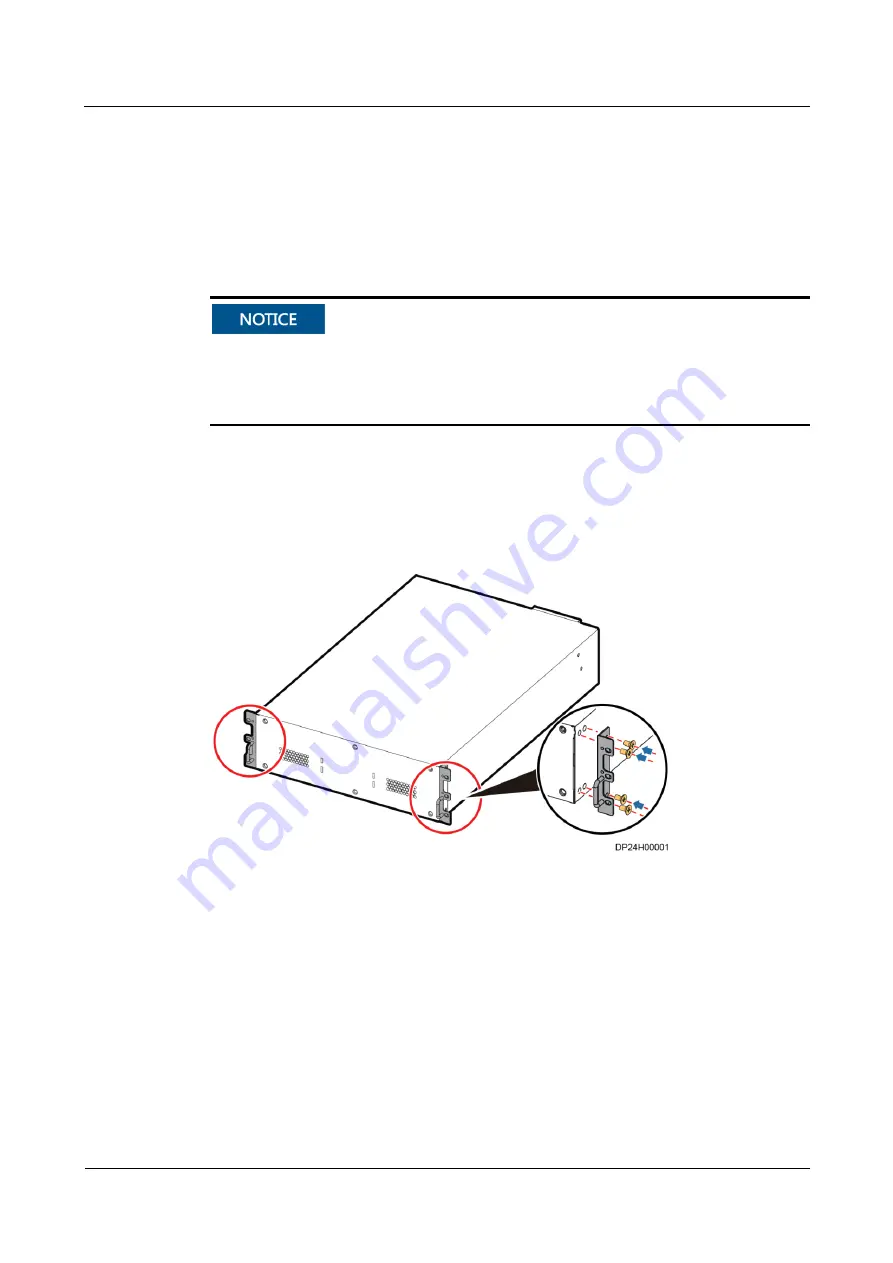
FusionModule800 Smart Small Data Center
Installation Guide (Six Fans)
3 Hardware Installation
Issue 10 (2019-12-20)
Copyright © Huawei Technologies Co., Ltd.
113
3.9 Installing a Battery Pack
Context
The battery pack is installed at the bottom of the IT cabinet adjacent to the Converged
Cabinet.
If no smart cooling product is installed in the IT cabinet, install battery packs from bottom
to top starting from the 1 U position above the cabinet bottom.
If a smart cooling product is installed in the IT cabinet, install battery packs from bottom
to top starting from the 12 U position above the cabinet bottom.
Procedure
Step 1
Take out mounting ears from the battery pack fitting bag, and install the mounting ears on the
battery pack using eight M4 screws, as shown in
Figure 3-96
Installing mounting ears
Step 2
Install floating nuts at the battery pack installation position.
Step 3
Install heavy guide rails at the battery pack installation position, as shown in