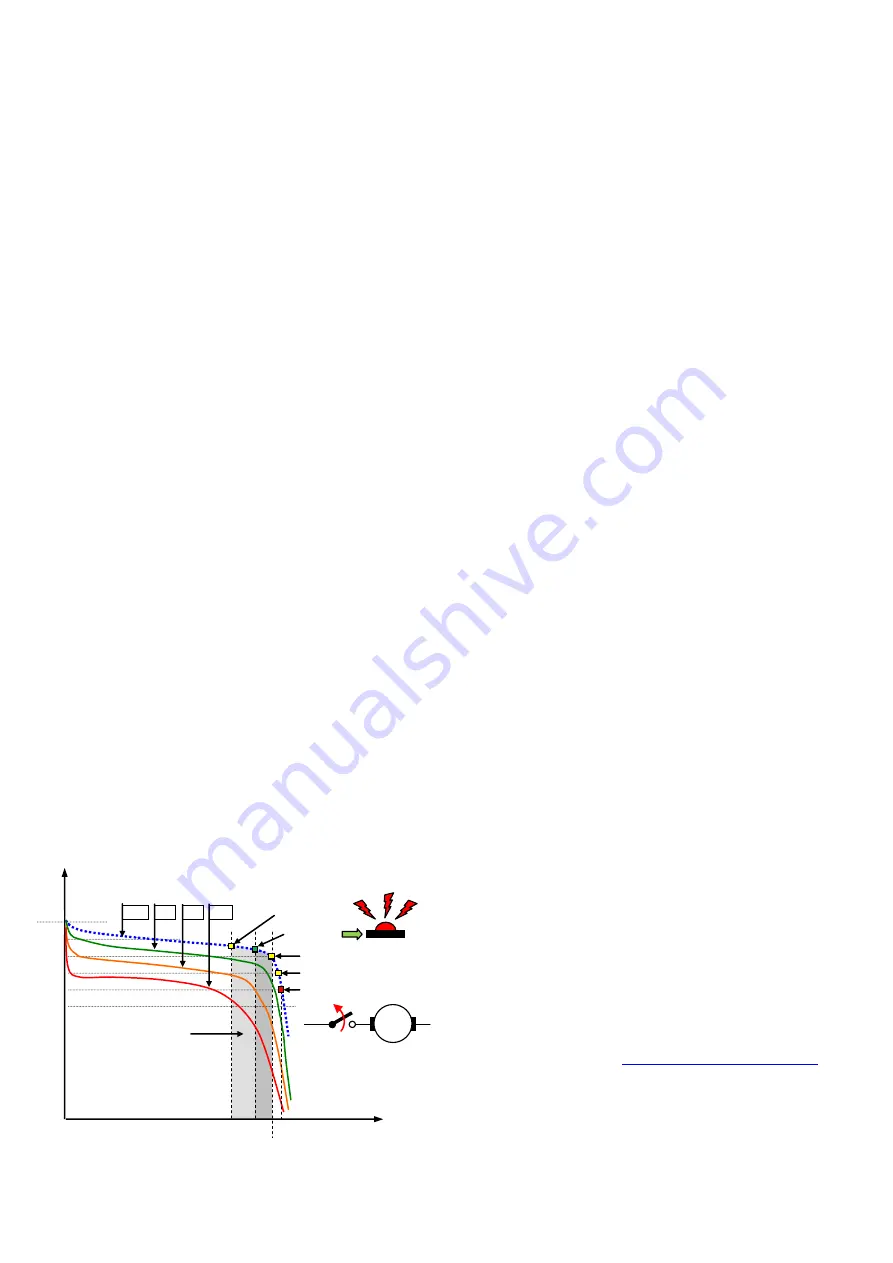
42 / 72
HBC-series V7 LV+MV
P42:
Controller feeding (Type of cells / switching-off voltage)
Parameter set type of cells, include standard switch-off voltage. Monitoring each cell is possible select for some type of cells.
Also is possible set switch-off voltage as 78% of value in moment of connection battery.
Next poss
ibility is selection of “universal cell” (UNI), when is possible set any value – this choice includes so much as type of cell, also cells which
are not available in moment of controller production.
▪
Unwatched battery voltage
–
ATTENTION
, with this setting you can damaged battery !!!
(
battery must be monitored by some external equipment
)
▪
Automat 78%
-
switch-off / power reducing for voltage drop to 78% of value
when connected battery
▪
Lipol (3,2V)
-
switch-off / power reducing for voltage drop to 3,2V / cell
▪
Lipol, monitors each cell -
switch-off / power reducing for voltage drop to 3,2V / cell (necessary external module) *)
▪
A123 (2,5V)
-
switch-off / power reducing for voltage drop to 2,5V / cell
▪
A123, monitors each cell -
switch-off / power reducing for voltage drop to 2,5V / cell
(necessary external module) *)
▪
Nixx (0,8V)
-
switch-off / power reducing for voltage drop to 0,8V / cell
▪
Pb (1,8V)
-
switch-off / power reducing for voltage drop to 1,8V / cell
▪
UNI universal value
-
switch-off / power reducing for voltage drop to set value
▪
UNI, monitors each cell
-
switch-off / power reducing for voltage drop to set value
(
necessary external module except 25063 and 40063 controller
)*)
▪
Power Supply
–
switch-off / power reducing for voltage drop to set value
–
ATTENTION
, with this setting you must not braking (+must not switch-off freewheel) without
connected and set braking resistors (with power switch)
!!! (controller these parameters automatically resize)
*)
excluding controller HBC 25063-3, which has integrated this module inside, it is necessary to connect an external measuring module
into the connector ICS-2..
Note
:
78% Automat
mode is useful if you often change the number or type of traction battery cells (you do not have rebuilt settings). The system to
work correctly, it is necessary to
always start with a fully charged battery!
If this condition is not met, cannot be guaranteed correct disconnect-
ed motor end (turn-off) battery voltage - i.e. if you start with an already partially or fully discharged battery, can significantly over discharge cells
and destroy them (mainly in the case of Lithium cells).
P43:
Number of cells
Set used number of cells for
Lipol
,
A123
,
Nixx
,
Pb
and
UNI
battery.
Not operate for
Automat 78%
and
Not monitored
…. – in these two cases is parameter afield.
P78:
Battery capacity
(value in Ah)
This enables possibility watch, in real time, discharging main battery in the model by “back data transfer” via Telemetry – as “fuel tank indicator”. It
is also important to specify when using parameter
P87
,
Capacity countdown
.
P44:
Switch-off voltage / cell [ For P42=UNI ]
(value in Volts)
Set switch-off voltage for one cell for selection
UNI
cells
.
P45:
Empty
battery Behavior
Motor stop
Motor stop with brake
Power reduction
When the voltage drops to a preset turn-off value can be set either by a gradual reduction in power or off (with the possibility of a new turned on
after moving the joystick to the STOP position if the battery is a little "recover" and its voltage rises again).
P77:
"Empty battery" in advance warning by voltage
(alarm when battery voltage drops below that …)
(value in Volt
– overall voltage)
Defines the total battery voltage, which is activated when an external indication to connector
ICS-2
, the signal
BL_1
. Appropriate setting can be
done that the notice of impending battery will get well in advance. Please, respect real discharging curves (characteristics) for used battery.
Switching-off voltage set to safety value corresponding with choice battery
type (parameter P42, P43, P44)
– example on the picture have set
3.0 V/ cell
for Lipol, red point on blue dotted discharging curve (starting val-
ue for motor power limitation).
Early warning voltage
set to corresponding value with requested residual
energy
– example on picture have set
3.7 V/ cell
, green point on blue dot-
ted discharging curve. Please, always respect discharging characteristics of
used battery, see to values on battery producer datasheet. Always use dis-
charging curve for lower current (lowest “C” rate), blue dotted curve for
example on the picture. Residual energy is in this sample ca 10%.
In regard of unique feature of
MGM
COMPRO
controllers (recalculation of
te
rminal battery voltage to its internal voltage), is this voltage (≈ residual
energy) almost independent on internal battery resistance as well as on real
battery discharging current, see „
Protective and safety mechanism ….
We recommend this set voltage (≈ residual energy) check by one discharg-
ing cycle on the ground (not during real flight) and verify real value of resid-
ual energy, and eventually make little correction by real result.
Profitable can be association with each cell monitoring
, by possibility of set-
ting of parameter
P42, Controller feeding.
Note:
Some types of batteries (such as A123 or LiFePO4) have extremely flat discharge curve for most of the time of discharge or even nega-
tive (end voltage increases). In these cases, early-warning mechanism does not work and can not be used - must use the "
Capacity
Countdown
" parameter
P87
.
Motor
TMM
®
controllers
MGM
COMPRO
– early warning indication
U
100%
capacity
[mAh]
Battery voltage for current:
3.0V
/
cell
3.3V
/
cell
3.6V
/
cell
3.7V / cell
3.8V / cell
Defined residual
energy for BEC
75% 90%
95%
4.2V
cell
0.5C
2C 10C 20C
LED flash