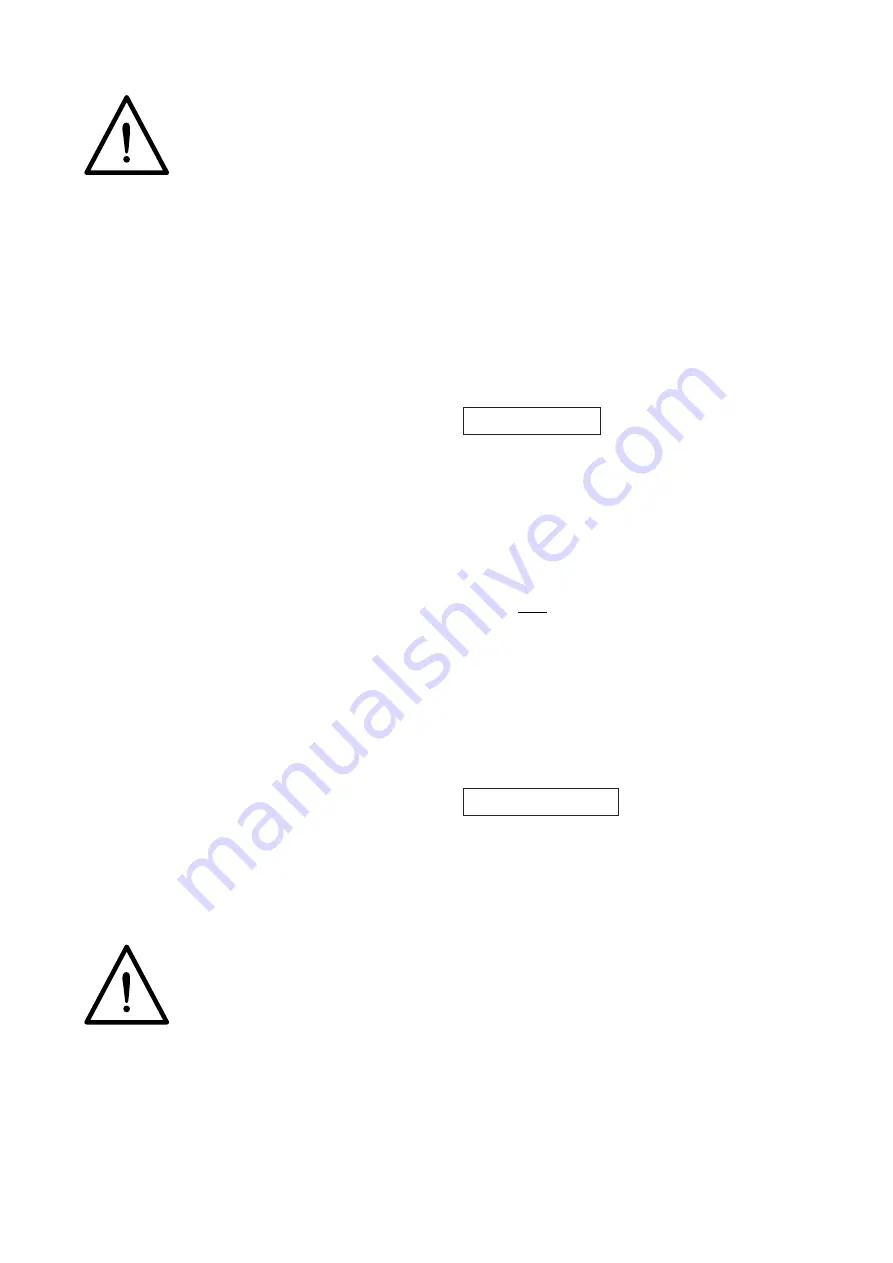
Instruction Manual MC6000
4-10
Using the internal braking resistor (Standard model):
For a single braking process within a ten minute period the peak braking power of 6kW may be
applied for 8 seconds (see Diagram 2, curve A). This assumes that the temperature of the side-
mounted heat sink is
≤
60° C before the start of braking. For cyclic braking the braking poweer
and duration can be read off curve B in Diagram 2.
Continuous braking power is shown in the table on page 4-5. In the case of regenerative
applications, i.e. continuous braking (an exception) permissible continuous braking power
corresponds to power loss.
Example : Checking an operating point for single braking processes (curve A)
A drive with an MC6404 is being used at occasional irregular intervals (always >10 min.) for
raising and lowering a tool. The braking power required has been calculated at 2.2 kW for
20 seconds. Is the internal braking resistor adequate for this purpose?
1.
Permissible braking energy:
2.
Condition for each operating point:
in the example:
⇒
The internal resistor is adequate if the temperature of the heat sink is
≤
60° C before the
braking operation. Check correct operation during commissioning.
Examplel : 2 Checking an operating point for cyclic braking (curve B)
Is the internal braking resistor still adequate if the lifting operation is to be every 90 seconds
(including 6 seconds total braking time) on a regular basis?
1.
Braking duration:
Braking time:
2.
Permissible braking energy:
for the MC6404:
3.
Condition for each working point:
in the example:
® from the table on pages 4-7, at the foot:
⇒
An external braking resistor is in fact required.
Using an external braking resistor (BR2 and BR3):
BR2 only: Peak braking power is limited by the braking circuit to 8 seconds. The waiting time
after a braking operation (or cyclic braking application) is shown in Fig. 2.
BR2 and BR3: The resistance value must be at least that shown in the table or damage to the
braking transistor may result. Continuous braking power depends on the continuous and peak
braking power of the resistance value of the resistor.
If there is an internal resistor, it must be disconnected and its connections insulated. As the
braking resistor generates heat it is essential to ensure it is mounted with adequate separation
from the servocontroller.
E
P
s
E
kW
s
Ws
P
t
E
kW
s
Ws
E
A
A
Br eff
Br
A
A
max
max
max
max
max
.
.
,
.
=
⋅
=
⋅
=
⋅
≤
⋅
=
≤
8
6
8
48 000
2 2
20
44 000
ED
s
s
t
s
s
E
P
s
E
W
s
Ws
P
t
E
kW
s
Ws
E
E
Ws
Br
EDBr
B
eff
B
Br eff
EDBr
B
B
=
=
=
⋅
=
=
⋅
=
⋅
=
⋅
≤
⋅
=
>
=
6
90
6 7
120
6 7
8
120
60
120
7 200
2 2
8
17 600
48 000
, %.
, %
.
.
,
.
.
max
max
max
max
max
(assuming 120 s
cycle)
for BR2 with R
B
= 90
Ω
.
Internal braking
resistor is not
adequate