRE DIAGRAM 700 900 ENGINE AND ENGINE CALL OUTS...
Page 295: ...14 7 WIRE DIAGRAM 700 900 CHASSIS...
Page 297: ...14 9 WIRE DIAGRAM 340 550 FUJI FAN ENGINE CHASSIS...
Page 298: ...14 10 WIRE DIAGRAM 500 FUJI ENGINE CHASSIS...
Page 299: ...14 11 WIRE DIAGRAM 500 600 IBERTY ENGINE CHASSIS...