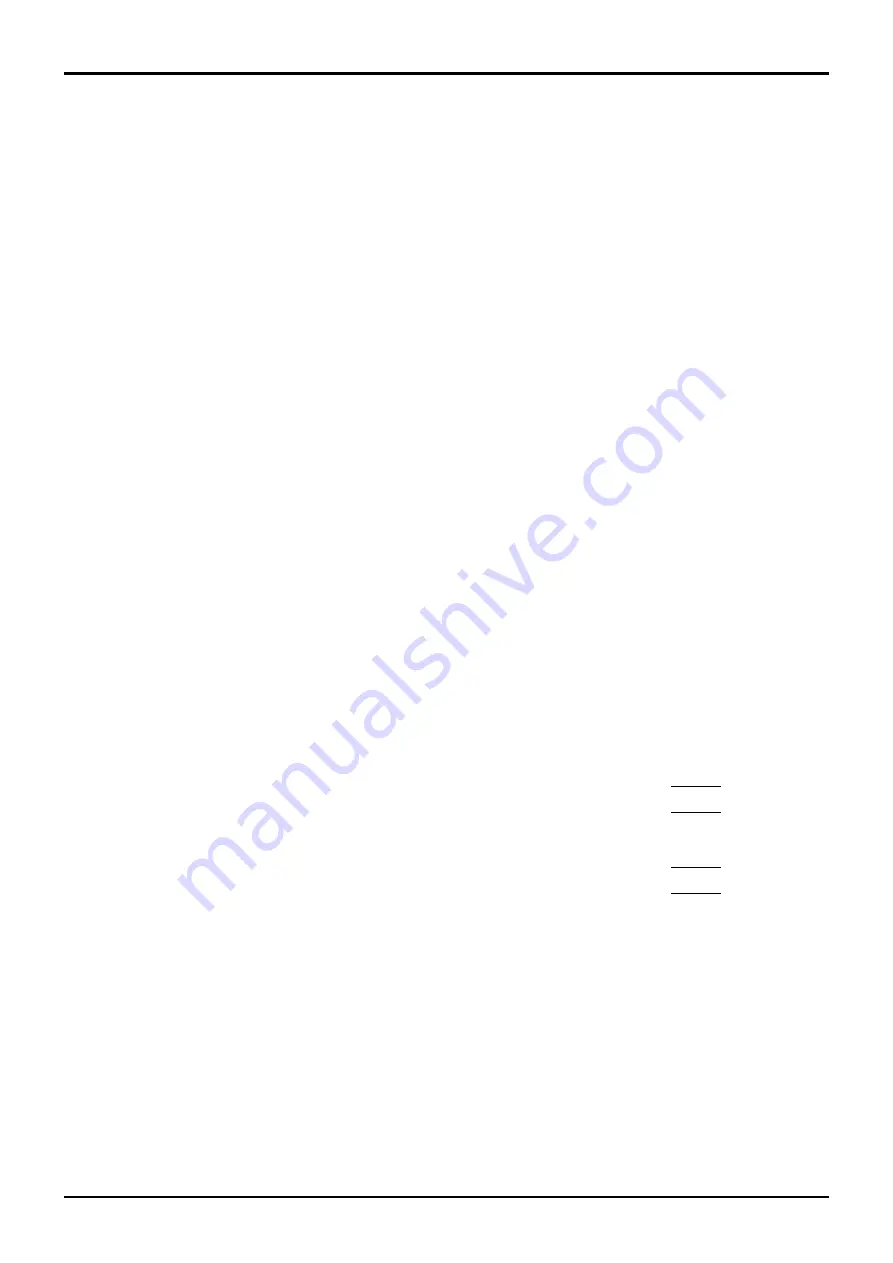
Variable Flow
Dismantling and Assembly
Before removing and dismantling the pump, make sure it is
the pump that is at fault. Complete all the necessary checks
as detailed in
Service Procedures, Variable Flow Pumps
.
Make sure that the exterior of the pump and working area is
t ho ro ug hly c leaned and f ree o f p o ssib le so urc es o f
contamination. Following removal of the pump from the
machine, transfer it to a clean dirt free environment ready for
dismantling.
The variable displacement pump has matched- ground
components. For this reason, some items will only be
available as a sub-assembly, for instance the barrel and
piston assembly.
All the ‘O’ rings, seals and bearings are available in a kit form
from your JCB Distributor.
Dismantling
Refer also to
Service Procedures, Variable Flow Pumps -
Renewing Drive Shaft Seal
.
1
Remove capscrews
1
(4 off) and detach the regulator
assembly
2
from the pump housing.
2
Mark the position of the port plate
3
to pump housing
4
.
3
Remove socket screws
5
, and remove the port plate
together with the valve plate
6
, control piston
7
and
stroking piston
8
. Hold the plate in position during
removal.
4
Remove taper roller bearing
9
and shim
10
from the
drive shaft
11
.
5
Remove the rotary piston assembly
12
from the pump
housing. Assembly includes shaft
11
, bearing
15
, and
cradle
16
.
6
Remove and discard port plate to pump housing ‘O’
ring
13
.
7
Remove bearing shells
14
and disc
17
.
8
Remove the outer bearing races (not shown) from the
pump housing and the port plate. Only remove the
races if they are damaged and unserviceable.
9
Lift the valve plate
6
off the port plate, do not lose the
dowel pins (not shown).
10
Remove and discard ‘O’ rings
18
.
11
Remove control piston
7
. Note that the control piston is
mounted on the same side as the regulator valve.
12
Remove the stroking piston assembly
8
.
Furt her d ismant ling and assemb ly of t he p ump is not
recommended.
Inspecting Parts
Generally check all pump parts for damage and/or wear. Any
parts that are scored or damaged must be replaced with new
ones.
The shaft ‘O’ ring grooves and all sealing faces must be free
of burrs and scores. During assembly, make sure that the
rotary piston group move freely. Renew all ‘O’ rings and
seals.
Assembly
Assembly is generally a reversal of the dismantle procedure,
but note the following:
The taper roller bearing must have a preload of 0.0 to
0.05mm (0.0 to 0.002in.). If the original bearing and shim is
being fitted no preload adjustment is required. If a new
bearing is installed a preload adjustment is required:
Preload Adjustment:
Install a setting shim of known thickness (as shown at
A
). The shim thickness must be manufactured to a
tolerance of ± 0.01mm (0.0004in.). In this example the
shim thickness is 1.5mm.
Fit the port plate item
3
and finger tighten the socket
screws. It is important that the socket screws are
tightened evenly and the port plate sits square.
Using feeler gauges measure the gap
B
between the
port plate and the pump housing
4
. Measure in more
than one position to establish the port plate is fitted
evenly. Obtain shim thickness (dimensions in mm):
Example measured gap
1.26
Subtract preload
- 0.05
Total
1.21
Known shim thickness
1.50
Subtract calculated preload
-1.21
SHIM THICKNESS
0.29
When the shim thickness has been calculated, remove the
setting shim
A
and fit the required shim (in this instance the
shim would be 0.29mm).
Note:
Setting shim
A
is not currently available as a service
t o o l. The shim (and t he c alc ulat ed shim ) c an b e
manufactured locally. Maintain a tolerance of ± 0.01mm
(0.0004in.).
The lubrication bore relief (item
C
) on the cradle must be
fitted on the pressure side of the pump.
Check the control piston and the stroking piston move
smoothly.
The regulator valve assembly is currently a non serviceable
part.
35 - 2
Section E
9803/3280
Section E
35 - 2
Issue 1
Main Pump