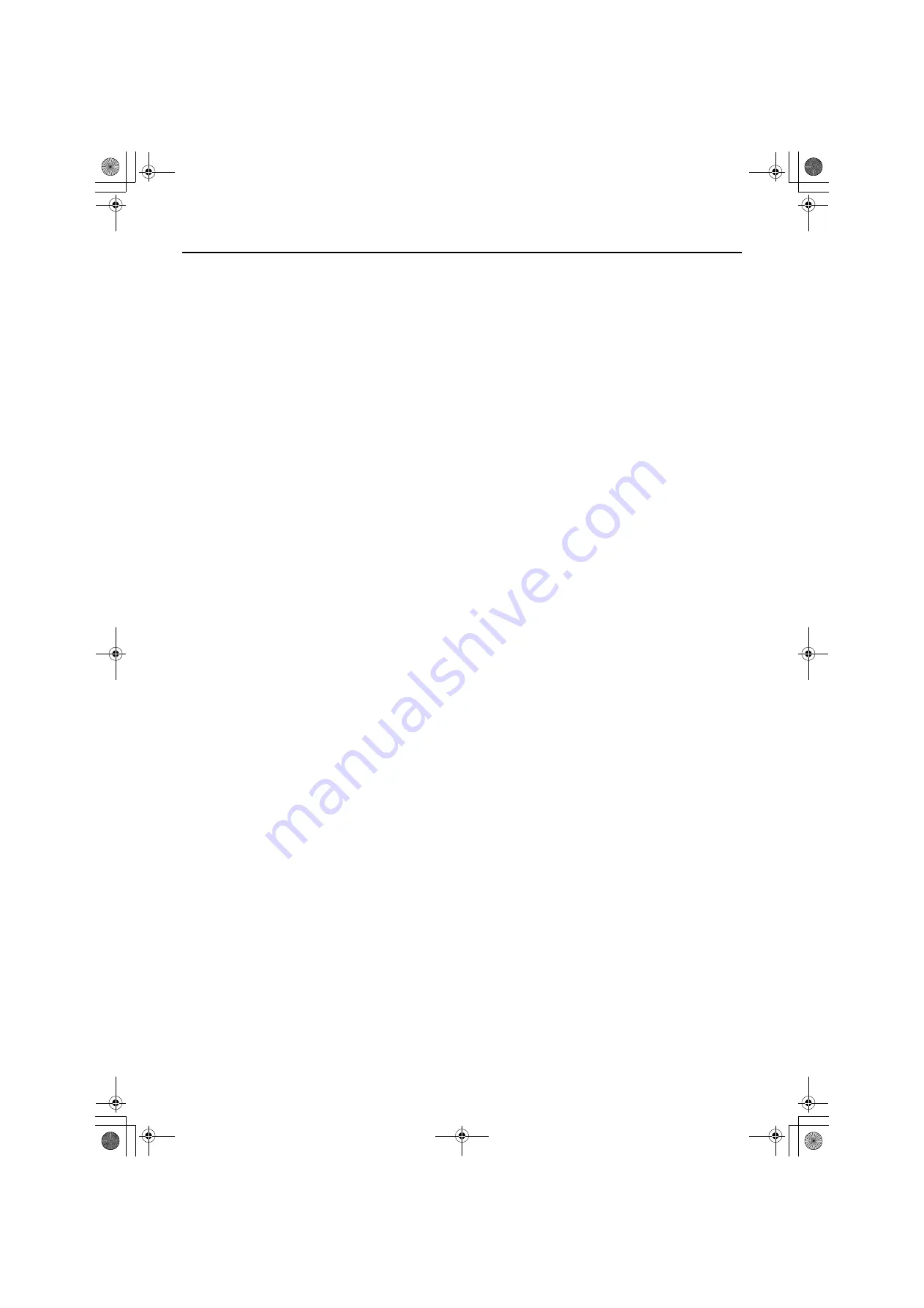
GB_BS_06_C
Chapter 6
Test Run
6-1
Read before Test Run........................................................................................................................... 1
6-2
Operation Characteristics and Refrigerant Charge ........................................................................... 2
6-3
Evaluating and Adjusting Refrigerant Charge ................................................................................... 2
6-3-1
Refrigerant Overcharge and undercharge .............................................................................................. 2
6-3-2
Checking the Refrigerant Charge during Operation................................................................................ 2
6-3-3
Refrigerant Charge Adjustment Mode .................................................................................................... 3
6-4
The Following Symptoms Are Normal ................................................................................................ 5
6-5
Initialization Procedure for System Rotation Settings ...................................................................... 6
0000004496.BOOK 1 ページ 2017年12月26日 火曜日 午前11時45分
Summary of Contents for PFD-P250VM-E
Page 11: ...GB_BS_01_C 0000004491 BOOK 2 ページ 2017年12月26日 火曜日 午後1時10分 ...
Page 27: ...GB_BS_02_C 0000004492 BOOK 2 ページ 2018年1月5日 金曜日 午前10時12分 ...
Page 49: ...GB_BS_03_C 0000004493 BOOK 2 ページ 2018年1月5日 金曜日 午前9時11分 ...
Page 71: ...GB_BS_04_C 0000004494 BOOK 2 ページ 2017年12月26日 火曜日 午前11時43分 ...
Page 89: ...GB_BS_05_C 0000004495 BOOK 2 ページ 2017年12月26日 火曜日 午前11時44分 ...
Page 117: ...GB_BS_06_C 0000004496 BOOK 2 ページ 2017年12月26日 火曜日 午前11時45分 ...
Page 281: ...GB_BS_09_A1 0000004538 BOOK 2 ページ 2017年12月25日 月曜日 午後7時48分 ...
Page 299: ...GB_BS_10_C 0000004550 BOOK 2 ページ 2017年12月26日 火曜日 午後12時1分 ...