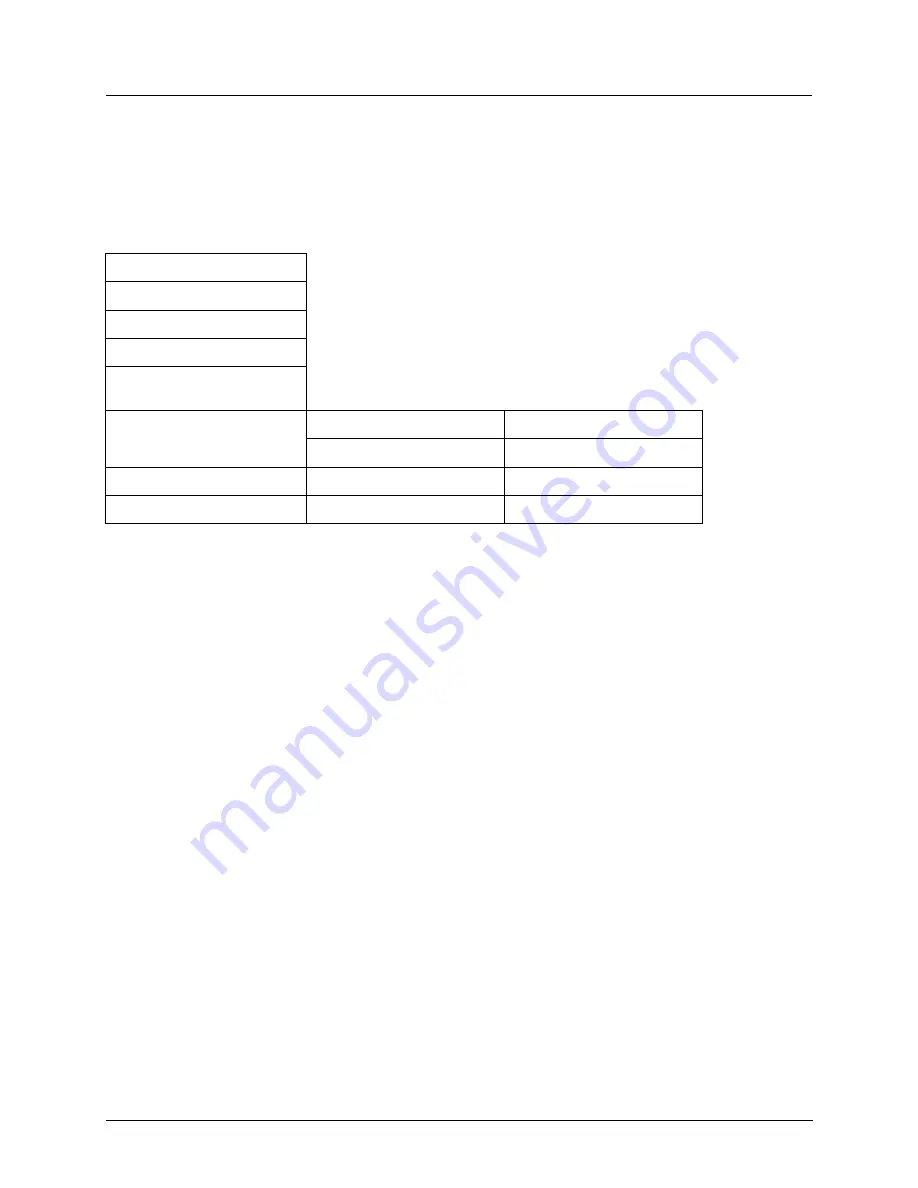
Main Menu
Communications
Menu Overview
22
900 Control Station User Guide
Revision 9
May 2014
Communications
Menu Overview
Menu
Submenu
Serial Port S1 (p. 22)
Serial Port S2 (p. 22)
Ethernet Port E1 (p. 27)
Ethernet Port E2 (p. 27)
Expansion Port
Communications (p. 29)
Modbus Slave Devices (p. 31)
Modbus Slave Device
n
Modbus Slave
n
Status
Modbus/TCP Slave Device
n
Modbus/TCP Slave
n
Status
Host Connections (p. 32)
Host Connection
n
Host Connection
n
Status
Peer Connections (p. 33)
Peer Connections
n
Peer Connection
n
Status
NOTE:
The 15" control station can be programmed using only the Ethernet, serial and compact flash card.
The 900CS15's USB programming port conflicts with today’s PCs so it's advisable to use Ethernet ports for
configuration changes. This problem has been observed only with the 15" control station; the 10" control
station has not shown any problems with its USB ports.
Serial Port S1/S2
The Serial Port S1 and Serial Port S2 screens both show Statistics (Table 6) and Settings (Table 8) for those
controller serial ports.
Table 9 shows the relationship between the setup parameters and each protocol.
The controller’s Serial Port S1 can be set-up as an ELN Configuration port, a Modbus Master port, or a
Modbus Slave port. The ELN protocol allows the controller to communicate with the Process Control
Designer package on the PC using the proprietary ELN protocol. The Modbus Master protocols allow the
controller to act as a Modbus Master, retrieving data from other instruments that have been configured as
Modbus slave devices. The three Modbus Slave protocols allow the controller to act as a slave to various
host devices, including a PC running HC Designer.
The information presented in Table 6 and Table 9 also applies to Serial Port S1 when a Redundant
Controller is used.