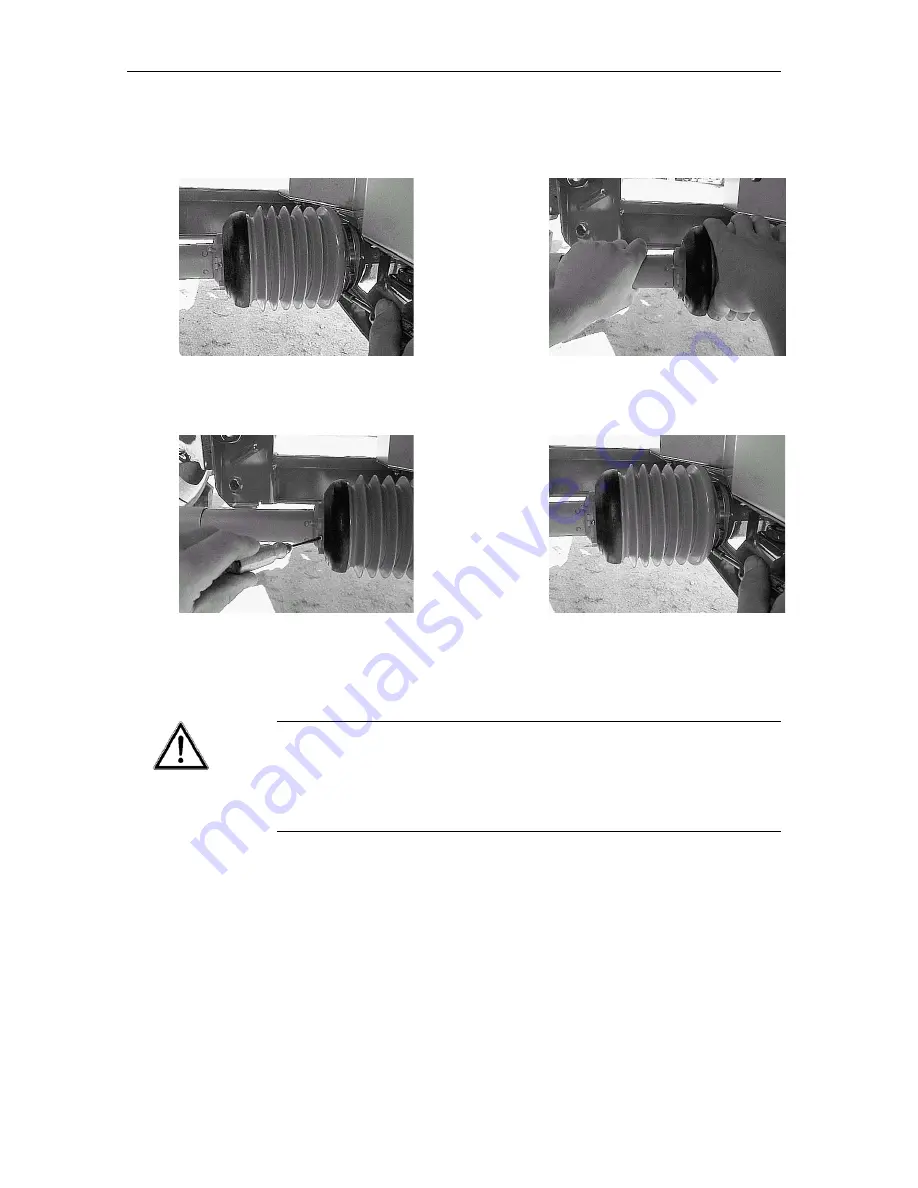
Erreur ! Style non défini.
Erreur ! Style non défini.
23
5.
Pull the guard muff over the pto CV
joint onto the housing boss and pla-
ce the banjo clip into position (do not
tighten).
6.
Turn the guard muff into its locked
position.
7.
Screw in locking screw.
8.
Tighten banjo clip.
•
Before engaging the pto drive, make sure that the correct tractor pto speed
is selected to match the recommended speed of the implement. (Respect
all details given in the spreading chart and the max. allowable pto speed.)
Drive shaft damage when engaging the pto drive
The pto drive shaft and the agitator drive can suffer damage if the pto drive is
engaged at high tractor engine speeds.
•
Engage the pto drive at lower tractor engine speeds to avoid sudden over-
load to the drive shaft and agitator drive.
•
Make sure that pto shafts, protector tube and end gaiter, as well as extension gaiters on the side
of the fertiliser spreader, are correctly in place and in good condition!
•
When detaching the pto shaft, place it in the holder provided on the fertiliser spreader.
•
Do not use the safety chain to support the shaft when not in use.
IMPORTANT