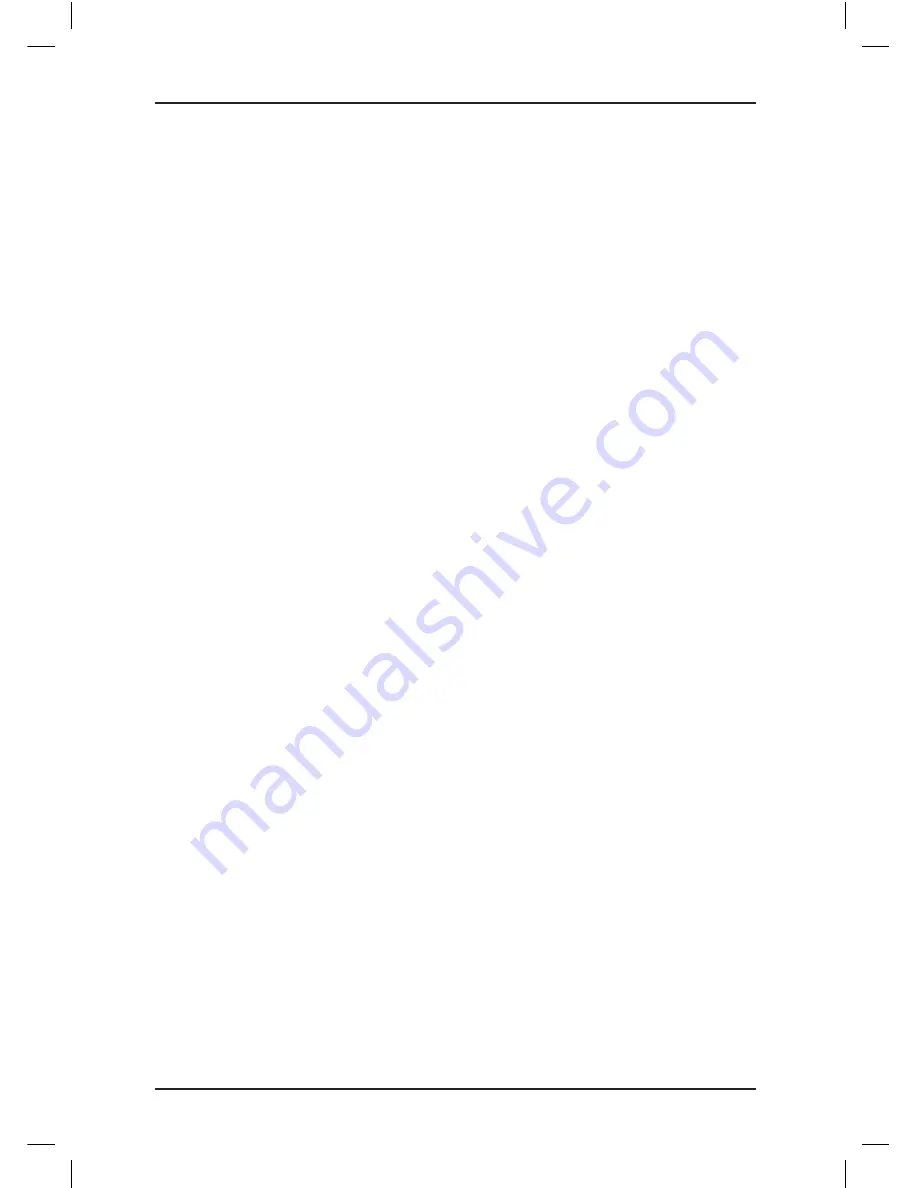
NICE7000 User Manual 5 System Commissioning and Functions
- 81 -
Switchover between synchronous motor and asynchronous motor is implemented easily by
changing F1-25.
Follow the following precautions:
•
Ensure that all wiring and installation meet the safety specifications.
•
Set F1-25 (Motor type) and set motor parameters in group F1 (F1-01 to F1-05) correctly.
Incorrect setting will result in auto-tuning failure.
•
Set FH-01 (Encoder type) and FH-02 (Encoder PPR) correctly. Ensure that the motor is
in CLVC (F0-00 = 1) and distance control (F0-01 = 1) mode.
•
Ensure that the motor wiring is correct (UVW cables of the motor respectively connected
to UVW cables of the controller) for with-load auto-tuning. If the motor wiring is incorrect,
the motor may jitter or fail to run after the brake is released; in this case, you need to
replace any two of the motor UVW cables.
•
Reset the current fault and then start auto-tuning, because the system cannot enter the
auto-tuning state ("TUNE" is not displayed) when there is a fault.
•
Perform motor auto-tuning again if the phase sequence or encoder of the synchronous
motor is changed.
•
For the synchronous motor, perform three or more times of auto-tuning, compare the
obtained values of FH-04 (Encoder initial angle). The value deviation of FH-04 shall be
within ±5°, which indicates that the auto-tuning is successful.
•
After the auto-tuning is completed, perform trial inspection running. Check whether the
current is normal, whether the actual running direction is the same as the set direction.
If the running direction is different from the set direction, change the value of F0-05.
•
With-load auto-tuning is dangerous (inspection-speed running of many control cabinets
is emergency electric running and the shaft safety circuit is shorted). Ensure that there
is no person in the shaft in this auto-tuning mode.
More descriptions of motor auto-tuning are as follows:
•
For synchronous motor, with-load auto-tuning learns stator resistance, shaft-D and
shaft-Q inductance, current loop (including position lock) PI parameters, and encoder
initial angle; no-load auto-tuning additionally learns the encoder wiring mode.
•
For the asynchronous motor, static auto-tuning learns stator resistance, rotor resistance,
and leakage inductance, and automatically calculates the mutual inductance and
motor magnetizing current. Complete auto-tuning learns the mutual inductance, motor
magnetizing current, and current loop parameters.
•
For the synchronous motor, when F1-11 = 3, the controller learns current loop
parameters in motor static state, and the brake is not released.
•
For the asynchronous motor, F1-11 =3 is the same as F1-11 = 1.
•
The controller learns current loop parameters by default during auto-tuning. If the riding
comfort is satisfactory, set FA-12 Bit2 to 1 to cancel self-adaptation of current loop PI
parameters when performing auto-tuning again.
■
Trial Running at Normal Speed
After ensuring that running at inspection speed is normal, perform shaft auto-tuning, ensure
Summary of Contents for NICE7000
Page 1: ......
Page 15: ......
Page 16: ...1 Safety Information and Precautions ...
Page 23: ...1 Safety Information and Precautions NICE7000 User Manual 22 ...
Page 24: ...2 Product Information ...
Page 34: ...3 Mechanical and Electrical Installation ...
Page 71: ...4 Use of the Commissioning Tools ...
Page 79: ...5 System Commissioning and Functions ...
Page 102: ...5 System Commissioning and Functions NICE7000 User Manual 100 ...
Page 103: ...6 Function Code Table ...
Page 134: ...6 Function Code Table NICE7000 User Manual 132 ...
Page 135: ...7 Description of Function Codes ...
Page 205: ...8 Troubleshooting ...
Page 224: ...8 Troubleshooting NICE7000 User Manual 222 ...
Page 225: ...9 EMC ...
Page 234: ...9 EMC NICE7000 User Manual 232 ...
Page 237: ......