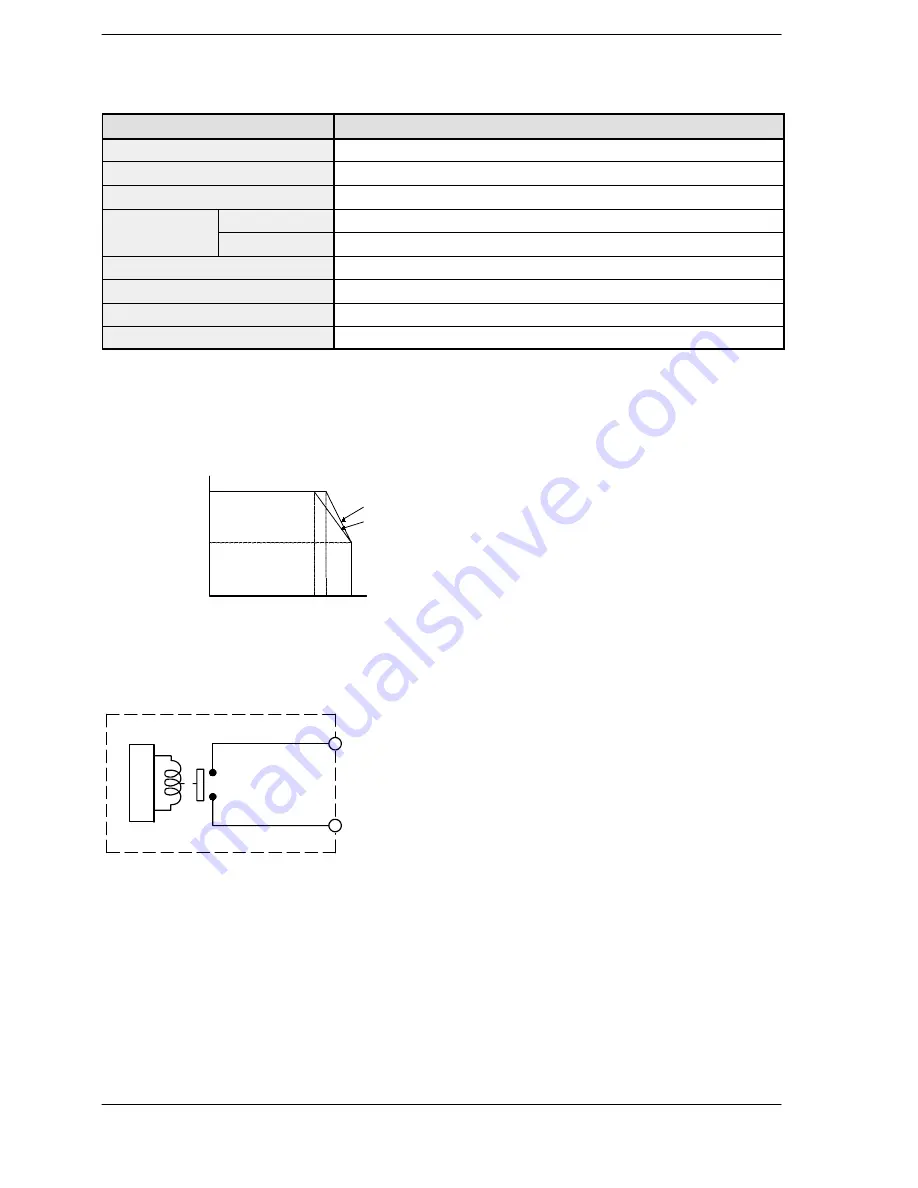
FP
Σ
2.2 Input and Output Specifications
2 - 11
Relay output specifications (for C24R2)
Item
Description
Output type
1a (1 Form A, Normally open)
Rated control capacity
2 A 250 V AC, 2 A 20 V DC (4.5 A per common or later)
Output points per common
8 points/common
Response time
off
→
on
Approx. 10 ms
on
→
off
Approx. 8 ms
Mechanical lifetime
Min. 20,000,000 operations
Electrical lifetime
Min. 100,000 operations
Surge absorber
-
Operating mode indicator
LED display
Limitations on number of simultaneous output on points
Keep the number of output points which are simultaneously on within the following
range as determined by the ambient temperature.
8
46/
107.8
48/
118.4
55/
124
[C24R]
at 24 V DC
at 26.4 V DC
4
Ambient temperature (
°
C/
°
F)
Number of
points per
common
which are
simultaneous
on
Internal circuit diagram
Internal
circuit
Yn
COM
[C24R]
Summary of Contents for FP Series
Page 15: ...FP Functions and Restrictions of the Unit 1 2...
Page 25: ...FP Specifications and Functions of Control Unit 2 2...
Page 37: ...FP Expansion 3 2...
Page 44: ...Chapter 4 I O Allocation 4 1 I O Allocation 4 3...
Page 45: ...FP I O Allocation 4 2...
Page 51: ...FP Installation and Wiring 5 2...
Page 77: ...FP High speed Counter and Pulse Output Functions 6 2...
Page 133: ...FP High speed Counter and Pulse Output Functions 6 58...
Page 135: ...FP Communication Cassette 7 2...
Page 147: ...FP Communication Function 1 Computer Link 8 2...
Page 169: ...FP Communication Function 2 General purpose Serial Communication 9 2...
Page 205: ...FP Communication Function 2 General purpose Serial Communication 9 38...
Page 207: ...FP Communication Function 3 PLC Link Function 10 2...
Page 232: ...Chapter 11 Other Functions 11 1 Analog Potentiometer 11 3 11 2 Clock Calendar Function 11 4...
Page 233: ...FP Other Functions 11 2...
Page 239: ...FP Self Diagnostic and Troubleshooting 12 2...
Page 249: ...FP Self Diagnostic and Troubleshooting 12 12...
Page 251: ...FP Specifications 13 2...
Page 323: ...Index FP I 4...
Page 325: ...FP Record of changes R 2...