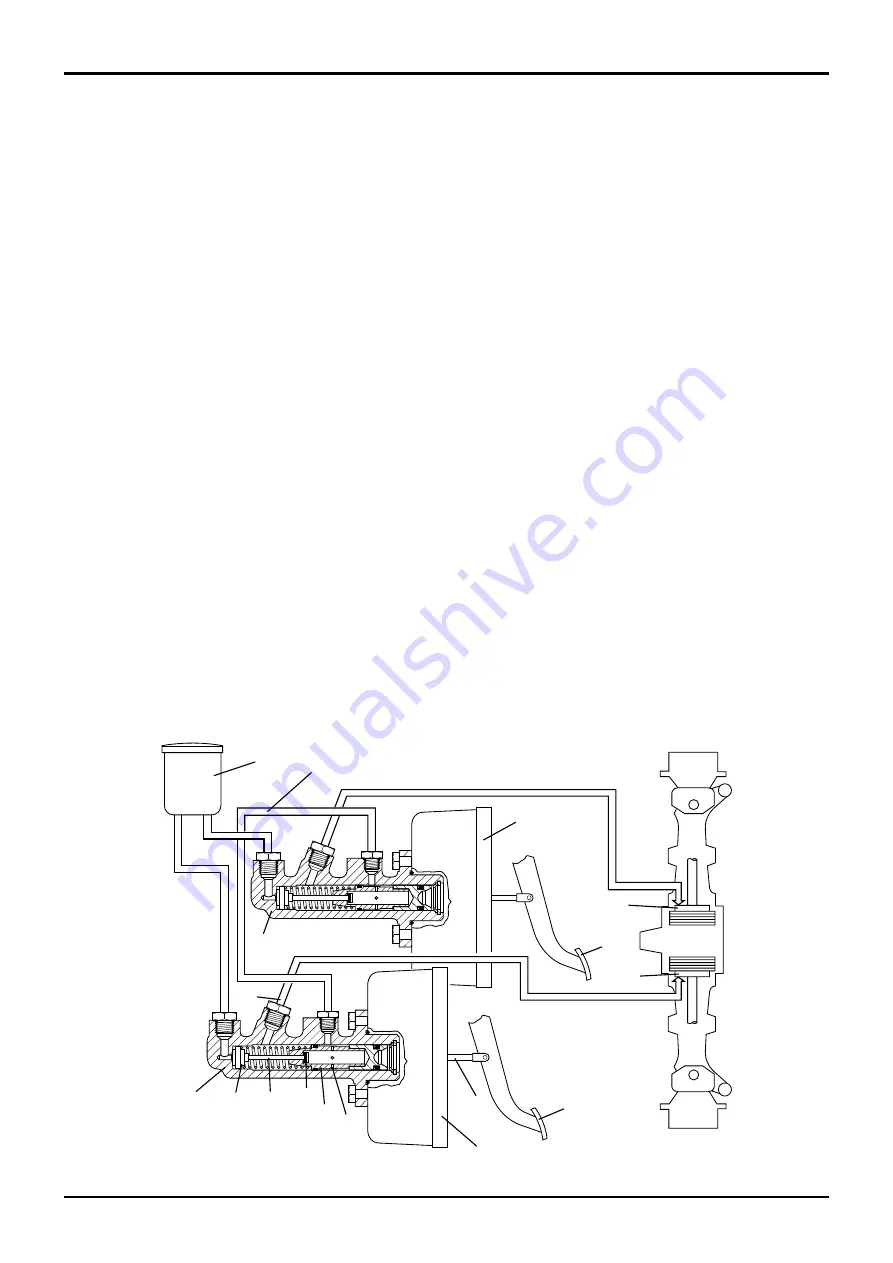
Compensating Master Cylinder
Description
Compensating master cylinders overcome the problem of
unequal wear between the right and left brake. The units
incorporate both master cylinder and compensating valve.
Each brake has its own master cylinder
A
,
A1
, brake pedals
B
,
B1
, servo units
N
,
N1
and associated pipework. Both
master cylinders have one common reservoir
C
.
N ot e :
Dual p ed al b rak ing is ap p lic ab le o nly t o 2WS
machines. 4WS machines have a single brake pedal.
Pedals Locked - Normal Operation
When the brake pedals are pushed down (the brake pedals
are mechanically locked together), rod
D
pushes the plunger
E
down the bore of the master cylinder. Pressurised oil
acting on centre valve seal
F
via valve stem
G
causes the
seal to close off the reservoir supply port. As the plunger
continues to move down the bore, pressurised oil flows to
the brake pack
H
via service port
J
and the associated
pipework.
Master cylinder
A1
operates in the same way to feed brake
pack
H1
.
With valve stem
G
at maximum travel, further movement of
plunger
E
causes valve
K
to lift off its seat. Both master
cylinders are interconnected via bridge pipe
M
, therefore
hydraulic pressure in both cylinders will be equal.
If the brake packs
H
and
H1
have worn equally, then the
amount of oil d isp lac ement b et w een c ylind ers w ill b e
minimal and the brakes will be applied evenly.
Pedals Locked - Compensating Operation
When the brake pedals are pushed down (the brake pedals
are mechanically locked together), actuation of the brake
packs
H
and
H1
is as described in Pedals Locked - Normal
Operation. If however, the brakes have not worn equally,
then the amount of fluid displaced from each master
c ylind er w ill vary and some form of c omp ensat ion is
required.
Pedal application moves plungers
E
down the bores of
master cylinders
A
and
A1.
Linings of brake
H
are brought
into contact before the linings of brake
H1
because they
have not worn as severely.
If further displacement took place at the linings, brake
H
w ould b e ap p lied b efore b rake
H1
. Therefore mast er
cylinder
A
begins to compensate for master cylinder
A1
.
Fluid is displaced from
A
to
A1
via bridge pipe
M
until the
p ressures are eq ualised . In t his c o nd it io n b o t h
compensating valves are open and both brakes are applied
evenly.
Pedals Unlocked - Normal Operation
When a single brake pedal is pushed down, rod
D
pushes
t he p lunger
E
d ow n t he b ore of t he mast er c ylind er.
Pressurised oil acting on centre valve seal
F
via valve stem
G
causes the seal to close off the reservoir supply port. As
the plunger continues to move down the bore, pressurised
oil flow s t o t he b rake p ac k
H
via servic e p ort
J
and
associated pipework, thus braking one wheel only.
With valve stem
G
at maximum travel, further movement of
p lunger
E
c auses valve
K
t o lift off it s seat . Fluid is
displaced through drillings
P
from the active cylinder
A
via
bridge pipe
M
to passive cylinder
A1
. Valve
K1
in the
p assive c ylind er is held on it s seat b y t he d isp lac ed
pressurised fluid.
3 - 1
Section G
9803/3280
Section G
3 - 1
Issue 1
Basic System Operation
A1
A
N
N1
B
B1
C
D
E
F
G
H
H1
J
K
M
P
A265570