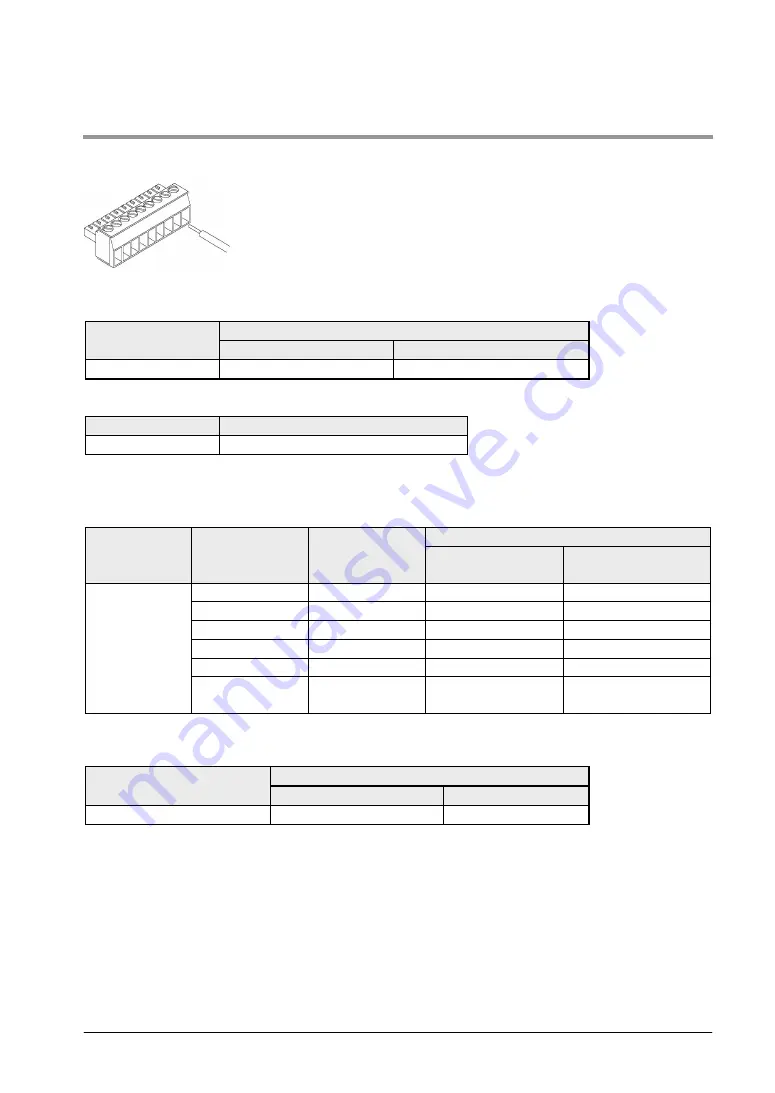
5-13
5.5 Wiring of Terminal Block Type
Attached terminal block/Suitable wires
A screw-down connection type is used for the terminal block. The suitable wires are given below.
Terminal block socket
The terminal socket manufactured by Phoenix Contact is used.
No. of pins
Model No. of Phoenix Contact
Model No.
Product No.
9 pins
MC1,5/9-ST-3,5
1840434
Suitable wires (Twisted wire)
Size
Nominal cross-sectional area
AWG#24 to 16
0.2mm
2
to
1.25mm
2
Pole terminal
If a pole terminal is being used, the following models manufactured by Phoenix Contact Co. should be
used.
Manufacturer Cross-sectional
area (mm
2
)
Size
Part No.
With insulating
sleeve
Without insulating
sleeve
Phoenix
Contact Co.
0.25
AWG #24
AI 0,25 – 6 BU
A 0,25 – 7
0.34
AWG #22
AI 0.34 – 6 TQ
A 0,34 – 7
0.50
AWG #20
AI 0,5 – 6 WH
A 0,5 – 6
0.75
AWG #18
AI 0,75 – 6 GY
A 0,75 – 6
1.00
AWG #18
–
A 1 – 60
0.5
×
2
AWG #20 (for 2
pcs)
AI – TWIN 2
×
0.5 – 8 WH
–
Pressure welding tool for pole terminals
Manufacturer
Model No. of Phoenix Contact
Model No.
Product No.
Phoenix Contact Co.
CRIMPFOX 6
1212034
For tightening the terminal block
When tightening the terminals of the terminal block, use a screwdriver (Product No. 1205037) with a
blade size of 0.4 x 2.5 (Part No. SZS 0,4x2,5).
The tightening torque should be 0.22 to 0.25 N
m (2.3 to 2.5 kgf-cm) or less.
Summary of Contents for FP0R Series
Page 1: ......
Page 6: ...iv ...
Page 14: ...xii ...
Page 15: ...Chapter 1 Functions and Restrictions of the Unit ...
Page 24: ...1 10 ...
Page 25: ...Chapter 2 Specifications and Functions of Control Unit ...
Page 38: ...2 14 ...
Page 39: ...Chapter 3 Expansion ...
Page 45: ...3 7 3 4 Terminal layout diagram Model No Terminal layout diagrams E8RS E8RM E16RS E16RM E8YRS ...
Page 48: ...3 10 ...
Page 49: ...Chapter 4 I O Allocation ...
Page 53: ...Chapter 5 Installation and Wiring ...
Page 73: ...Chapter 6 Preparation of USB Port ...
Page 77: ...6 5 5 Click Finish on the following screen to be displayed ...
Page 79: ...6 7 4 Double click on FP0R 5 Click Update Driver ...
Page 84: ...6 12 ...
Page 85: ...Chapter 7 Communication ...
Page 139: ...7 55 Sample program For Type II Use a program as below to directly specify a MODBUS address ...
Page 141: ...Chapter 8 High speed Counter Pulse Output and PWM Output Functions ...
Page 142: ...8 2 ...
Page 199: ...Chapter 9 Security Functions ...
Page 211: ...Chapter 10 Other Functions ...
Page 217: ...Chapter 11 Self Diagnostic and Troubleshooting ...
Page 227: ...Chapter 12 Precautions During Programming ...
Page 242: ...12 16 ...
Page 243: ...Chapter 13 Specifications ...
Page 254: ...13 12 ...
Page 255: ...Chapter 14 Dimensions and Others ...
Page 262: ...14 8 ...
Page 263: ...Chapter 15 Appendix ...
Page 344: ...15 82 15 7 ASCII Codes ...
Page 346: ......
Page 347: ......
Page 348: ......