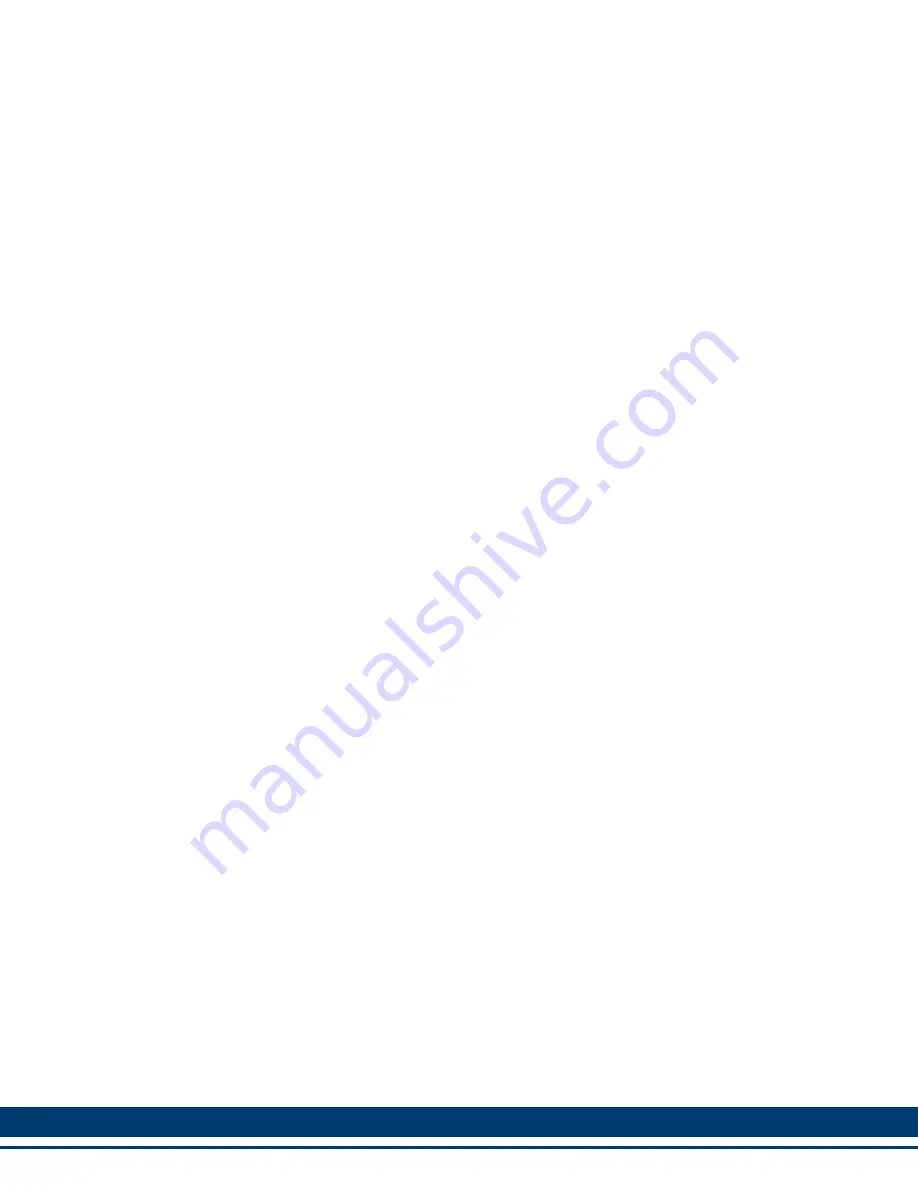
Kollmorgen - June 2014
305
MMC Smart Drive Hardware Manual
-
MOTOR CABLES & CONNECTORS
10
Motor Cables & Connectors
Kollmorgen offers many cables that connect directly from the MMC Smart Drive’s F1/
F2 connector to various Kollmorgen motors. These cables are described in detail in
This section describes additional cables and connector kits that can be used to
connect Kollmorgen motors and drives, as well as providing cable installation
guidelines.
10.1
Flex Cable Installation Guidelines
Follow these guidelines for any flexing cable application:
•
Cable should be hung suspended for 48 hours to develop its most natural “set*
and lay” prior to installation
•
A cable should be installed with, not against, its natural set
•
Using strain relief fittings at both ends of the cable will reduce conductor breakage
at the flex points
•
If there is any kink in a cable after installation, it will always remain and eventually
cause a cable failure
•
After installation, the most critical factors in the cable are the minimum bend
radius and the reel tension
* Note: The natural set occurs during the manufacturing of the cable. The cable is
cured in one direction on the reel with a notable difference in its ability to be flexed one
way versus the other.
When using specially designed flex cables, the following five criteria must be
considered:
•
Bending Radius
•
Cable Tension
•
Operating Speed
•
Temperature
•
Ampacity
Bending Radius and Cable Tension are discussed in the following sections.
10.1.1
Bending Radius
The following guidelines recommended by the ICEA standards are intended to
optimize cable life:
•
Minimum Bend Radius (Shielded Feedback Cables) = 12 times the Cable Diame-
ter
•
Minimum Bend Radius (Shielded Power Cables) = 12 times the Cable Diameter
Reduced bending radii result in reduced cable life due to increased stress on the
copper conductors and overall distortion of the cable. Therefore, reduced radii should
only be considered for applications in which other factors, such as reduced cable
tension, lower operating speed, and ambient temperature are more favorable to cable
life, or where the mechanical limitations of the installation do not allow the optimum
radius.
Summary of Contents for MMC Smart Drive Series
Page 2: ......
Page 10: ...8 Kollmorgen June 2014 MMC Smart Drive Hardware Manual TABLE OF CONTENTS...
Page 14: ...12 Kollmorgen June 2014 MMC Smart Drive Hardware Manual INTRODUCTION TO THE MMC SMART DRIVE...
Page 164: ...162 Kollmorgen June 2014 MMC Smart Drive Hardware Manual 460V 3 PHASE MMC SMART DRIVE NEXTGEN...
Page 286: ...284 Kollmorgen June 2014 MMC Smart Drive Hardware Manual S200 DLS DRIVE Figure 9 1...
Page 316: ...314 Kollmorgen June 2014 MMC Smart Drive Hardware Manual MOTOR CABLES CONNECTORS...
Page 368: ...366 Kollmorgen June 2014 MMC Smart Drive Hardware Manual DECLARATIONS OF CONFORMITY...
Page 369: ...Kollmorgen June 2014 367 MMC Smart Drive Hardware Manual DECLARATIONS OF CONFORMITY...
Page 370: ...368 Kollmorgen June 2014 MMC Smart Drive Hardware Manual DECLARATIONS OF CONFORMITY...
Page 371: ...Kollmorgen June 2014 369 MMC Smart Drive Hardware Manual DECLARATIONS OF CONFORMITY...
Page 372: ...370 Kollmorgen June 2014 MMC Smart Drive Hardware Manual DECLARATIONS OF CONFORMITY...
Page 384: ...MMC Smart Drive Hardware Manual INDEX 382 Kollmorgen June 2014...
Page 386: ...384 Kollmorgen June 2014 MMC Smart Drive Hardware Manual SALES AND SERVICE...