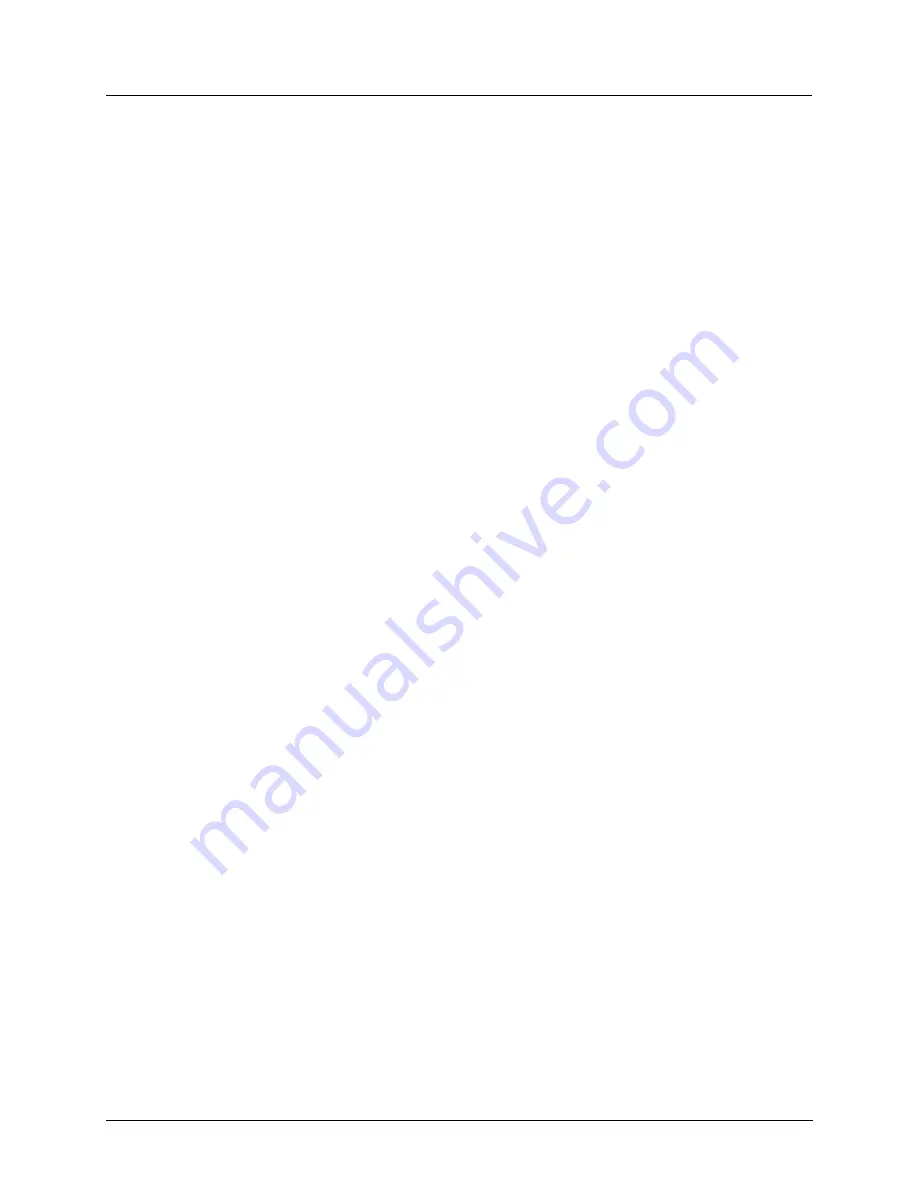
Main Menu
Troubleshooting a Comm Quality problem
Communications
Revision 9
900 Control Station User Guide
35
May 2014
Troubleshooting a Comm Quality problem
If a slave device is reporting a Comm Quality value of “BAD”, check the following items:
5.
Verify that the slave device is powered-up.
6.
Verify that the slave device is wired correctly.
7.
Verify that the slave device has the correct slave address.
8.
Verify that all slave devices on the link have a unique slave address.
9.
Verify that the slave device has the correct baud rate and parity settings.
10.
Verify that all slave devices on the link have the same baud rate and parity settings.
11.
Verify that the slave is set-up for half-duplex operation.
12.
If all slave devices report a BAD status, check the physical connection of the link to the controller’s
RS-232 port. If this connection is OK, check the connection to each slave device on the link.
13.
If there is more than one slave device on the link, verify that the RS-232/RS-485 converter box is
working correctly.
14.
Verify controller is set to unterminated for RS-485 communications.
Troubleshooting Data Link Errors
Data Link Errors can be caused by electrical noise, physical wiring problems, or incorrect configuration
settings. If a Master or Slave device is reporting Data Link Errors, check the following items:
15.
Verify that the physical wiring of the communication link is correct.
16.
Verify that the physical wiring is shielded from electrical noise.
17.
Verify that all devices on the link have the correct baud rate and parity settings.
18.
Verify that all terminating resistors are installed properly. Verify that the ohm-value of the
terminating resistors is correct.
19.
Verify controller is set to unterminated for RS-485 communications.