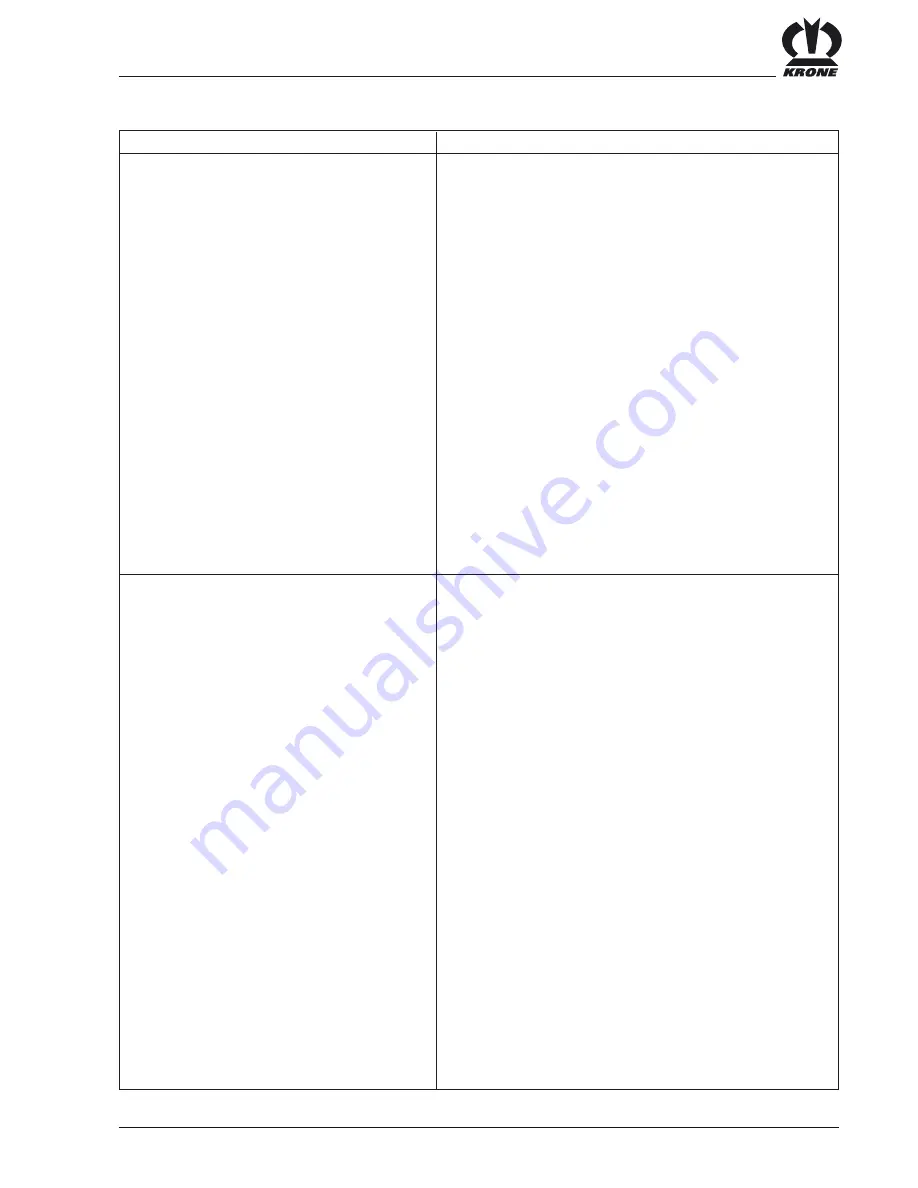
XIII - 7
Faults, their Causes and Elimination
Fault
Blockage in the system or in any connected
bearings.
Hand-actuated systems.
Hand lever cannot be moved or is hard to move.
Blockages in the Distributor
If no lubricant comes out of the outlets after all
the outlets on the main distributor and/or the
sub-distributor have been taken off, the
distributor is blocked.
13.8 Finding Errors in the Central Lubrication System
Eliminating the Fault
Establishing the Causes of Blockages and Eliminating
Them.
PROCEDURE
First check whether the transport pump is working and is
providing the distributor with lubricant. To do this take off the
pump outlet and switch on the pump. If the pump is working
properly connect the pump outlet again. (Conclusion: the pump
is in perfect condition.)
Let pump run until the next blockage occurs or the next
unacceptable pressure increase occurs. Let the pressure
remain.
Loosen the inlet screw fittings on the sub-distributor or the main
distributor one after the other. For single-stage systems loosen
the inlet screw fittings one after the other.
The distributor
which suddenly leaks lubricant when the
screw fitting is loosened unter pressure
leads to the source of
the fault.
The screw fittings should then be tightened up again. The
pertinent bearing inlet screw fittings should then be loosened
one after the other. The bearing whose inlet screw fitting leaks
lubricant when loosened under presure is the bearing which is
blocked. Clear the blockage.
Replace the blocked distributor.
If necessary the distributor can be cleaned under the following
conditions.
A clean working area must be available.
Remove all pipe connection screw fittings.
Remove the piston screw plug with a strong screw driver. If
loosen by striking the screw with a hammer.
Die piston should be removed with a soft mandril (with less than
6 mm Ø, if possible plastic).
Very important:
A record should be kept of which piston
belongs to which drilling so that the pistons cannot be mixed up.
Clean the distributor body several times with grease-soluble
cleaning agent and blow dry with compressed air.
There are inclined channels with a diameter of 1.5 mm located
at the ends of the thread on the piston screw openings, which
should be cleared with a piece of wire or a pin.
Clean and blow dry the distributor again.
Congealed grease may have formed in the piston screw plugs,
which should be removed.
Re-assemble the distributor, at the same time replacing all
copper strips.
Before screwing in the pipe oputlet fittings, oil (if possible)
should be pumped through the distributor several times with a
hand pump or similar.
The pressure in the distributor should not exceed 25 bar. A
pressure higher than this means that the distributor was not
cleaned properly or that the piston openings are damaged. If
the distributor operating pressure does not fall below 25 bar in
spite of remedial action, the distributor should be replaced.
Summary of Contents for Big Pack 127 / MultiCut
Page 10: ...I 6 General Information ...
Page 15: ...II 5 Safety ...
Page 22: ...II 12 Safety ...
Page 46: ...IV 10 Comfort Controls ...
Page 70: ...VI 16 Settings ...
Page 90: ...X 2 ...
Page 92: ...XI 2 Putting into Operation Again ...
Page 114: ...XII 22 Special Equipment ...