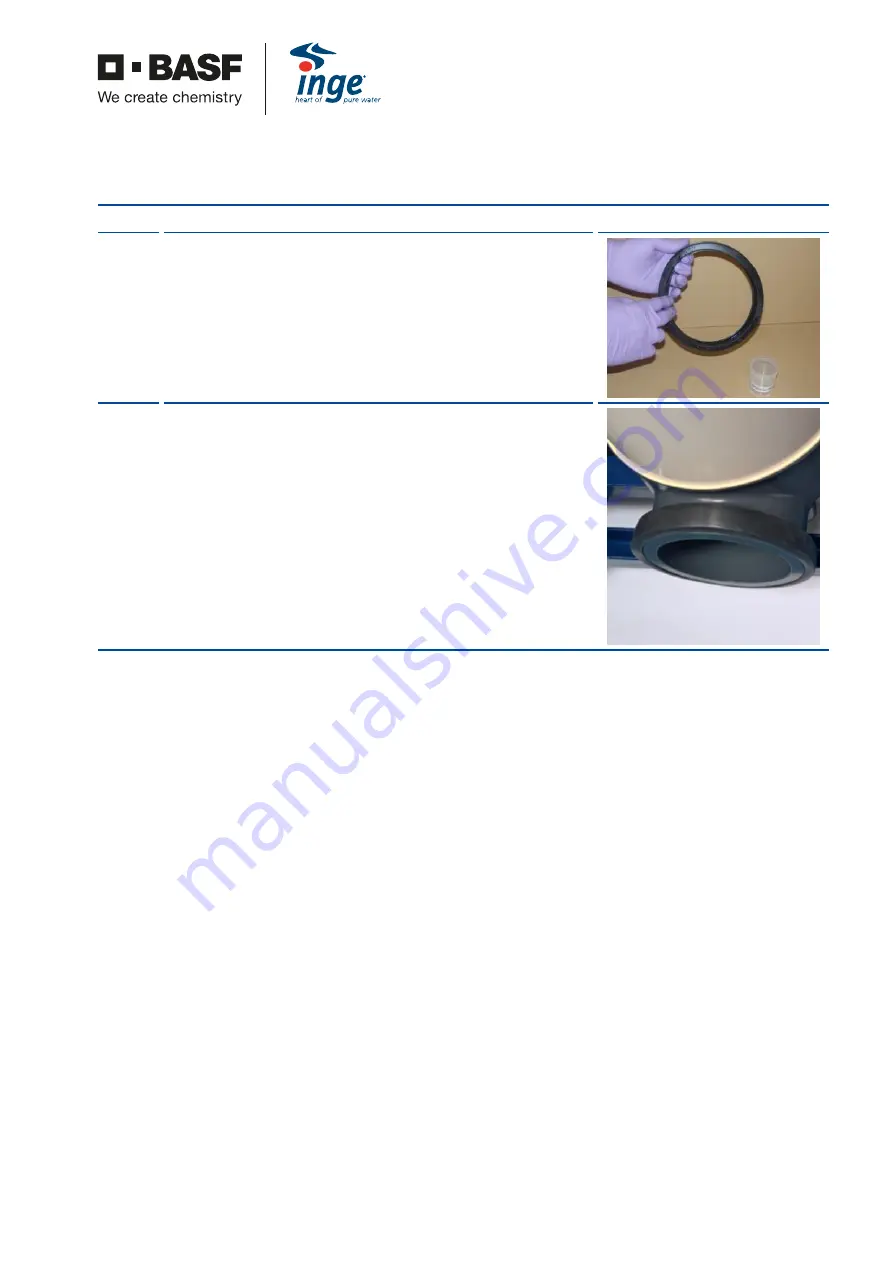
Installation / Assembly
T-Rack
®
3.0 Series
– Assembly Instructions 1.1(2019-03) E inge
Page 49 of 84
© inge GmbH
5.7.3
Mounting the Gaskets on the T Pieces
Step
Activity
Figure
1
Lubricate the gaskets with glycerin
a)
Remove the gaskets of the flexible composite
couplings 6”.
b)
Lubricate the gaskets with glycerin on the inside and
outside.
2
Mount the gaskets on the filtrate pipe
Number of persons: 2
a)
Continue holding the module in position to prevent tipping.
b)
Mount one of the lubricated gaskets over the opening of
the lower T piece, which will face the following module of
the T-Rack
®
.
c)
Push the gasket onto the T piece so it is flush with the end.
d)
Repeat procedures b) and c) for the upper T piece.