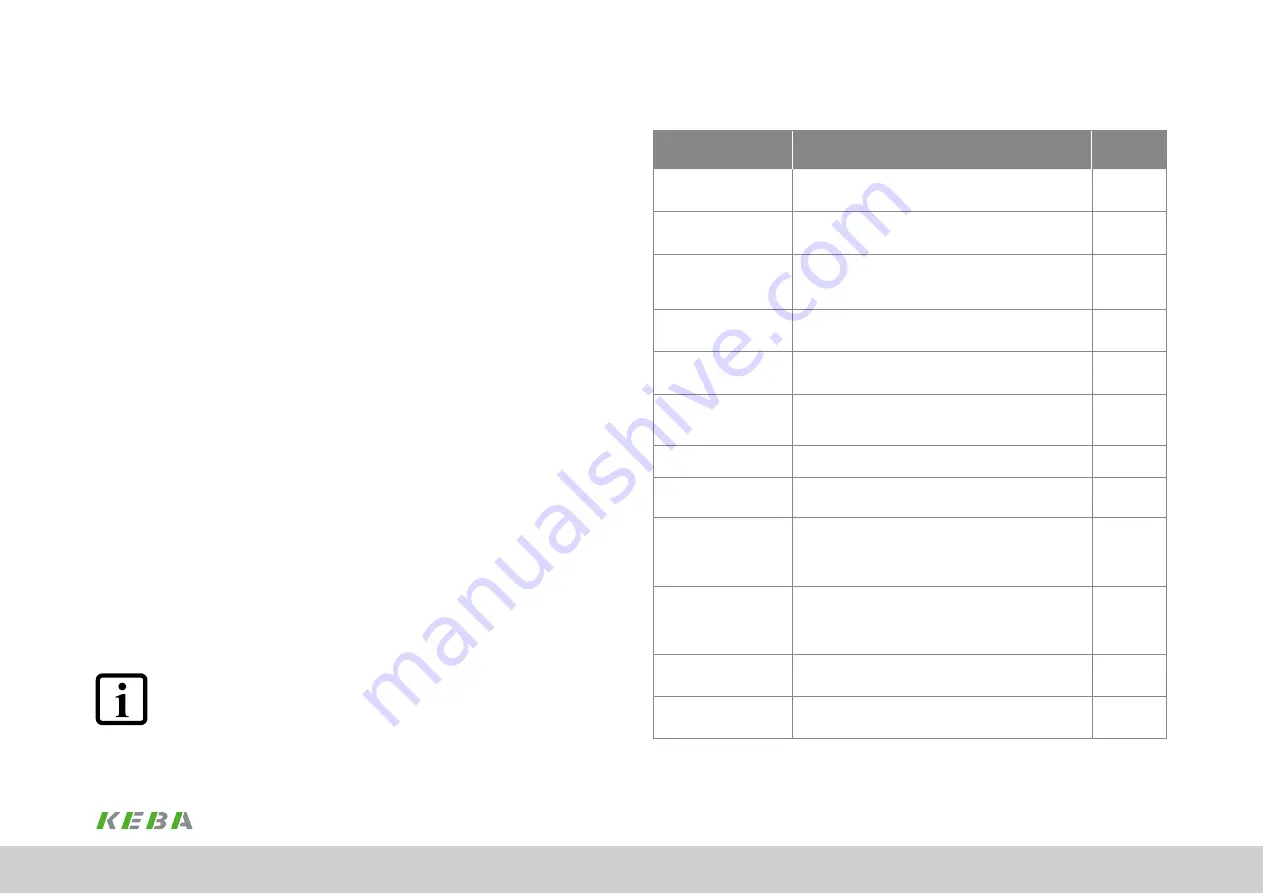
Operation Manual ServoOne Supply Unit
7
ID no.: 1101.21B.6-00 Date: 04/2020
General
1
General
The product DVD from KEBA Industrial Automation Germany GmbH contains the
complete documentation for the related product series. The documentation for a product
series includes the operation manual (hardware description), device help (software
description) as well as further user manuals (e.g. field bus description and specifications).
The documents are available in the formats PDF or HTML.
1.1 Target group
Dear user,
the documentation forms part of the device and contains important information on
operation and service. It is aimed at all persons who undertake mounting, installation,
commissioning and servicing work on the product.
1.2 Prerequisites
Prerequisites for the usage of devices from KEBA:
y
The documentation on the devices is to be stored so it legible, accessible at all times and for the
entire life of the product.
y
Read and ensure you understand the documentation on your device.
y
Qualification: to prevent injury or damage, personnel may only work on the device if they have
electrical engineering qualifications.
y
Knowledge required:
− National health and safety regulations (e.g. BGV A3 in Germany)
− Mounting, installation, commissioning and operation of the device
Work in other areas, for example transport, storage and disposal is only allowed to be
undertaken by trained personnel.
NOTE
This operation manual only applies to the supply unit for the ServoOne multi-
axis system (referred to in the following as the supply unit or SOVE for short).
1.3 Reference documents
Document
Contents
ID no.
Format
ServoOne junior -
Operation Manual
Safety, mechanical installation, electrical installation, commissioning,
diagnostics, specifications, certification and applicable standards,
technical data
1300.20B.x
ServoOne Single-Axis
System -
Operation Manual
Safety, mechanical installation, electrical installation,
commissioning, diagnostics, specifications, certification and
applicable standards, technical data
1100.20B.x
ServoOne Multi-Axis System -
Operation Manual
Safety, mechanical installation, electrical installation, commissioning,
diagnostics, STO, operation with servocontroller as supply, planning,
application example, specifications, certification and
applicable standards, technical data
1101.20B.x
ServoOne Multi-Axis System
Supply Unit -
Operation Manual
Safety, mechanical installation, electrical installation, commissioning,
diagnostics, specification, certification and applicable standards,
technical data
1101.21B.x
ServoOne Sercos II -
User Manual
Safety, commissioning, communication phases, parameter interface,
error, warning and status messages, operation modes, weighting,
referencing, touchprobe, parameter lists
1100.29B.x
ServoOne Sercos III -
User Manual
Safety, installation and connection, commissioning and configuration,
setting parameters, data transmission, scaling and weighting,
functionality, error message and diagnostics, parameter lists
1108.26B.x
CANopen/EtherCAT -
User Manual
Safety, commissioning, data transmission, operation modes,
referencing, parameters, technical data
1108.28B.x
PROFIBUS-DPV
User Manual
Description and configuration of the parameters for the ServoOne
on the PROFIBUS-DPV field bus system
1108.27B.x
ServoOne System -
System Catalogue
Information, notes on ordering, specifications and
technical data on:
ServoOne junior, ServoOne single-axis system, ServoOne multi-axis
system, safety technology, communication, technology, function
packages, accessories and motors
1100.24B.x
ServoOne - device help
Description of the software functionality ServoOne,
firmware versions:
- SO junior from V1.30-xx
- SO single-axis system from V3.25-xx
- SO multi-axis system from V3.25-xx
0842.26B.x
PDF and HTML
Program help DriveManager 5
PC user software
Context-sensitive help for DriveManager version 5.x graphic PC
user software for initial commissioning and serial commissioning,
operation, diagnostics and project management
0842.25B.x
PDF and HTML
UL-Certification
Notes on UL-compliant mounting and usage
0927.21B.x
Summary of Contents for ServoOne Series
Page 6: ...Operation Manual ServoOne Supply Unit 6 ID no 1101 21B 6 00 Date 04 2020 Table of contents ...
Page 10: ...Operation Manual ServoOne Supply Unit 10 ID no 1101 21B 6 00 Date 04 2020 ...
Page 90: ...Operation Manual ServoOne Supply Unit 90 ID no 1101 21B 6 00 Date Date 04 2020 Glossary ...
Page 91: ...Operation Manual ServoOne Supply Unit 91 ID no 1101 21B 6 00 Date 04 2020 ...