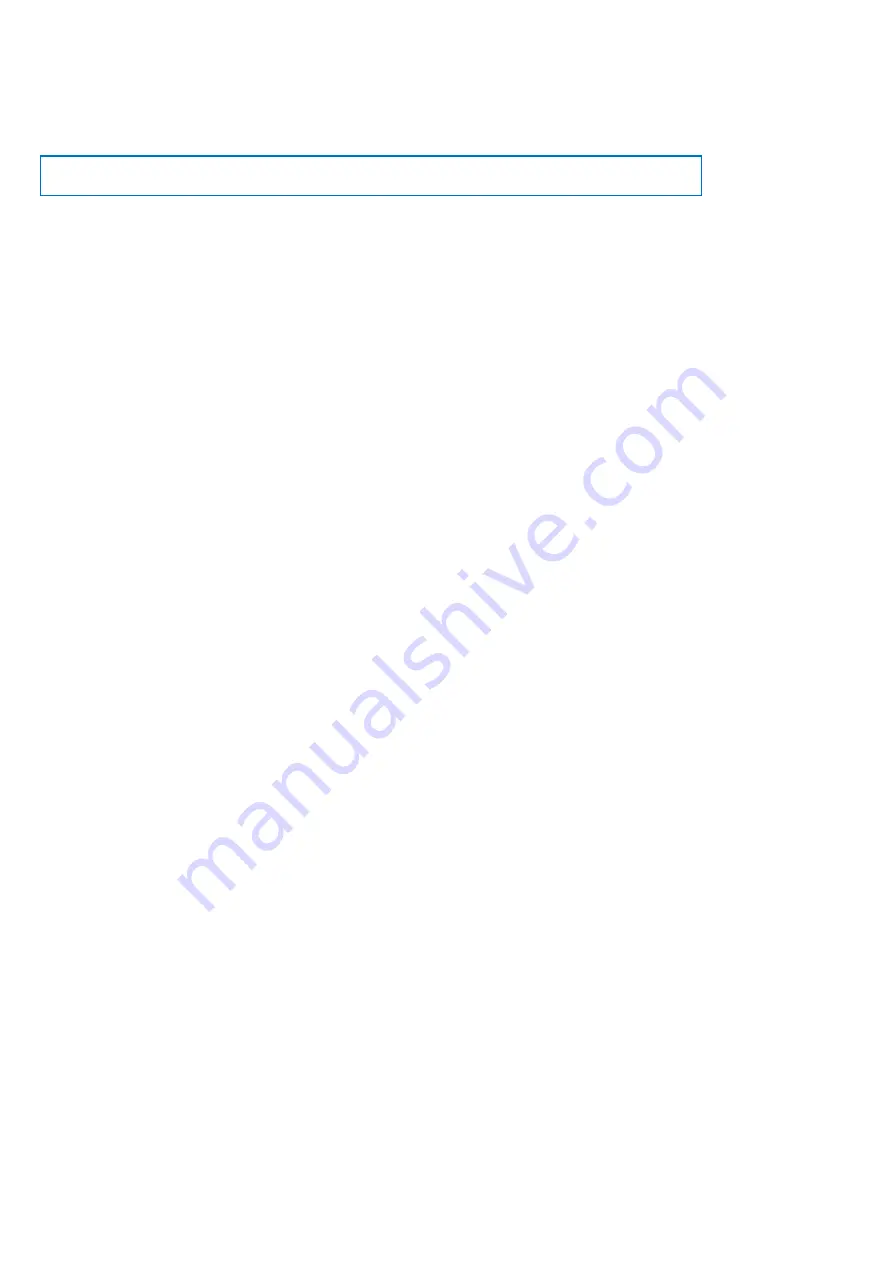
40 / 72
HBC-series V7 LV+MV
P4:
Control signal
Driving signal can be:
-
input PWM (pulse width 1 ÷ 2 ms, period 3.5 ÷ 30 ms, signal pulse level 0 ÷ 3,3V or 0 ÷ 5V)
- voltage 0 up to +3,3V resp. 0 up to +5,0V (or other range)
-
potentiometer 1kΩ (resp. 5kΩ or 10kΩ)
- logic signal, value 0 to +3,3V resp. 0 to +5,0V, read contact, etc.
- data transfer
Note:
Main channel for control signal by input
PWM
is port „
INP_1
“, auxiliary port is „
INP_2
“
Main channel for control by
voltage
(or
potentiometer
) is port „
INP_2
“,auxiliary port is „
INP_1
“
I)
1)
▪ PWM automat
(throttle limits is necessary set for each turning on controller)
2)
▪ PWM programmed
(controller use saved learned throttle limits)
===========================================================================
II) (controller always remember throttle limits
)
3)
▪ PWM main channel (= input
INP_1)
4)
▪ PWM channel 1+2
(main c auxiliary channel)
5)
▪ PWM channel 1-2
(main channel - auxiliary channel)
6)
▪ PWM separated throttle / brake
(main channel control throttle / auxiliary channel control brake)
7)
▪ Voltage main channel (=input
INP_2)
(or potentiometer)
8)
▪ Voltage channel 1+2
(main c auxiliary channel)
9)
▪ Voltage channel 1-2
(main channel - auxiliary channel)
10) ▪ Voltage, separated throttle / brake
(main channel control throttle / auxiliary channel control brake)
11) ▪ Logic signal
12) ▪ Data transfer UART (RS-232)/(RS-485)
13) ▪ Data transfer CAN
14) ▪ Data transfer TWI
This parameter coheres with next parameters
P6
,
P7
and
P8
, resp.
P9
,
P10
and
P11
.
I)
In case
PWM automat
is advantageous because you do not have to set or program anything even when you change the transmitter setting
(on channel throttle) or use different transmitter or receiver (driving signal). The disadvantage is that you have to show the controller the
throttle limits after each turn on of the controller by moving the throttle forwards and backwards, respectively minimal and maximal throttle.
In most cases is better when controller remember real throttle limits. Necessary set this parameter to
“
PWM Programmed
” and learn real
throttle limits by way description for next parameters (P6, P7, P8).
II)
In case „
PWM main channel
“ and next parameters, (i.e. parameters
II
)
,
under line
====
), is necessary directly set values for parameters
P6, P7 a P8, resp. P9, P10 a P11 by program
Controller 2.
This way parameters set not possible change by some other method (as pos-
sible for parameters
I
). Controller remembered these values.
P33:
Control signal limits setting lock
(by signal source settings)
locked (programming disabled)
-
blocks of unwanted rewriting of throttle limits (blocks “learning” of these values)
unlocked (programming enabled)
-
permits learning of throttle limits (rewriting of parameters P6, P7, P8) from signal source
P90:
Monitoring limits for voltage control
Parameter off limits of the analog input voltage 0.15 V and 3.15 V - when above and below this value, the input voltage is evaluated as "out of
range" (Prohibited area L).
Related to monitoring of disconnection control signal / cut potentiometer. When set to "off" prohibited areas are disa-
bled and deactivated and the input signal can be in the full range 0.0 to 3.3 V.
off
on
P92:
Safety switch (KEY, ignition key)
Input used in the "ignition key". When activating, it was triggered sequences switching of antispark relays and the main contractor and allows mo-
tor to run. When it is switched off even when the engine is running, controller correctly disconnected engine and stop it. Subsequently turn-off
contactor and relay and disconnects the traction voltage.
no
yes