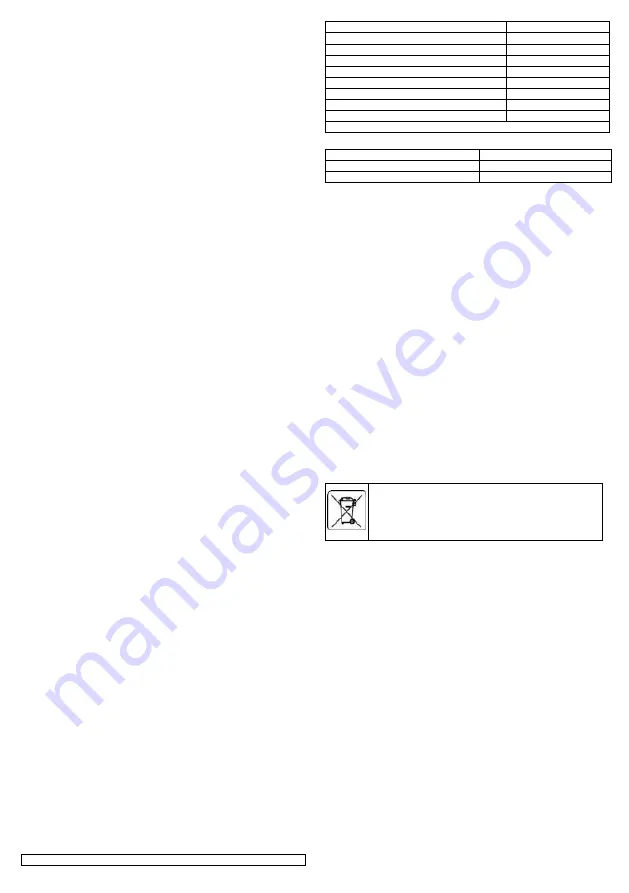
7
Before assembling, disassembling, replacing accessories and before
performing any maintenance, switch off the power source, drain the hose
and disconnect the unit from the hose.
Frequent, but not excessive, lubrication of the unit provides the best
results. Oil introduced into the compressed air connection lubricates the
internal parts of the machine. An automatic oiler is recommended, although
oiling can also be done manually, before starting work and after every hour
of continuous operation of the machine. Only a few drops of oil are applied
at a time. Excess oil could accumulate in the unit and would be blown out
with the exhaust air. ONLY USE OIL INTENDED FOR PNAUMATIC
DEVICES. Do not use oil with detergents or other additives, as this could
cause accelerated wear of the sealing elements used in the unit. Dirt and
water in the supplied air are the main causes of wear on a pneumatic
device. The use of an oiler and air filter on the supply air ensures better
performance and longer life of the pneumatic device. The capacity of the
filter should be matched to the air flow requirements specific to the
equipment.
The pneumatic angle ratchet spanner is not designed to measure torque.
If a connection requires sufficient torque, it should be measured with a
torque spanner after tightening with a pneumatic impact spanner.
NOTE: The actual torque is directly related to the hardness of the
connection, the speed, the quality of the connection and the running time
of the tool. Use the simplest possible connection between the tool and the
power source. Each connection absorbs energy and reduces torque.
LUZING
•
Attach a suitably sized cap to the drive end.
•
Set the compressor pressure regulator to a pressure of 6.2 bar. Do
not set the compressor outlet valve to a pressure higher than 6.2 bar.
•
Connect the ratchet angle pneumatic spanner to the hose connected
to the compressor. If a leak is noticed, disconnect the hose and make
the repair.
•
Slide the cap onto the nut to be loosened.
•
Grip the ratchet angle pneumatic spanner securely. Check the
direction of rotation of the spanner. Press the start button, the
spanner starts working. Note: Ensure that the components to be
loosened, nut or bolt, can withstand the torque exerted by the impact
spanner.
•
If the air spanner is unable to loosen the nut, DO NOT increase the
air pressure supplied by the compressor.
•
Do not repeatedly attempt to unscrew the nut with the spanner. In
this case, a different device or a different method of operation must
be used.
•
Once the nut has been loosened, stop the spanner by releasing
pressure on the on-off button and slide the cap off the nut. If the nut
has been loosened completely, remove it from the cap.
TIGHTENING
•
Make sure that the nut or bolt you intend to tighten is capable of
bearing the load that the spanner generates.
•
Screw the nut on as far as it will go by twisting it by hand.
•
Slide the cap onto the nut. Check the direction of rotation of the
impact spanner. Press the on button for the spanner to start working.
•
If the spanner is stopped during tightening, DO NOT increase the air
pressure supplied by the compressor above 6.2 bar.
•
Do not repeatedly attempt to tighten the nut with an impact spanner.
In this case, a different device or a different method of operation must
be used.
•
When the nut has been tightened, the spanner should be removed
together with the socket. The possibility of overloading the threads
of the fasteners must be avoided.
•
If possible, familiarise yourself with the desired tightening torque for
the nut. The final tightening of the nut should be done with a torque
spanner.
CONSERVATION
Ideally, the tool should operate on a mains supply equipped with an air
lubricator. If the spanner is powered without the use of an oiler, it requires
the following maintenance:
Disconnect the ratchet angle pneumatic spanner from the hose. Introduce
a couple of drops of oil for pneumatic devices into the inlet port of the
spanner, before each use of the device or every hour of operation of the
spanner, in case of continuous operation. Introduce a couple of drops of oil
into the key switch mechanism. Press the button a few times to distribute
the oil over the mating surfaces.
Oil with detergents or other additives must not be used, as this risks
accelerating the wear of the seals used in the key.
RATING DATA
Pneumatic ratchet angle spanner 14-012
Parameter
Value
Length
260 mm
No-load speed
180 min
-1
Max. torque
88 Nm
Average air usage
991.1 l/min
Air connection diameter
¼"
Max. operating air pressure
6.2 bar / 90psi
Mass
1.17 kg
Year of production
14-012 indicates both the type and the designation of the machine
NOISE AND VIBRATION DATA
Sound pressure level
L
PA
= 90 dB(A) K= 3dB(A)
Sound power level
L
WA
= 101 dB(A) K= 3dB(A)
Vibration acceleration values
a
h
= 4.05 m/s
2
K= 1.5m/s
2
Information on noise and vibration
The noise emission level of the equipment is described by: the emitted
sound pressure level Lp
A
and the sound power level Lw
A
(where K
denotes measurement uncertainty). The vibrations emitted by the
equipment are described by the vibration acceleration value a
h
(where
K is the measurement uncertainty).
The sound pressure level Lp
A
, the sound power level Lw
A
and the
vibration acceleration value a
h
given in these instructions have been
measured in accordance with EN ISO 11148-6:2012. The vibration level
a
h
given can be used for comparison of equipment and for preliminary
assessment of vibration exposure.
The vibration level quoted is only representative of the basic use of the
unit. If the unit is used for other applications or with other work tools, the
vibration level may change. A higher vibration level will be influenced by
insufficient or too infrequent maintenance of the unit. The reasons given
above may result in increased vibration exposure during the entire
working period.
In order to accurately estimate vibration exposure, it is necessary
to take into account periods when the unit is switched off or when
it is switched on but not used for work. Once all factors have been
accurately estimated, the total vibration exposure may turn out to
be much lower.
In order to protect the user from the effects of vibration, additional safety
measures should be implemented, such as cyclical maintenance of the
machine and working tools, securing an adequate hand temperature
and proper work organisation.
ENVIRONMENTAL PROTECTION
The product should not be disposed of with household waste, but
should be taken to appropriate facilities for disposal. Equipment that
is not recycled poses a potential risk to the environment and human
health.
"Grupa Topex Spółka z ograniczoną odpowiedzialnością" Spółka komandytowa with its
registered office in Warsaw, ul. Pograniczna 2/4 (hereinafter: "Grupa Topex") informs that
all copyrights to the content of this manual (hereinafter: "Manual"), including, among
others. Its text, photographs, diagrams, drawings, as well as its composition, belong
exclusively to Grupa Topex and are subject to legal protection under the Act of 4 February
1994 on Copyright and Related Rights (ie Journal of Laws 2006 No. 90 Poz. 631, as
amended). Copying, processing, publishing, modification for commercial purposes of the
entire Manual and its individual elements, without the consent of Grupa Topex expressed
in writing, is strictly prohibited and may result in civil and criminal liability.
EC Declaration of Conformity
Manufacturer: Grupa Topex Sp. z o.o. Sp.k., Pograniczna 2/4 02-285
Warszawa
Product: Pneumatic angle ratchet spanner
Model: 14-012
Trade name: NEO TOOLS
Serial number
: 00001 ÷ 99999
This declaration of conformity is issued under the sole responsibility of the
manufacturer.
The product described above complies with the following documents:
Machinery Directive 2006/42/EC
And meets the requirements of the standards:
EN ISO 11148-6:2012
This declaration relates only to the machinery as placed on the market and does
not include components
added by the end user or carried out by him/her subsequently.
Name and address of the EU resident person authorised to prepare the technical
dossier:
Signed on behalf of:
Grupa Topex Sp. z o.o. Sp.k.
2/4 Pograniczna Street
02-285 Warsaw
Summary of Contents for 14-012
Page 1: ...1...
Page 8: ...8 Pawe Kowalski TOPEX GROUP Quality Officer Warsaw 2022 07 22 RU 14 012 ISO 11148 4 10 60...
Page 9: ...9 1 2 3 4 5 1 2 3 4 5 1 2 3 4 Oiler 5 6 7 8 LUZING 6 2 6 2...
Page 18: ...18 14 012 ISO 11148 4 Nm 10 Nm 60 Nm...
Page 19: ...19 1 2 3 4 5 1 2 3 4 5 1 2 3 4 Oiler 5 6 7 8 LUZING 6 2 bar 6 2 bar 6 2 bar...