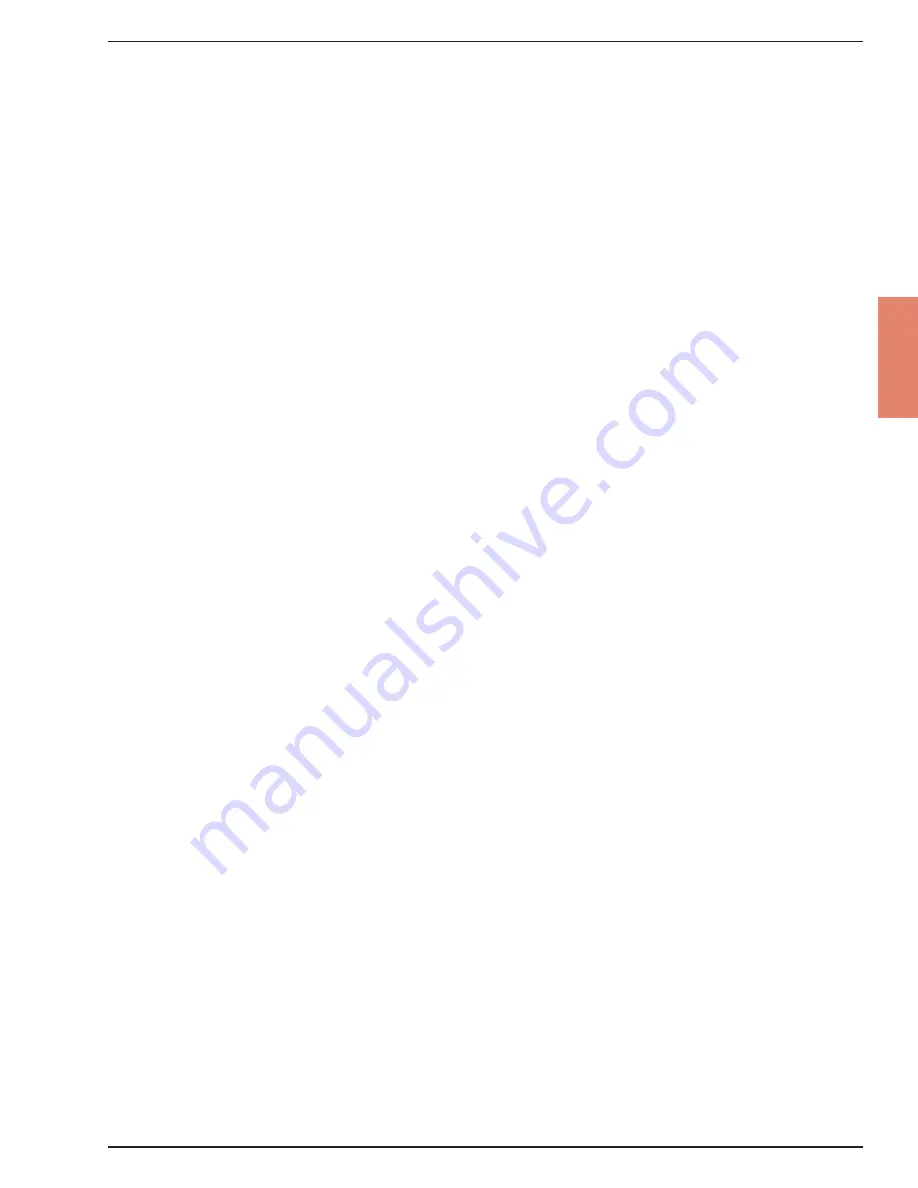
Coral Sea Vertical 6800
Page 2-7
Pre-installa
tion
3. High pressure pump (optional): This is a marine
quality positive displacement ceramic plunger pump
with stainless steel manifold.
4. The pressure relief valve (optional pump) works
in conjunction with a over pressure switch to shut
the System off should over pressure develop. If the
System is over pressurized, the pressure relief valve
will open and allow water pressure to build up at the
pressure switch, which, in turn, opens to shut the
System off.
5. The high pressure hose connects the outlet of the
high pressure pump to the inlet of the pulsation
dampener.
6. The pulsation dampener (optional pump) is of the in
line design and has no repairable parts. The pulsation
dampener is, therefore, maintenance free. The
pulsation dampener assists the high pressure pump
in delivering a smooth, pulsation free, supply of water
to the R.O. membrane elements.
7. High pressure protection switch is a normally closed
(N.C.) switch and set to open at 975 psi (67.2 bar).
At 975 psi (67.2 bar), when the high pressure switch
opens, the System will shut off for safety purposes.
8. The high pressure gauge located at the outlet
of the high pressure pump and inlet of the fi rst
R.O. membrane element, is a visual indication of
the pressure created by the high pressure pump
and pressure within the R.O. membrane element
assemblies. The high quality stainless steel gauge
is glycerin oil fi lled for dampening, and provides an
accurate, smooth reading.
9. The fl ow by-pass valve allows for the System to be
started with minimal shock to the R.O. membrane
elements. This valve should be opened at each start
up of the System which allows a large portion of
the feed water to by-pass the R.O. Membrane and
discharge back to the feed water. This helps protect
the membrane from the sudden thrust of water at
each start up and, in turn, prolong the life of the R.O.
membrane element.
10. Sea Recovery’s R.O. membrane & vessel assemblies
consists of an exclusive, and unique, high pressure,
an corrosion resistant vessel, which houses two
or three special spiral wound reverse osmosis
membrane element. The R.O. membrane elements
reject the salt ions present in the feed water, yet
allow the potable H2O molecules to pass through the
thin membrane surface. A suffi cient fl ow of water
across the membrane surface must be continually
in progress in order for the correct percentage of
salt rejection to occur. Only about 5 to 10% (sea
water systems, per individual membrane element)
of the system feed water becomes fresh product
water. The remainder, becomes a concentrated brine
solution which carries rejected salt ions away from
the membrane element and back to the feed water
source. The proper fl ow of water is also essential
to minimize fouling of the R.O. membrane element.
Reducing the fl ow of feed water, would cause the
R.O. membrane element to recover a higher
percentage of the feed water. Excessive recovery,
would rapidly foul the membrane.
11. High pressure lines transfer pressurized seawater
from the pulsation dampener to the fi rst SRC R.O.
membrane element vessel assembly, between R.O.
membrane element vessel assemblies and from the
last SRC R.O. membrane element vessel assembly
to the back pressure regulator assembly. These lines
are constructed of a special high grade stainless steel
alloy.
12. The pressure by-pass valve must be open at each
start up and during system storage or membrane
cleaning cycles in order to relieve all pressure at the
R.O. membrane element. The valve must be closed
for normal operation.
13. The high pressure gauge located at the outlet of the
R.O. membrane vessel assemblies and inlet of the
back pressure regulator valve, is a visual indication of
the differential pressure between the R.O. membrane
vessel assemblies. Proper correlation of this pressure
gauge to pressure gauge [46] will allow the operator
to determine R.O. membrane element fouling and
the necessity for cleaning of the R.O. membrane
elements.
14. Back pressure regulator valve is of 316 Stainless
Steel construction. By turning the valve handle
clockwise, a smaller orifi ce is created and this
results in pressure build up. By turning the valve
handle clockwise and counter clockwise pressure is
increased and decreased accordingly, which in turn
increases and decreases System operating pressure
and productivity of the R.O. membrane element(s).
E. BRINE DISCHARGE SUBSYSTEM:
This section of the System carries the Brine Discharge
expelled from the R.O. Membrane Element back to the
feed source.
1. The pressure gauge at the brine discharge line
allows the operator to determine if there is any
obstruction on the brine discharge line. This line must
be kept free and clear of any blockages so that the
brine water discharges with minimal pressure and
restriction.
2. Brine discharge pressure switch is a normally closed
switch and set at 70 psi (4.8 bar) when the brine
disharge pressure exceeds 70 psi, the PLC will
Coral Sea Owner's Manual
Summary of Contents for Coral Sea
Page 3: ...SECTION 1 SYSTEM DESCRIPTION Coral Sea Owner s Manual...
Page 14: ...SECTION 2 PRE INSTALLATION NOTES Coral Sea Owner s Manual...
Page 25: ...SECTION 3 ELECTRICAL INFORMATION Coral Sea Owner s Manual...
Page 28: ...SECTION 4 INSTALLATION REQUIREMENTS Coral Sea Owner s Manual...
Page 35: ...SECTION 5 OPERATIONS MANUAL Coral Sea Owner s Manual...
Page 36: ...Operation THIS PAGE INTENTIONALLY LEFT BLANK Coral Sea Owner s Manual...
Page 166: ...Intentionally Left Blank Coral Sea Owner s Manual...
Page 167: ...SECTION 6 R O MEMBRANE INSTALL CARE Coral Sea Owner s Manual...
Page 193: ...SECTION 7 MAINTENANCE AND REPAIR Coral Sea Owner s Manual...
Page 194: ...Maintenance Coral Sea Owner s Manual...
Page 203: ...SECTION 8 COMPONENT USER MANUALS Coral Sea Owner s Manual...
Page 204: ...Page Intentionally Left Blank Coral Sea Owner s Manual...
Page 215: ...SECTION 9 DRAWING PULL OUTS Coral Sea Owner s Manual...
Page 216: ...Page Left Intentionally Blank Coral Sea Owner s Manual...
Page 247: ...SECTION 10 SPARE PARTS LIST Coral Sea Owner s Manual...