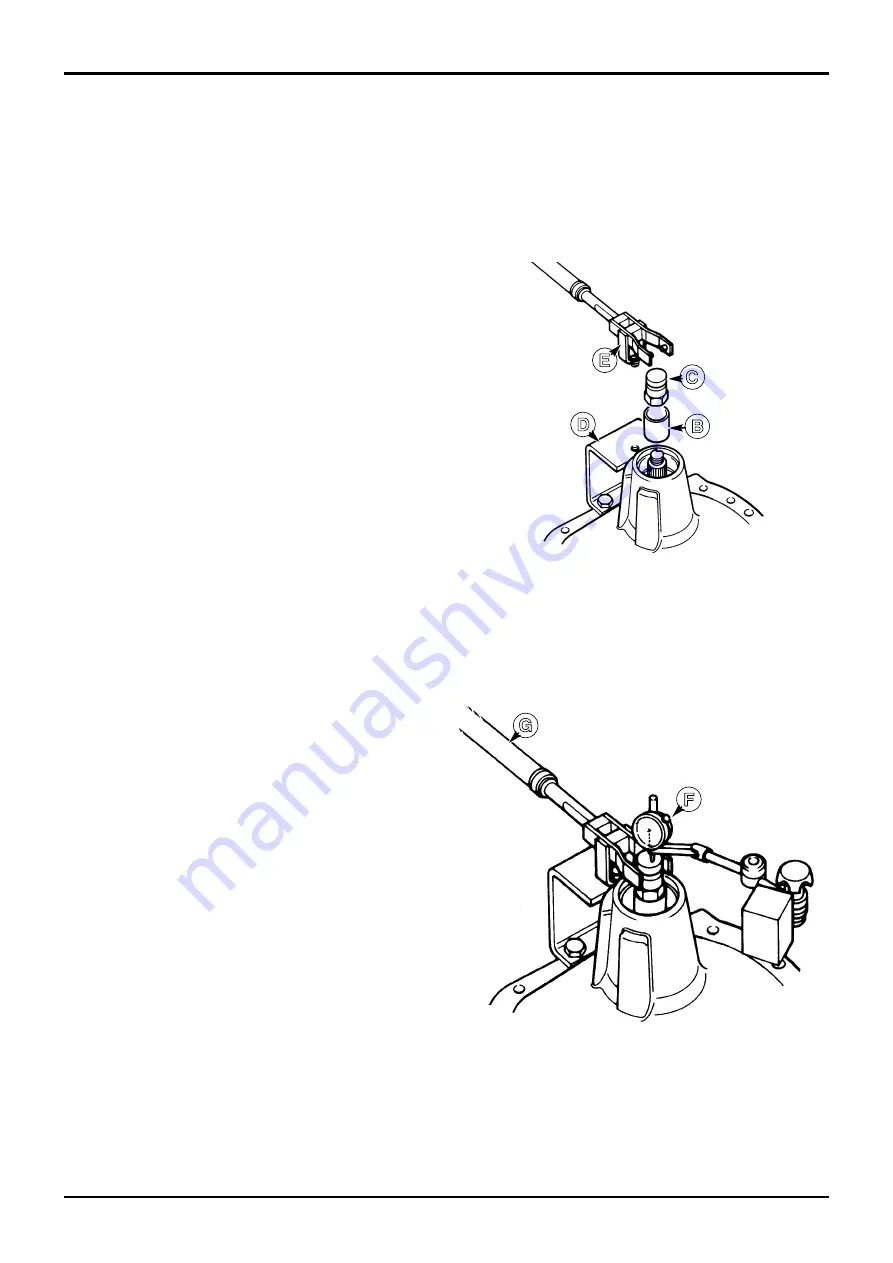
82 - 4
Section F
9803/3280
Section F
82 - 4
Issue 1
Front Axle - SD55
Drive Head - Assembly
The outline procedure below refers also to the following
aspects of the drivehead assembly, which are covered
separately in detail as sub topics later in this section:
Pinion Depth Setting
Collapsible Spacer Assembly
Crown Wheel and Pinion Meshing
Note:
Both the crownwheel
15
and pinion
20
and the bevel
gears
9
and
10
are matched and should be renewed as sets
if any of their components are damaged or excessively
worn. The two differential housing halves
8A
and
8B
are also
matched. Do not use unmatched halves.
Make sure all bearings are lightly oiled before fitting and
setting. Make sure bearings are rotated whilst being set.
1
Determine the correct thickness required for the shims
23
, refer to
Pinion Depth Setting
.
2
Fit shims
23
behind new bearing cup
22
.
3
Fit new pinion head bearing cone
22
onto pinion
20
.
4
Install pinion and bearings into the drive head casing.
Install largest available solid spacer
24
e.g (14.20 mm)
and fit pinion tail bearing
21
(lightly oiled). Do not fit the
oil seal
19
at this stage.
Note
: It should be noted that the axle is assembled using a
solid spacer. However, in the absence of the special tools
required or the correct size solid spacer
24
it is acceptable
to fit a collapsible spacer, refer to
Collapsible Spacer
Assembly
.
5
Fit special tool sleeve
B
and special pinion shaft
adapter
C
. Tighten adapter
C
to approximately 50 Nm,
making sure the pinion is free to rotate and there is end
float, this will prevent any damage to the bearing. If the
pinion is not free to rotate or there is no end float at this
stage check the bearing is fitted correctly. Also check
the correct size spacer has been fitted.
6
Fit special bracket
D
to the drive-head housing using
two M10 x 30 nuts and bolts. Fit special tool support
pillar
E
to bracket
D
so that the fork end engages in
adapter
C
. Ensure that fork
E
is centrally located on
adapter
C
. If necessary, re-align bracket
D
to suit.
7
Fit dial test indicator (DTI)
F
. Ensure that the DTI is
mounted on the drive head and not on bracket
D
.
8
Set torque wrench
G
to 35 Nm (25.8 lbf ft) and measure
the end float while rotating the shaft.
C
B
D
348030
E
F
G
348040