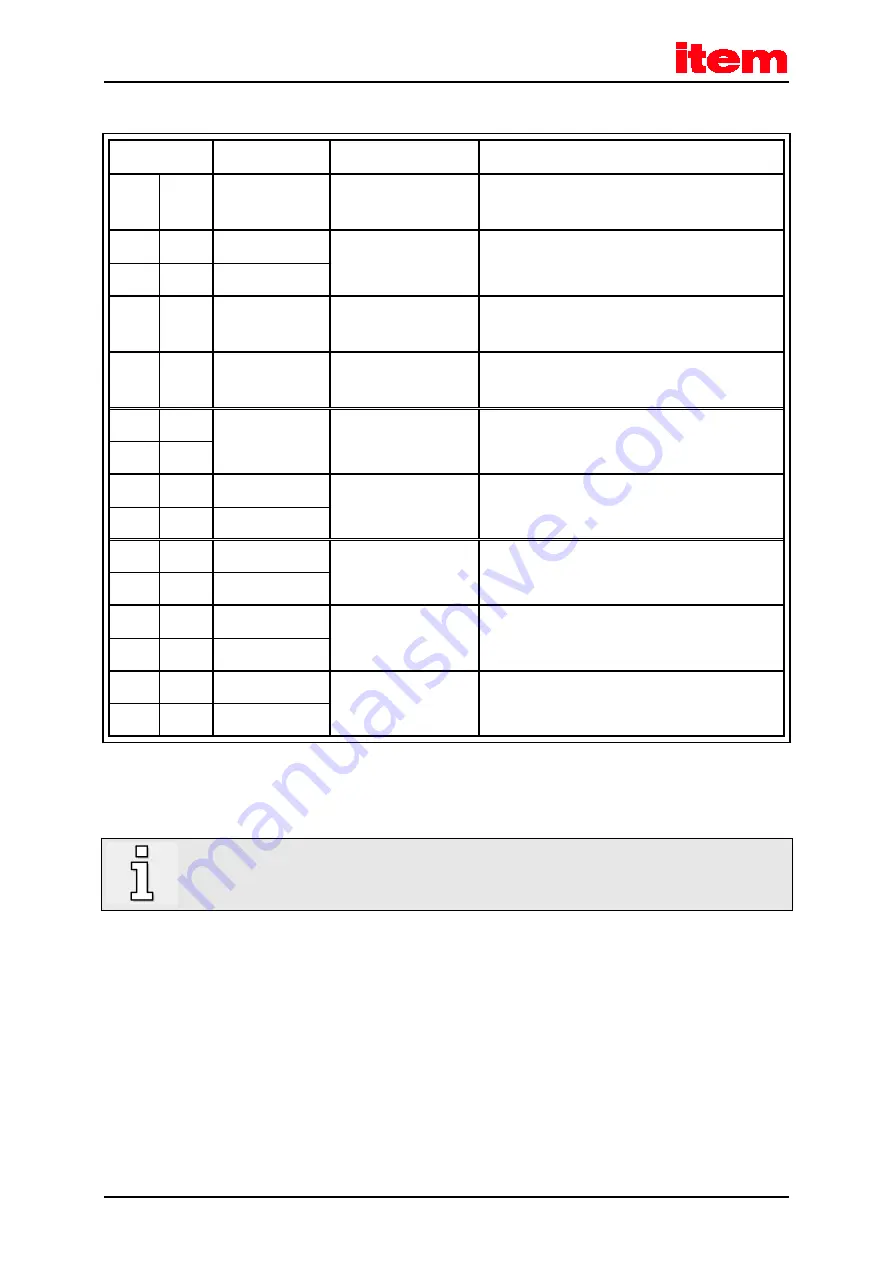
Electrical installation
Page 92
Table 39:
Pin assignment: incremental encoder with a serial interface (e.g. EnDat, HIPERFACE) – option [X2B]
Pin no.
Name
Value
Specification
1
MT+
+ 3.3 V / Ri = 2 k
Ω
Motor temperature sensor
1)
, normally closed contact,
PTC, KTY ...
9
5 V ... 12 V
R
I
≈
1 k
Ω
Sensor cables for the encoder supply
2
U_SENS-
10
US
5V / 12 V /
±
10%
I
max
= 300 mA
Operating voltage for high-resolution incremental
encoders
3
GND
0 V
Reference potential for the encoder supply and motor
temperature sensor
11
4
12
DATA
5 V
pp
RI
≈
120
Ω
Bi-directional RS485 data line (differential)
(EnDat/HIPERFACE)
5
#DATA
13
SCLK
5 V
pp
RI
≈
120
Ω
Clock output RS485 (differential)
(EnDat)
6
#SCLK
14
COS_Z0
2)
1 V
pp
/
±
10%
RI
≈
120
Ω
COSINE track signal (differential) of the high-resolution
incremental encoder
7
#COS_Z0
2)
15
SIN_Z0
2)
1 V
pp
/
±
10%
RI
≈
120
Ω
SINE track signal (differential) of the high-resolution
incremental encoder
8
#SIN_Z0
2)
1)
Please refer to
chapter 9 Additional requirements to be fulfilled by the servo positioning controllers for UL approval
page 113.
2)
Heidenhain encoder: A
=
SIN_Z0; B
=
COS_Z0
In addition, the outer cable shield of the angle encoder cable must be connected to the mounting plate of the
controller over a large contact area with the aid of shield terminal SK14.