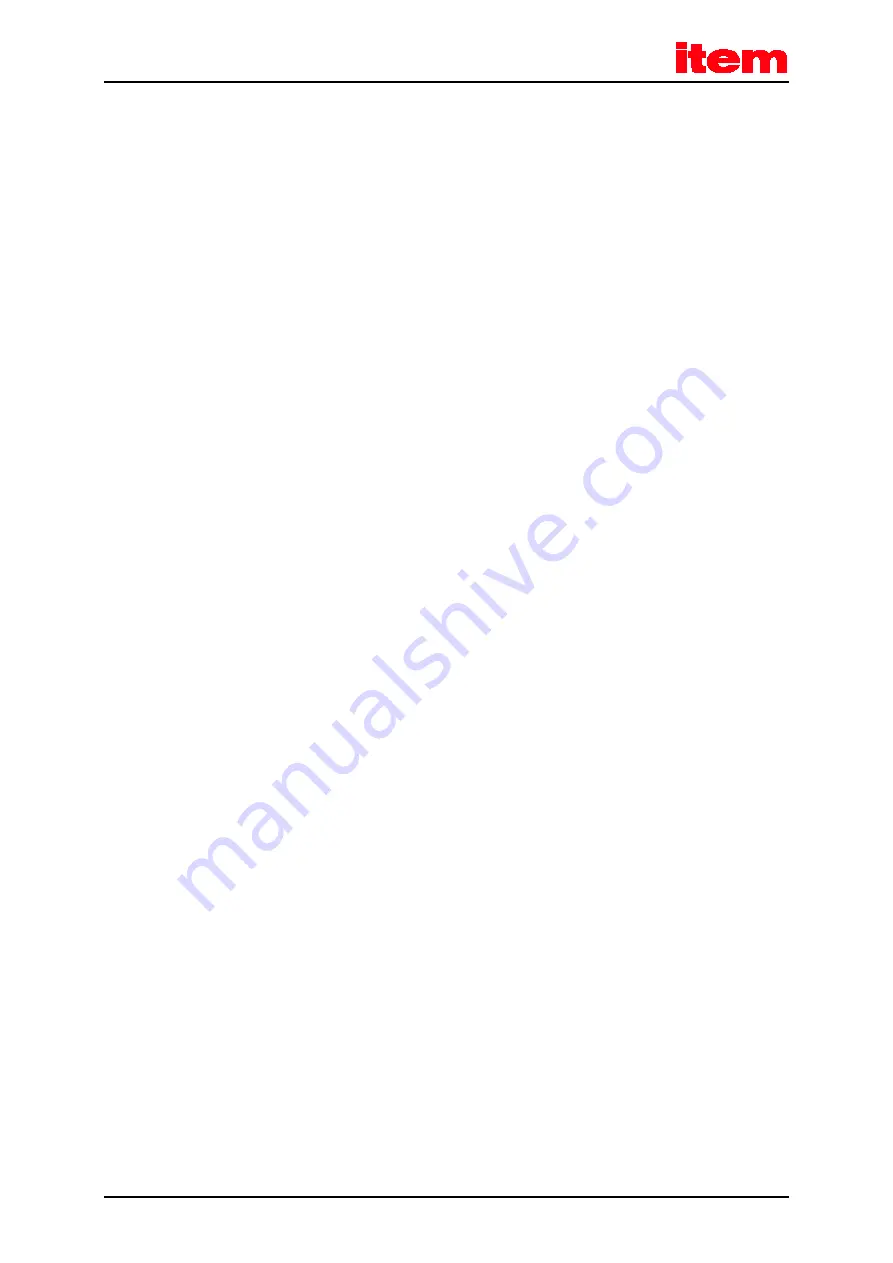
Electrical installation
Page 87
8.5.4
Cable type and configuration [X1]
The cable names that are stated refer to cables made by Lapp. They have proved to be reliable and are successfully used in
many applications. However, it is also possible to use comparable cables from other manufacturers, for example Lütze or
Helukabel.
LAPP KABEL UNITRONIC LiYCY (TP); 25 x 0.25 mm²;
∅
10.7 mm
shows the cable between the item Servo Positioning Controller C 3-Series and the control system. The cable that is
shown has two cable shields.
The outer cable shield is connected to PE on both sides. Inside the item C 3-Series, the connector housing of the D-Sub
connectors is connected to PE. When using metal D-Sub connector housings, the cable shield is simply squeezed underneath
the strain relief clamp.
Often, an unshielded cable is sufficient for the 24 V signals. In environments with high interference levels or in the case of long
cables (l > 2 m) between the control system and the item C 3-Series, item recommends using shielded control cables.
Despite the differential design of the analogue inputs of the item C 3-Series, using unshielded cables for the analogue signals
is not recommended, since interferences, e.g. caused by switching contactors, or output power stage interferences of the
converters can reach high amplitudes. They inject themselves into the analogue signals and lead to common-mode
interferences, which may lead to deviations of the analogue values.
In the case of a limited cable length (l < 2 m, wiring inside the control cabinet), the outer dual-sided PE shield is sufficient for
guaranteeing a trouble-free operation.
For optimal interference suppression of the analogue signals, the cores for the analogue signals must be shielded together
and separate from other cores. This internal cable shield is connected to AGND (pin 1 or 14) on one side of the item C 3-
Series. It can be connected on both sides in order to establish a connection between the reference potentials of the control
system and of the item C 3-Series. Pins 1 and 14 are directly connected to each other inside the controller.
8.5.5
Connection notes [X1]
The digital inputs are rated for control voltages of 24 V. The high signal level already ensures a high level of interference
immunity of these inputs. The item Servo Positioning Controller C 3-Series supplies an auxiliary voltage of 24 V, which may be
loaded with a maximum of 100 mA. As a result, the inputs can be activated directly via switches. Activation via the 24 V
outputs of a PLC is, of course, also possible.
The digital outputs are designed as so-called "high-side switches". This means that the 24 V of the item C 3-Series are actively
switched through to the output. Loads such as lamps, relays, etc. are thus switched from the output to GND24. The four
outputs DOUT 0 to DOUT 3 can be loaded with a maximum of 100 mA each. The outputs can also be led directly to the 24 V
inputs of a PLC.