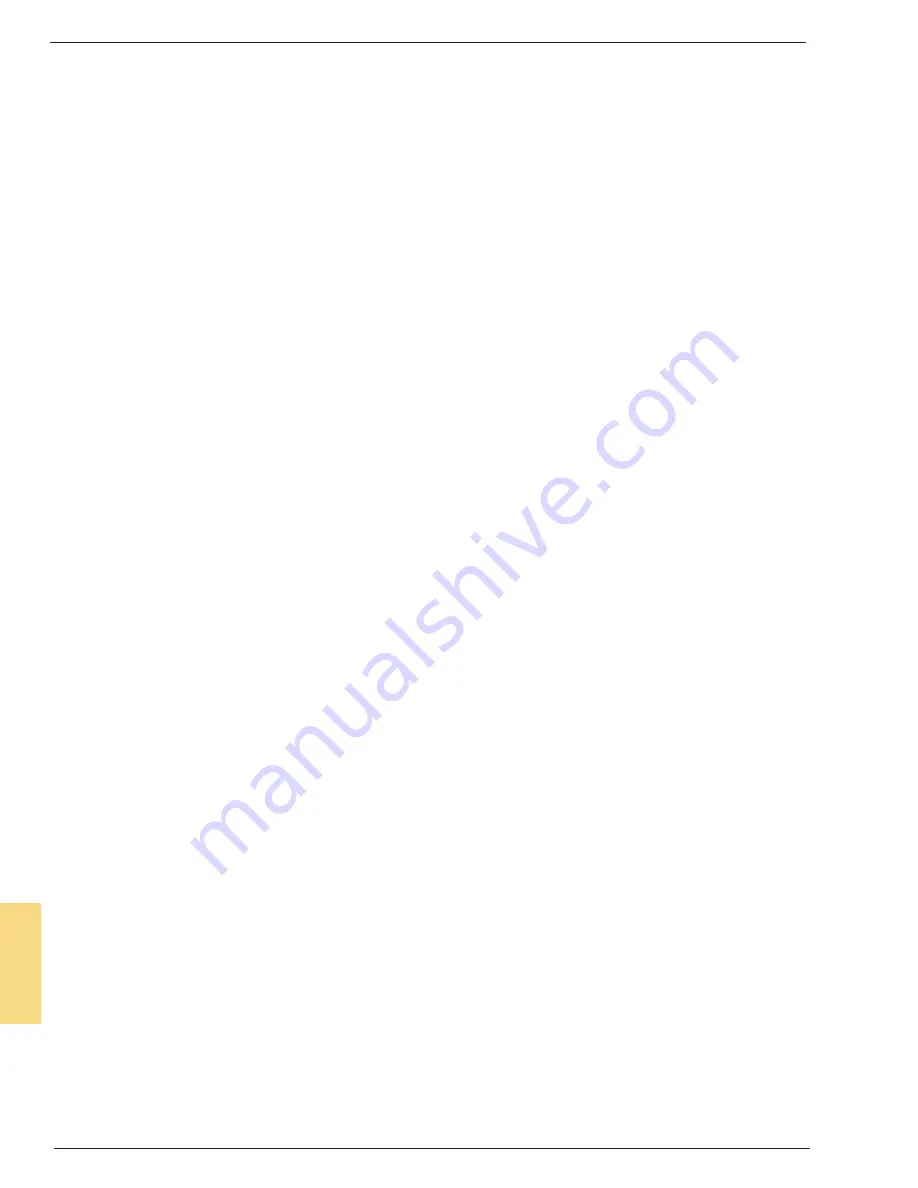
Coral Sea Vertical 6800
Page 7-4
Maintenance
pressure the switch may be recalibrated.
a. Remove the calibration sealing cap located in the
center top of the pressure switch canister to expose
the calibration hole and calibration screw.
b. Insert a medium size fl at blade screwdriver into
the calibration hole. Adjust the calibration screw
maximum 1/8 th turn (45 degrees) at a time clockwise
to increase the set point or counter clockwise to
decrease the set point as appropriate to adjust the
switch.
c. Repeat this procedure as necessary to properly
calibrate the switch.
7.5 PRESSURIZATION SUBSYSTEM
1. HP Pump (standard): Refer to Danfoss APP Pump
instructions in Appendix A.
2. High-pressure pump (optional): Parker Hannifi n
Positive Displacement Split Manifold Plunger Pump
(see below).
a. Servicing the valves:
1) Disassembly:
a) Remove the 6 M41 Hex Valve Plugs.
b) Using standard pliers, remove the valve retainer by
grasping the top tab. The valve assembly should
remain together. If the assembly separates, the parts
will lift out without any tools.
c) Remove the O-Ring in the groove at the bottom of the
valve chamber.
d) Inspect machined sealing surfaces on manifold. If
pitting is present replace manifold.
2) Reassembly:
a) Examine the O-Rings and back-up rings on the seat
and replace if cut or worn. Lubricate the O-Ring with
silicone based O-Ring lubricant before installing the
valve and seat.
b) Examine the surface of the valve seat for pitting,
grooves or wear and replace if necessary.
c) Assemble valve retainer, spring, valve and seat by
snapping together securely.
d) Lubricate outer O-Ring and back-up ring surface and
walls of valve chamber with silicone based O-Ring
lubricant and press valve assembly squarely into
chamber.
e) Examine the O-Ring and back-up ring on the valve
plug and replace if cut or worn.
Lubricate new O-Ring and back-up ring with silicone
based O-Ring lubricant before
installing on plug to avoid damaging as they are
worked over the plug threads.
k) Install impeller onto motor shaft being careful to align
key way of impeller with key way in motor shaft. Be
careful seal spring retainer fi ts inside lip of impeller
hub. Push impeller on until impeller bottoms out on
shaft sleeve.
l) Install new impeller lock screw gasket into impeller
lock screw. Install impeller lock screw into motor shaft
and tighten.
m) Return pump to motor and install using new gasket
and tighten 8 volume bolts evenly.
n) Jog the motor with the feed water pump switch (SW-
1) to ensure free rotation.
5. Pretreatment tank: As the tank gets dirty, clean it with
product water and a brush or cloth.
6. Pretreatment pump: The pretreatment pump may
be repaired as per the instructions supplied with the
pump.
7.4 LOW-PRESSURE PRE-FILTRATION
SUBSYSTEM
1. Multi-Media Filter: As required perform multi media
backwashing per
Section 7.2
2. Flow Meters: Since the fl ow meter bodies are
clear acrylic, light can penetrate them and support
biological growth within. In order to gain access for
cleaning of the fl ow meter body, fi rst loosen the union
locking rings then remove the body. To clean the fl ow
meter body, pull a wetted soft cloth back and forth
through it.
3. Cartridge pre-fi lter element replacement: The pre-
fi lter elements must be replaced when plugged
to the extent that the high-pressure pump is not
receiving a positive head and the lowpressure switch
is activating and stopping the system due to low feed
water pressure to the highpressure pump. Determine
if both the 25 and/or just the 5 micron pre-fi lter
elements are fouled by reviewing the feed line
pressure gauge readings. The pressure differential
reading across these gauges will determine which or
if both stages of the cartridge pre-fi lters are fouled
and require replacement. Proceed as follows for
the respective pre-fi lter element replacement. See
Section onf Component Manuals.
4. Pressure gauges: The pressure gauges used in the
Parker Hannifi n R.O. system are non repairable.
Replace the gauge should it loose calibration or
develop a defect or malfunction.
5. Low-pressure switch: The low-pressure switch is
normally open and will close on the rise at the factory
set pressure of approximately 6-10 psi.
Should the pressure setting drift from the factory set
Coral Sea Owner's Manual
Summary of Contents for Coral Sea
Page 3: ...SECTION 1 SYSTEM DESCRIPTION Coral Sea Owner s Manual...
Page 14: ...SECTION 2 PRE INSTALLATION NOTES Coral Sea Owner s Manual...
Page 25: ...SECTION 3 ELECTRICAL INFORMATION Coral Sea Owner s Manual...
Page 28: ...SECTION 4 INSTALLATION REQUIREMENTS Coral Sea Owner s Manual...
Page 35: ...SECTION 5 OPERATIONS MANUAL Coral Sea Owner s Manual...
Page 36: ...Operation THIS PAGE INTENTIONALLY LEFT BLANK Coral Sea Owner s Manual...
Page 166: ...Intentionally Left Blank Coral Sea Owner s Manual...
Page 167: ...SECTION 6 R O MEMBRANE INSTALL CARE Coral Sea Owner s Manual...
Page 193: ...SECTION 7 MAINTENANCE AND REPAIR Coral Sea Owner s Manual...
Page 194: ...Maintenance Coral Sea Owner s Manual...
Page 203: ...SECTION 8 COMPONENT USER MANUALS Coral Sea Owner s Manual...
Page 204: ...Page Intentionally Left Blank Coral Sea Owner s Manual...
Page 215: ...SECTION 9 DRAWING PULL OUTS Coral Sea Owner s Manual...
Page 216: ...Page Left Intentionally Blank Coral Sea Owner s Manual...
Page 247: ...SECTION 10 SPARE PARTS LIST Coral Sea Owner s Manual...