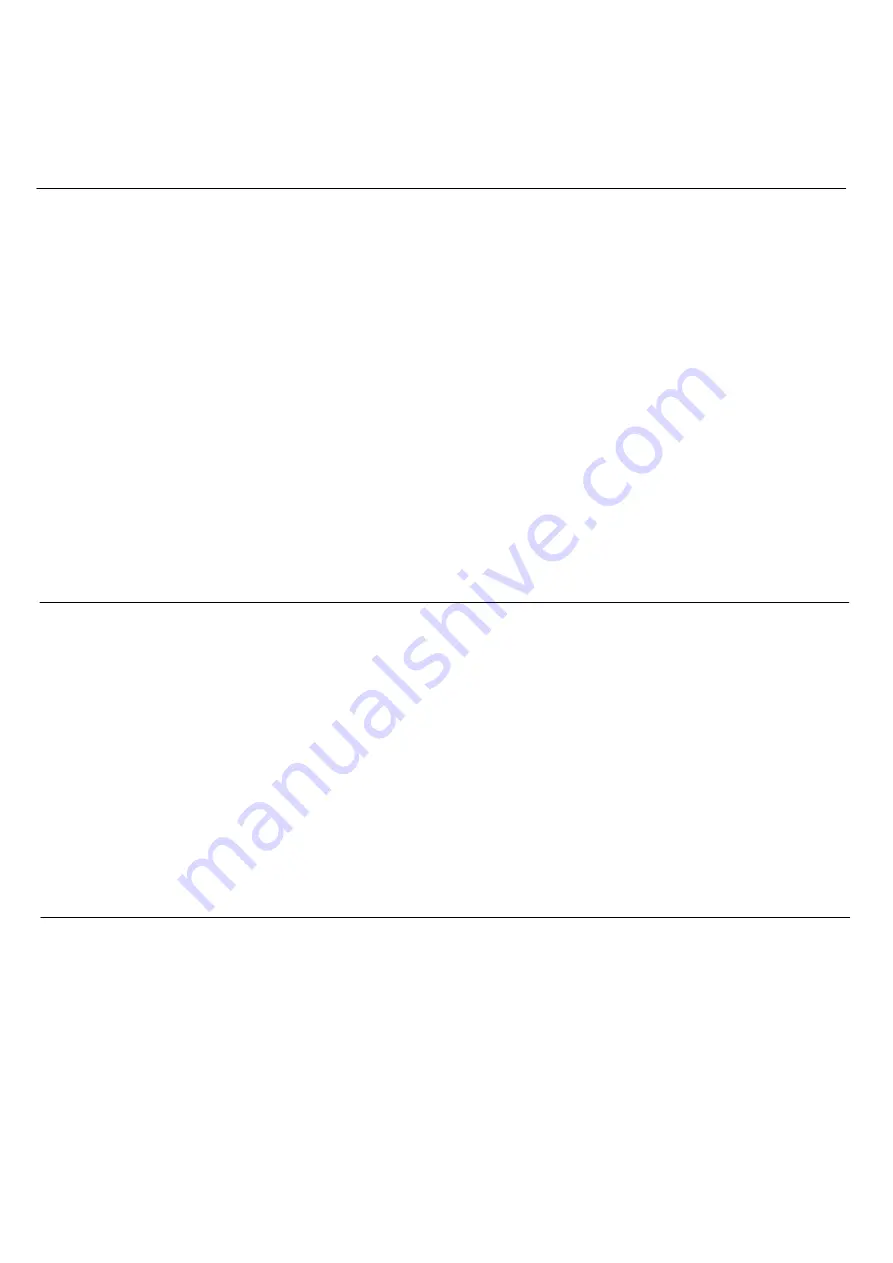
49 / 72
HBC-series V7 LV+MV
P36:
Calibration of the battery temperature sensor
(value in °C)
For easy replacement of the temperature sensor you can make its calibration at any time. If you specify this parameter in the current ambient
temperature in which the sensor is calibrated (of course after stabilization of temperature), write them into the controller and turn-off and back
turn-on the controller. If everything went correctly, the controller after this normally works and you can normally run, drive, etc. with calibrated
temperature sensor. In case some problem occurs, the situation is indicates on the LEDs.
Can be combined with other parameter settings, i.e. including the present battery temperature sensor calibration can be calibrated the motor tem-
perature sensor, see parameter P37.
Caution - for each memory bank be made separately (possible advantage of different sensors for different settings).
P15:
Communication address
Defines controller address for bus (RS 485, CAN, I2C) communication. This address must be different from other bus addresses.
P27:
CAN bus speed
1 Mbit/s
500 kbit/s
250 kbit/s
125 kbit/s
P35:
CAN bus version
CAN 2.0a
CAN 2.0b
P14:
Telemetry
Telemetry protocol definition
off
MZK service
Graupner HoTT
P91:
Baud rate of RS 232 / 485
Communication speed can be set in the range of 10 Bd to 1MBd . Speed is entered directly numerically in baud rate, I.e. 38400 for the standard
rate of 38,400 baud or 9600 for 9600 baud, etc..
For optically isolated RS 232 TTL speed limit a
pplies to a maximum of 2400 baud. If the line is not optically isolated, restrictions don´t apply. For
RS-485 is no speed limit.
P79:
Signal BL-1
This output signal can be assigned to the several possibilities:
Signaling approaching battery discharge / brake lights !!!!!!
Continuous light
Continuous Flashing
Output "the speed signal"
Signal (pulse) is active in log.1 (+3.3 V). For the “output speed” is generate
1 pulse / 1 electric revolution
P70:
Braking resistors control (activation)
(on - off)
In case of need braking when controller feeding is from power supply (not from battery), must be connected braking resistors and corresponding
power switch. Driving this switch implement this parameter. In active state (= need power switch ON) diving output is +3.3V (+10V). In most cas-
es is power switching element realized as correct designed power MOSFET with driver. Is not allowed freewheel off and not allowed to use the
freewheel with synchro.
P80:
Motor beeping
(value yes / no)
In case that acoustic indication by the engine is unwanted, beep can be disabled by this parameter.
off
on
P55:
PID regulator
– part P
(xxx)
You can set component
P
by this parameter and significantly influence the behavior of the PID controller.
P56:
PID regulator
– part I
(xxx)
You can set component
I
by this parameter and significantly influence the behavior of the PID controller.
P57:
PID regulator
– part D
(xxx)
You can set component
D
by this parameter and significantly influence the behavior of the PID controller.