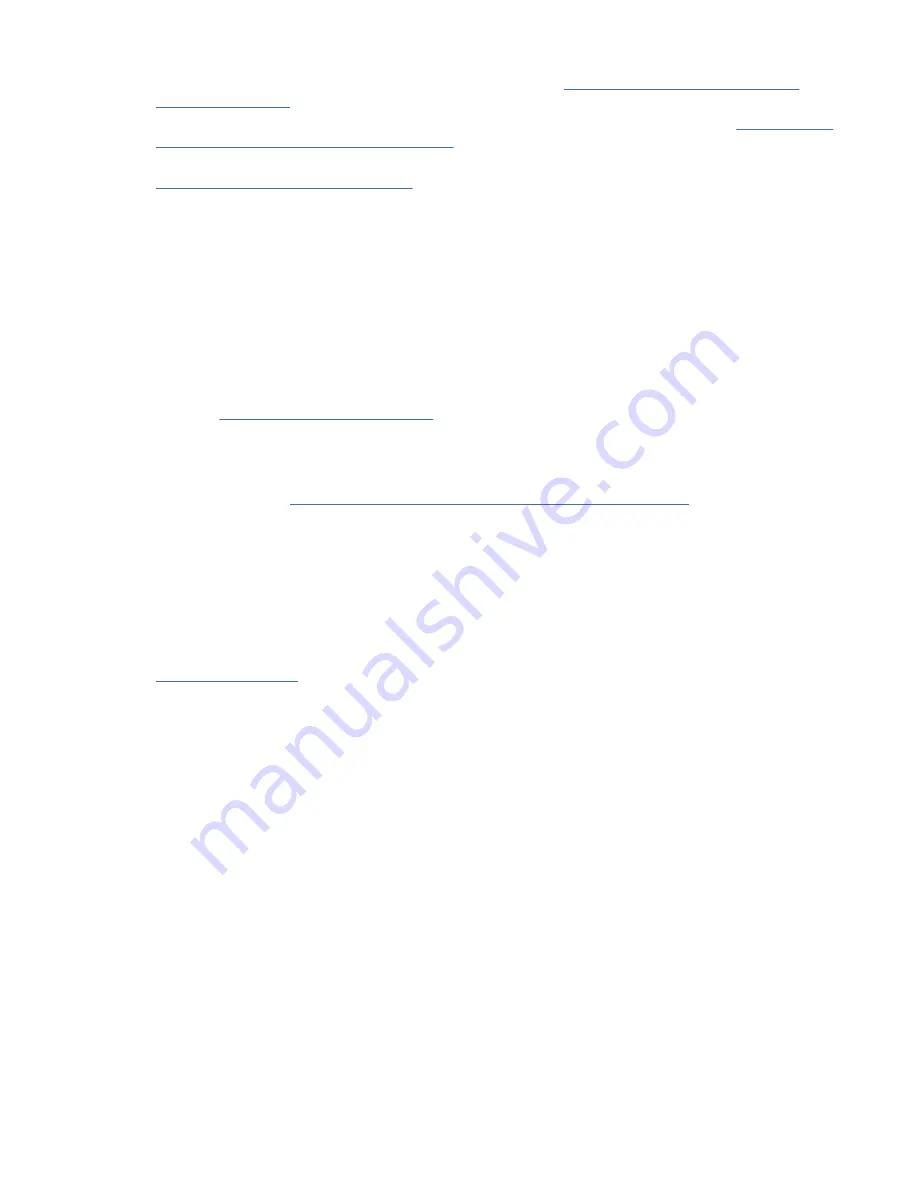
47. Connect the power distribution system. For instructions, see “Connecting the power distribution
front or rear AC electrical outlet” on page 48.
49. If you are not going to attach a front electrical outlet and you are installing rack doors, go to
“Attaching the rack doors” on page 77.
Connecting multiple racks with rack-to-rack attachment kit
You might need to connect multiple racks together. Use the procedure in this section to perform this task.
About this task
This topic describes how to connect multiple racks to each other using a rack-to-rack attachment kit. To
do this, you will need the rack-to-rack attachment kit.
To connect multiple racks with the rack-to-rack attachment kit, complete the following steps:
Procedure
1. Read the “Rack safety notices” on page 1.
2. If they are installed, remove the side panels from each rack. Remove side panels only from the sides
that will be attached to each other by completing the following steps:
a. If the side panel ruggedized kit is installed, remove the screw securing the panel. For more
information, see “Releasing the side panel with a ruggedized kit” on page 88.
b. If the security kit is installed, slide the security bar to the unlocked position.
c. Pull down on the two panel-release tabs.
d. Pull the panel up and away from the rack chassis. This motion will release the panel from the two
lower J brackets.
e. Store the side panels.
3. Remove the two Z brackets and the two J brackets. These brackets are used to hang the side panels.
4. Install the first two standoffs in the upper-left and lower-right corners of the first rack as shown in
Racks and rack features 23
Summary of Contents for 7014 T00
Page 1: ...Power Systems Racks and rack features IBM ...
Page 4: ...iv ...
Page 14: ...xiv Power Systems Racks and rack features ...
Page 151: ...Figure 98 Removing the remaining screws 7 Lift off the top cover Racks and rack features 137 ...
Page 167: ...Figure 110 Installing the inner hose panel Racks and rack features 153 ...
Page 184: ...170 Power Systems Racks and rack features ...
Page 195: ......
Page 196: ...IBM ...