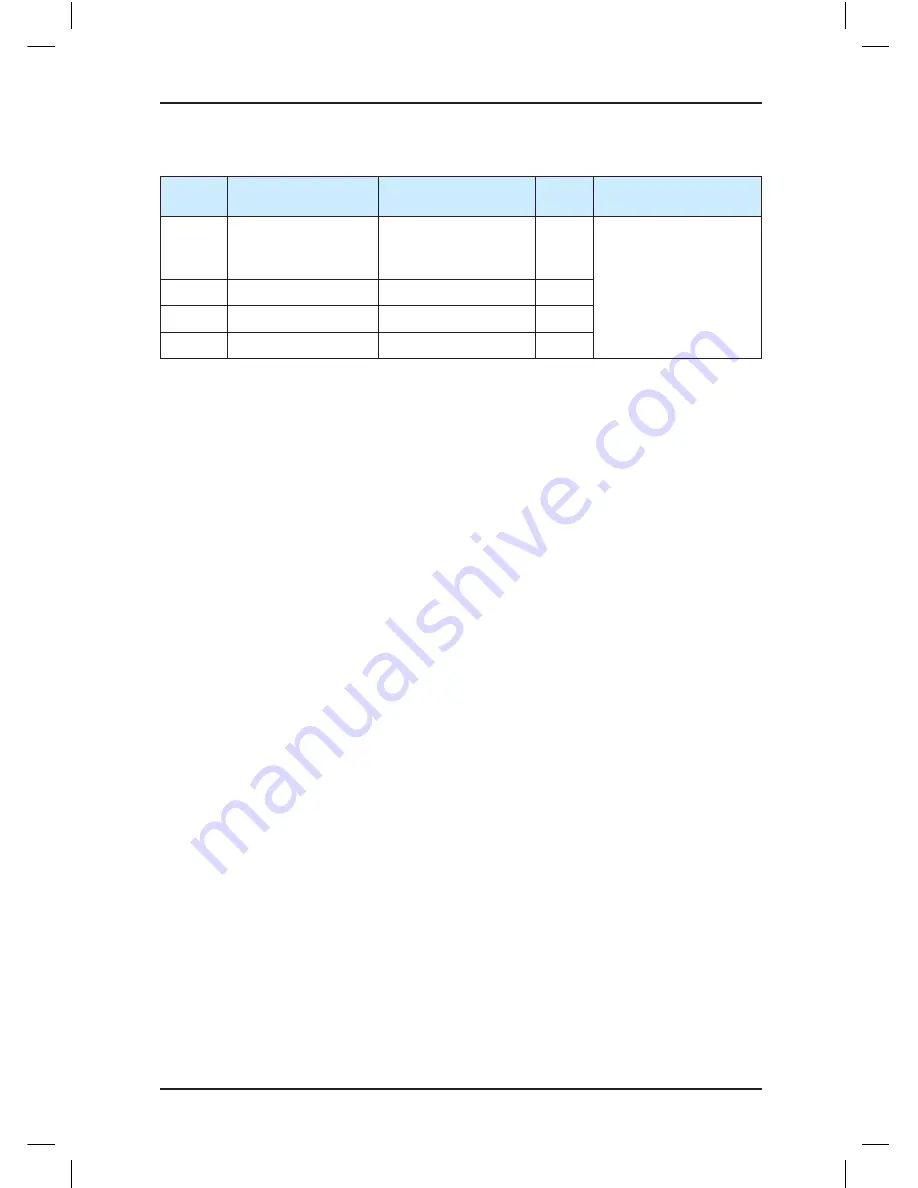
5 System Commissioning and Functions NICE7000 User Manual
- 86 -
d.
Large motor noise indicate excessive values of F2-14/F2-15. Decrease their values.
Function
Code
Parameter Name
Setting Range
Default
Remarks
F8-01
Pre-torque selection
0: Invalid
1: Load call pre-torque
compensation
0
These are pre-torque
regulating parameters.
F8-02
Pre-torque offset
0.0%–100.0%
50.0%
F8-03
Drive gain
0.00–2.00
0.60
F8-04
Brake gain
0.00–2.00
0.60
When F8-01 is set to 1 (Load cell pre-torque compensation), the system with a load cell pre-
outputs the torque matched the load to ensure the riding comfort of the elevator.
•
Motor driving state: full-load up, no-load down
•
Motor braking state: full-load down, no-load up
F8-02 (Pre-torque offset) is actually the elevator balance coefficient, namely, the percentage
of the car load to the rated load when the car and counterweight are balanced.
F8-03 (Drive gain) or F8-04 (Brake gain) scales the elevator’s present pre-torque coefficient
when the motor runs at the drive or brake side.
If the gain set is higher, then the calculated value of startup pro-torque compensation is
higher. The controller identifies the braking or driving state according to the load cell signal
and automatically calculates the required torque compensation value.
When an analog device is used to measure the load, these parameters are used to adjust
the elevator startup. The method of adjusting the startup is as follows:
•
In the driving state, increasing the value of F8-03 could reduce the rollback during the
elevator startup, but a very high value could cause car lurch at start.
•
In the braking state, increasing the value of F8-04 could reduce the jerk in command
direction during the elevator startup, but a very high value could cause car lurch at start.
■
Mechanical Construction
The mechanical construction affecting the riding comfort involves installation of the guide
rail, guide shoe, steel rope, and brake, balance of the car, and the resonance caused by the
car, guild rail and motor. For asynchronous motor, abrasion or improper installation of the
gearbox may arouse poor riding comfort.
1.
Installation of the guide rail mainly involves the verticality and surface flatness of the
guide rail, smoothness of the guide rail connection and parallelism between two guide
rails (including guide rails on the counterweight side).
2. Tightness of the guide shoes (including the one on the counterweight side) also
influences the riding comfort. The guide shoes must not be too loose or tight.
1.
The drive from the motor to the car totally depends on the steel rope. Large flexibility of
the steel rope with irregular resistance during the car running may cause curly oscillation
of the car. In addition, unbalanced stress of multiple steel ropes may cause the car to
jitter during running.
Summary of Contents for NICE7000
Page 1: ......
Page 15: ......
Page 16: ...1 Safety Information and Precautions ...
Page 23: ...1 Safety Information and Precautions NICE7000 User Manual 22 ...
Page 24: ...2 Product Information ...
Page 34: ...3 Mechanical and Electrical Installation ...
Page 71: ...4 Use of the Commissioning Tools ...
Page 79: ...5 System Commissioning and Functions ...
Page 102: ...5 System Commissioning and Functions NICE7000 User Manual 100 ...
Page 103: ...6 Function Code Table ...
Page 134: ...6 Function Code Table NICE7000 User Manual 132 ...
Page 135: ...7 Description of Function Codes ...
Page 205: ...8 Troubleshooting ...
Page 224: ...8 Troubleshooting NICE7000 User Manual 222 ...
Page 225: ...9 EMC ...
Page 234: ...9 EMC NICE7000 User Manual 232 ...
Page 237: ......