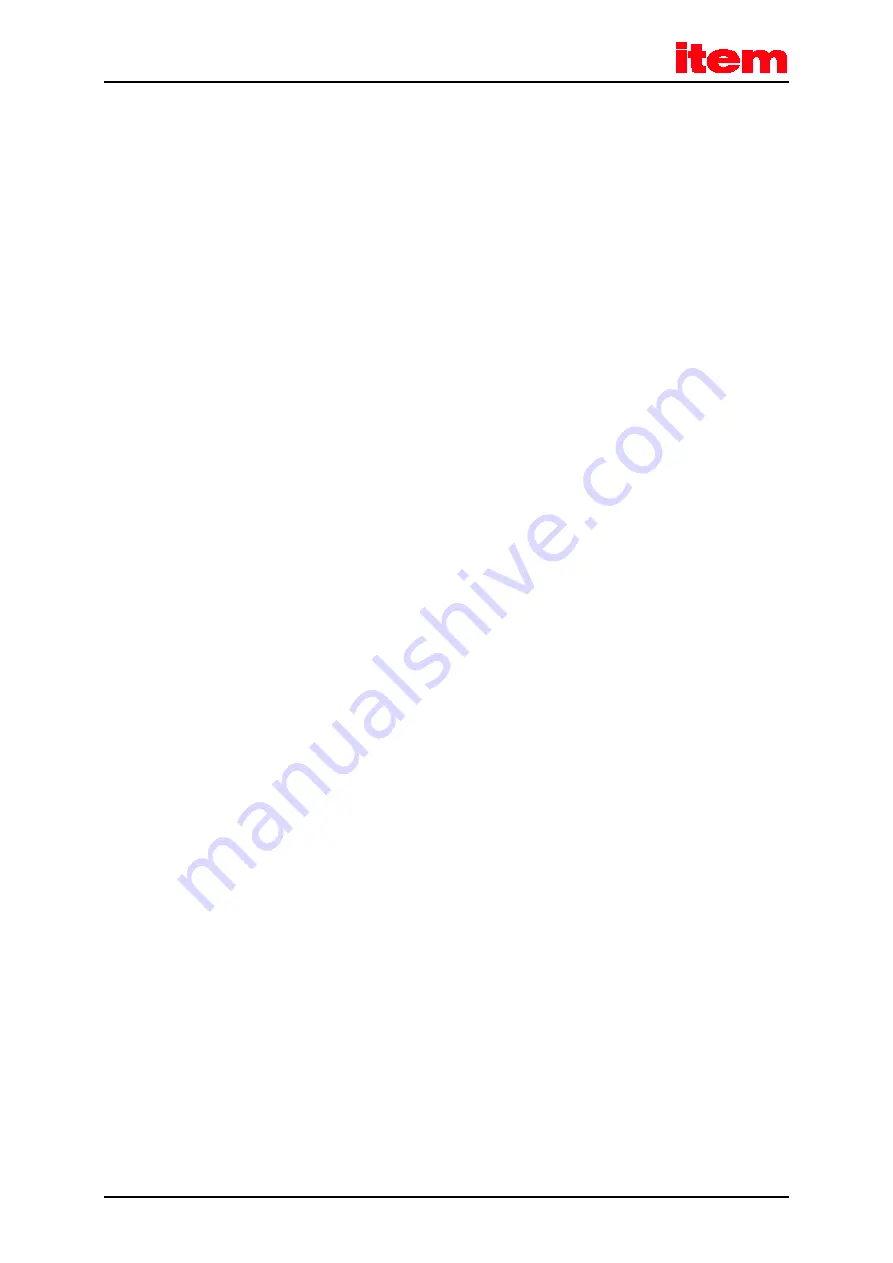
Functional safety technology
Page 64
6.1.2
Assignment of the DIP switch
The firmware of the item servo positioning controller C Series distinguishes itself by the universal support of various types of
fieldbuses. Since every fieldbus requires a specific hardware, the fieldbus is selected based on the fieldbus module that is
plugged into one of the technology slots. Depending on the identified technology module, the individual switches have an
influence on the activation and, where applicable, also on the configuration of this specific fieldbus. If the system does not find
any fieldbus technology module, the switch settings affect the fieldbus CAN whose interface is integrated into the basic device.
This means that if, for example, a Profibus module is installed, then the switch positions cannot be used to activate the CAN
communication.
The assignment of the individual switch positions to a specific function depends on the fieldbus that is used. As far as this is
possible, the function of a switch is the same for all of the fieldbuses such as, for example, switch 8 for activating/deactivating
the communication. The functions are listed in
The following general rules apply to the communication parameterisation of the technology modules that are listed in
Switch position = 0:
The activation of the communication, baud rate, and fieldbus address will be taken from the parameter data set or –
depending on the parameterisation – optionally also by an addition of digital inputs.
Switch position <> 0:
The configuration of the communication parameters via the DIP switch takes precedence over the corresponding settings
in the parameter data set:
Activation of the communication via DIP switch
Selection of the baud rate (if it can be adjusted) via DIP switch
Setting of the fieldbus address via DIP switch (addition to the basic node number taken from the parameter data set)
If the communication is deactivated via the DIP switch, it is optionally possible to reactivate or deactivate it via the item
Motion Soft
parameterisation software.
The fieldbus address that is set via the DIP switch is checked internally for validity and, if necessary, it is limited.
Fieldbus-specific functions (for example CAN: check for double node numbers) are configured via the settings in the
parameter data set.
If no fieldbus technology module is connected, the DIP switch is used for the configuration of the CAN hardware that is
integrated in the basic device.
The control of operating parameters for the RS485 communication that is also supported in the basic device is not
possible in favour of the parameterisation of the CAN interface.