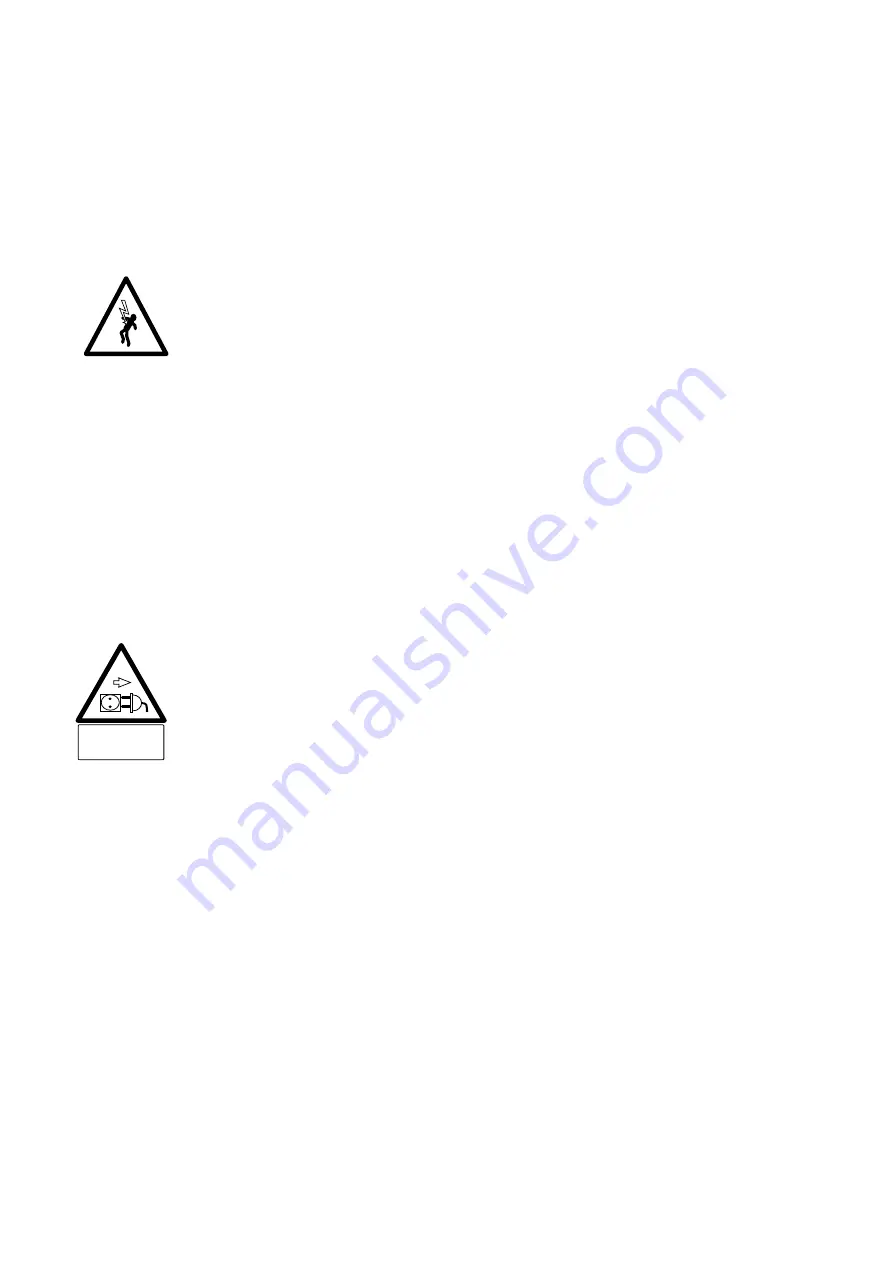
Instruction Manual MC6000
3-2
2. Cabinet installation of the Servocontroller: follow installation instructions (heat, minimum
mounting distances for installation) in
Section 2.7.
3. Electrical installation of the Servocontroller: the electrical installation of the Servocontroller
depends on its application. Wiring instructions are contained in
Section 4 “Electrical
Connections”.
•
open the MC6000 Servocontroller by undoing the screw on the front (bottom right).
•
wire up motor (including thermistor), do not mix up motor phases
•
connect encoder cable to motor and Servocontroller
•
wire up control terminals (observe power stage enable: ENPO)
•
wire up serial interface, encoder simulation, Bus system or application hardware, eg I/O
module 1 (AH1) as appropriate
•
connect to the mains, but do not switch on yet
4. Check the electrical installation. Check all connections, then close the MC6000 cabinet again.
3.3
Commissioning of the Drive System
1. Function test (correct selftest sequence):
•
switch on mains power supply
•
during MC6000 selftest the display is backlit red and displays the message "TEST"
•
after successful completion of the self test the colour of the display changes to green
and the current actual value is displayed in the VAL menu (torque speed or position
depending on mode; parameter REFV in the VAL menu)
•
if the device detects an error during self testing, the red backlit display will indicate the
cause of the fault
(see Section 9)
wait 2 minutes
after power-off
3.2
Installation of the drive system
1. When installing the Servomotor in the system or machine observe the instructions in
Sections
4.3.2 and 12. If possible delay installing shaft end items (e.g. gears, pulleys, couplings etc.)
until after commissioning, so that tests can be carried out without exposed system parts
turning.
Note:
Suitable devices must be used for fitting and removing shaft end items and there must
be support at the A end of the shaft.
Warning! Safety instructions for Servomotors
•
after installing the motor check that brake (if present) operates correctly
•
before commissioning motors with a feather key in the shaft end, the feather key must be
securred to prevent it being thrown out if this is not prevented by the presence of drive shaft
items such as pulleys, couplings or similar
•
these motors are designed for operation using a Servocontroller. Direct connection of such
motors to the mains may result in their destruction
•
surface temperatures above 100 degrees C may occur on the motors. Consequently no
temperature-sensitive items may be placed or fixed on them. If necessary, measures to
prevent people touching them must be provided
•
the optional emergency hold brake is only designed for a limited number of emergency
stops. It is not approved for use as a normal working brake
•
the PTC in the windings must be connected to the Servocontroller to prevent overheating of
the motor