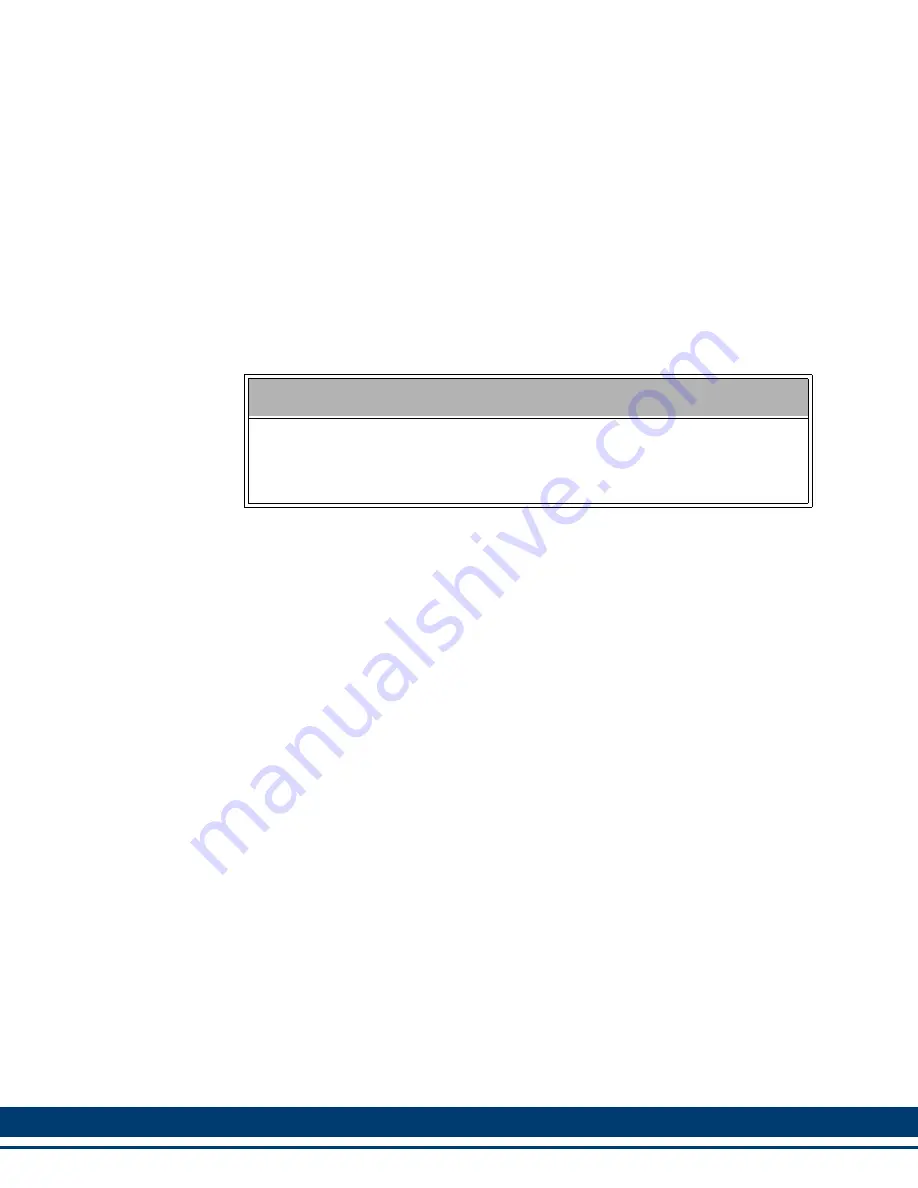
Kollmorgen - June 2014
337
MMC Smart Drive Hardware Manual
-
DRIVE RESIDENT DIGITAL MMC CONTROL
Low level signals that can be less than three meters in length or can be separated
from noise sources are tested at a 1 KV level. Under the stated conditions, there will
be no disturbance of digital I/O, encoder, or encoder operation. For analog signals,
there may be momentary disturbances but there will be self-recovery when the noise
subsides.
Do not operate transmitters, arc welding equipment, or other high noise radiators
within one meter of an enclosure that has the door open. Continue to equip inductive
devices, if they are in series with a mechanical contact or switch, with arc suppression
circuits. These devices include contactors, solenoids and motors. Shield all cables
that carry heavy current near the system, using continuous foil wrap or conduit
grounded at both ends. Such cables include power leads for high-frequency welders
and for pulse-width-modulated motor drives.
13.4
Starting an Operation
Good procedure suggests that the system should be tested each time a new
application is powered up. The Diagnostic LED (D2) on the Drive Resident Digital
MMC Control should be off indicating that the diagnostic tests were passed.
Turn off the main disconnect switch and plug the DC connector into the power
connector on the MMC-SD. Turn on input power. The D2 LED turns on and then turns
off when the Drive Resident Digital MMC Control passes its diagnostic tests.
13.4.1
Connecting the Drive Resident Digital MMC Control to the Applica-
tion
1.
Turn off the main disconnect switch in the control cabinet. If some devices are not
powered from the control cabinet, turn them off also.
2.
Connect the connectors according to your diagrams.
3.
Turn on power to the system. The PWR light on the MMC-SD goes on and stays
on.
The D2 light goes on, then goes off in turn.
The SCAN (S) light goes on.
The application starts to work under control of the system.
4.
If an application program is not in system memory, use the download command in
the PiCPro software to place it there.
13.4.2
Basic Setup and Maintenance Procedures
below summarizes how to proceed when performing certain maintenance
and/or setup functions.
WARNING
Use care when wiring I/O devices to the Drive Resident Digital MMC Control
and when plugging in cables. Wiring the wrong device to the connector or
plugging a connector into the wrong location could cause intermittent or in-
correct machine operation.
Summary of Contents for MMC Smart Drive Series
Page 2: ......
Page 10: ...8 Kollmorgen June 2014 MMC Smart Drive Hardware Manual TABLE OF CONTENTS...
Page 14: ...12 Kollmorgen June 2014 MMC Smart Drive Hardware Manual INTRODUCTION TO THE MMC SMART DRIVE...
Page 164: ...162 Kollmorgen June 2014 MMC Smart Drive Hardware Manual 460V 3 PHASE MMC SMART DRIVE NEXTGEN...
Page 286: ...284 Kollmorgen June 2014 MMC Smart Drive Hardware Manual S200 DLS DRIVE Figure 9 1...
Page 316: ...314 Kollmorgen June 2014 MMC Smart Drive Hardware Manual MOTOR CABLES CONNECTORS...
Page 368: ...366 Kollmorgen June 2014 MMC Smart Drive Hardware Manual DECLARATIONS OF CONFORMITY...
Page 369: ...Kollmorgen June 2014 367 MMC Smart Drive Hardware Manual DECLARATIONS OF CONFORMITY...
Page 370: ...368 Kollmorgen June 2014 MMC Smart Drive Hardware Manual DECLARATIONS OF CONFORMITY...
Page 371: ...Kollmorgen June 2014 369 MMC Smart Drive Hardware Manual DECLARATIONS OF CONFORMITY...
Page 372: ...370 Kollmorgen June 2014 MMC Smart Drive Hardware Manual DECLARATIONS OF CONFORMITY...
Page 384: ...MMC Smart Drive Hardware Manual INDEX 382 Kollmorgen June 2014...
Page 386: ...384 Kollmorgen June 2014 MMC Smart Drive Hardware Manual SALES AND SERVICE...