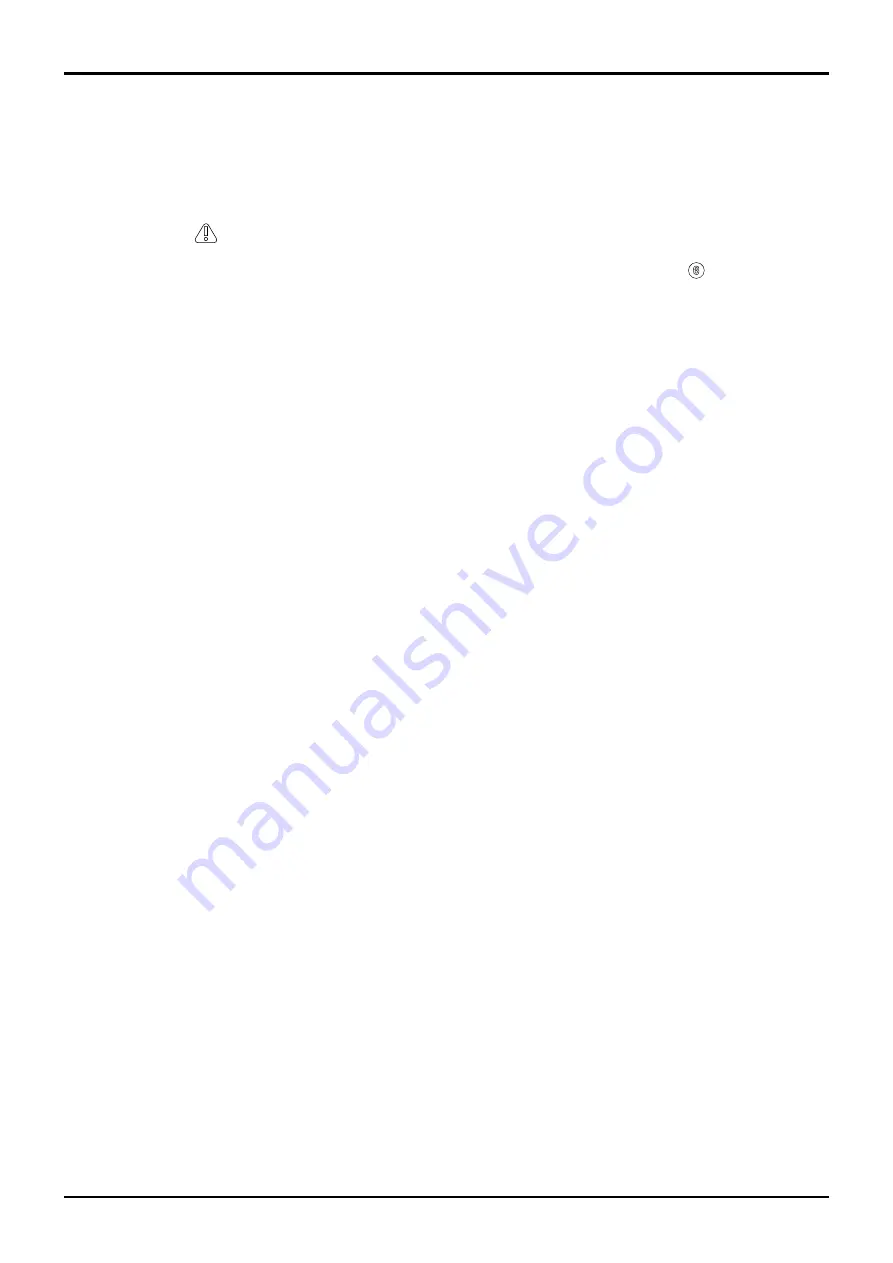
37 - 2
Removal and Replacement
Removal
1
Slew the kingpost to the centre and remove the boom
and dipper.
!
WARNING
Hydraulic fluid at system pressure can injure you. Before
disconnecting or connecting hydraulic hoses, stop the
engine and operate the controls to release pressure
trapped in the hoses. Make sure the engine cannot be
started while the hoses are open.
INT-3-1-11/1
2
Make sure that the slew lock pivot pin
11
is in its
stowage position (i.e. not fitted in the ‘slew lock’
position.
3
Working from the base up, disconnect the backhoe
hydraulic hoses, before disconnecting the hoses make
sure that they are labelled (to assist with reassembly).
4
Plug and cap all open hydraulic connections to prevent
ingress of dirt and loss of hydraulic fluid.
5
Remove thin nuts
1
(2 off per pivot pin) and remove
pivot pin retaining bolt
2
(2 off).
6
Remove the slew ram (eye end) pivot pins
3
(2 off) and
bearing liners
3A
.
7
Attach suitable lifting straps to the kingpost assembly.
Note that the weight of the kingpost casting is
approximately 130 kg (287 lbs).
8
Remove the boom lock assembly (see Boom Lock
Removal and Replacement in Controls, section D).
9
Remove thin nuts
4
(2 off) and remove retaining bolt
5
.
10
Remove the kingpost top pivot pin
6
.
11
Remove bolt
7
, washer
8
, and spacer
9
.
12
Remove the kingpost bottom pivot pin
10
.
13
Remove the kingpost casting
12
from the rear frame
and thrust washers
13
.
Inspection
Inspect the nickel bronze liner bearings
14
and
15
for signs
of damage, wear, scores or nicks etc. Use a suitable
mandrel (manufactured locally) to facilitate removal of the
liner bearings.
To ensure the drift is manufactured to the correct size, the
liner bearing dimensions are shown on the illustration. Note
that the dimensions are NOMINAL figures only and must not
be used to manufacture the liner bearings.
Replacement
Replacement is generally a reversal of the removal
procedures, however note the following:
To assist with the identification of 15ft 6in and 17ft
centremount kingposts the number
6
is stamped on the
kingpost to identify 60mm diameter bores.
Check for and remove any burrs and sharp edges on both
housing bore, bearing and pivot pin to minimise assembly
damage.
If necessary, use oil or suitable lubricant to facilitate
pressing-in bearing - to minimise scoring of mating face.
Bearings
14
and
15
have ‘lead-in’ diameters (noticeable with
a slight step), always install the smaller diameter first into the
pivot bore.
Thrust washers
13
come in different sizes to allow for
variations of castings.
Make sure that the boom base liner bearings
14
are fully
engaged in the boom base pivot bores. There must be a
recess of 5mm (3/16 inch) to allow for installation of the
seals
16
.
If fitting new liner bearings, assemble with a close fitting
shouldered mandrel. Refer to liner bearing sizes on the
illustration (nominal figures given).
Make sure that the liner bearings
15
are fully engaged in the
kingpost pivot bores. There must be a recess of 6mm (1/4
inch) to allow for installation of the seals
17
.
If a new kingpost casting has been installed, the boom lock
may need resetting, refer to the boom lock removal and
replacement procedures.
Seals
16
and
17
are lip seals, on reassembly make sure that
the seal lips face outward (shown in insets on the kingpost
pivot).
Make sure that thin lock nuts, items
1
and
4
are ‘just’ free
when locked into position.
Make sure that all pivot bores and pivot pins are clean and
greased when assembling. When fully assembled, apply
grease at each grease nipple before operating the machine.
Section B
9803/3280
Section B
37 - 2
Issue 1
Kingpost