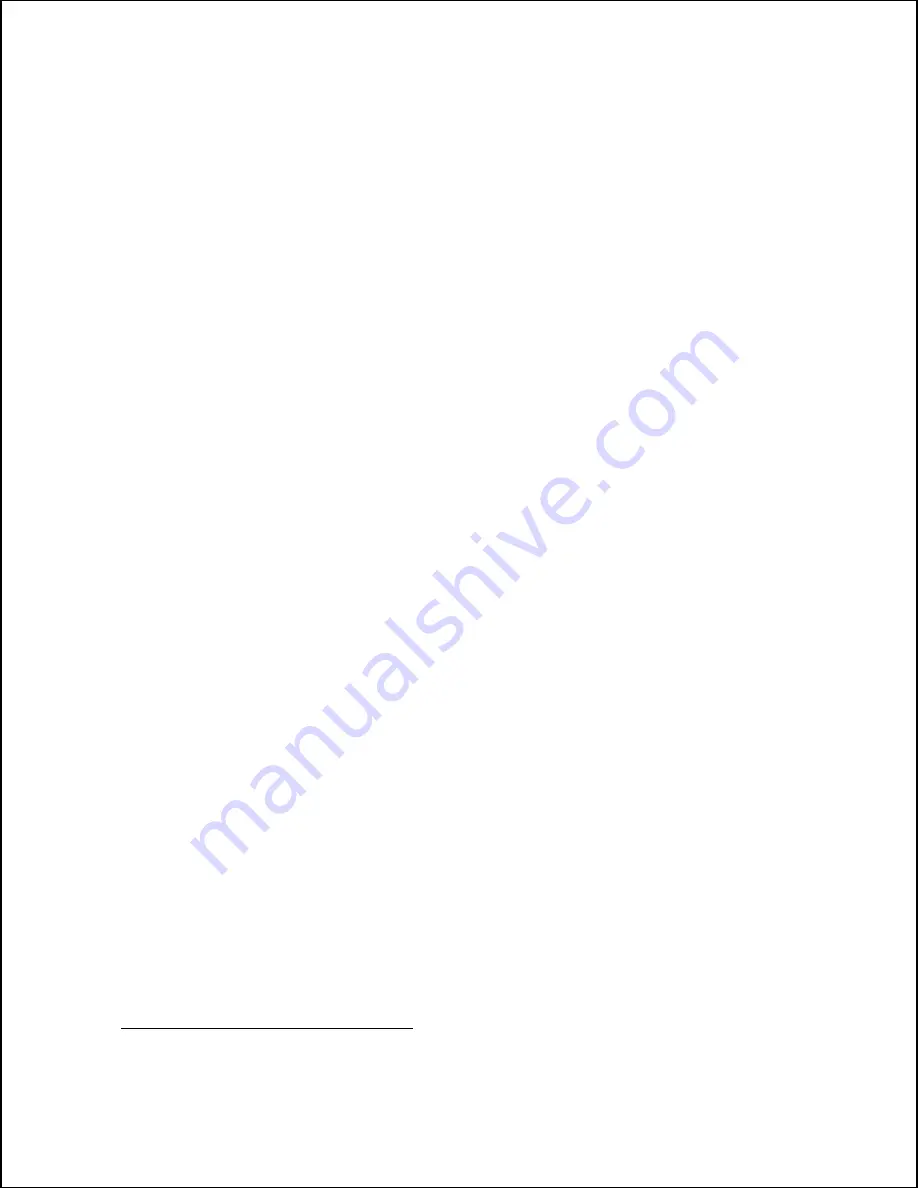
c. Adjust the AVERAGE CURRENT overload R42 until the
OVERCURRENT LED lights AMBER.
d. Modulate the transmitter with 100 Hz at 100%.
e. Increase the audio in 1 dB steps. The PA current should not
increase further than near full scale on the PA current
meter.
f. Further increase the audio level until the transmitter shuts
off and recycles back on. If the audio level is not reduced,
the transmitter may shut OFF and stay OFF at this time.
g. The Overcurrent LED will illuminate RED and can be reset
from the ColorStat™ panel.
h. Turn the transmitter back ON and verify that the transmit-
ter takes at least +10 dB of audio overdrive before shutting
OFF.
5.6.7.4.1
Average Current Overload Test
a. Modulate the transmitter 100% with 400 Hz sine wave.
b. Verify it will continue to operate with at least +10.0 dB
over 100% audio overdrive.
c. The transmitter should trip OFF from a Current Overload
with between 10.0 and 15.0 dB of overdrive.
d. The supply current should not exceed 250 amperes during
the test.
5.6.7.4.2
Program Modulation Test
If OVERCURRENT overloads occur during program modula-
tion conditions, the PEAK CURRENT OVERLOAD may be
backed off 1-2 turns, but the voltage at TP7 must NOT exceed
11.5 VDC.
5.6.7.5
Power Supply Protection Overload R86
a. Operate the transmitter at maximum output power. Modu-
late the transmitter with 120 Hz at 100% modulation.
b. Increase the audio modulation 0.5dB (6%). Note: Use
100Hz modulation if operating at 50 Hz AC line frequency.
c. Adjust R86 clockwise until the transmitter shuts OFF with
a Power Supply Protection Overload. Note hat the Supply
Fault LED on the ColorStat™ panel is RED and that the
transmitter will not recycle for this fault.
d. Adjust R86 1/4 turn counter-clockwise.
e. Depress the reset button to reset the fault indicator to
GREEN.
NOTE
It is not required to depress the RESET button on the Color-
Stat™ to restart the transmitter. The RESET button only clears
the fault indication.
f. Depress the HIGH power button to operate the transmitter
at maximum output power.
g. Modulate the transmitter at 100% with 120/100 Hz. The
transmitter should not trip OFF with a Power Supply fault.
5.6.8
Driver Encoder/Temp Sense Board (A19)
If the power supply circuits on the original board are operational,
measure the following Test Point voltages on the original board
and adjust the new board to the same voltages:
•
TP1 (R17): Driver Threshold Reset
•
TP2 (R19): Driver Threshold ON
•
TP3 (R49): Temp Cal
•
TP4 (R50): Step 1 Temp
•
TP5 (R51): Step 2 Temp
•
TP6 (R60): Temp Thresh
•
TP11 (R98): Air Flow
After the replacement board voltages have been calibrated, en-
sure that JP1, JP2 and JP3, J5, S1 and S2 are in the correct
position to correspond to the original board. The transmitter is
now ready for operation.
If it is necessary to calibrate the replacement board, use the
following procedure:
5.6.8.1
Over Temperature Circuits
Set the Over Temperature circuits on the Driver Encoder/Temp
Sense Board as follows:
NOTE
The transmitter should be OFF and at room temperature when
the Over Temperature circuits are calibrated.
a. Adjust R49 to set TP3 for 2.73 VDC.
b. Determine the ambient temperature in degrees centigrade
and multiply this value by 0.1 (25 degrees C X 0.1 = 2.5).
c. Adjust R50 to set this value at TP4, and R51 to set this
value at TP5.
d. Set the voltage at TP-6 to 7.0 VDC with R60.
5.6.8.2
Auto Driver circuits
The Auto Driver circuit should turn the Auto Driver Module D7
ON when the D8B voltage on the RF MULTIMETER reaches
maximum, approxi115 VDC. The Auto Driver circuit
should turn the Auto Driver Module D7 OFF when the D8A
voltage on the RF MULTIMETER reaches zero.
Set the Auto Driver circuit thresholds on the Driver En-
coder/Temp Sense Board as follows:
a. Turn the transmitter ON at LOW power.
b. Make sure S2 on the Driver Encoder/Temp Sense Board is
in the AUTO position
c. Locate the Driver Supply Regulator in the Driver Compart-
ment. Move S1 to the OPEN LOOP position.
d. Record the D8A and D8B voltage on the RF MULTIME-
TER.
e. Adjust R2 on the Driver Supply Regulator until the D8B
voltage reaches maximum, +115 VDC.
f. Adjust R17 on the Driver Encoder/Temp Sense Board until
the AUTO DRIVER LED DS1 illuminates.
g. Adjust R2 on the Driver Supply Regulator until the D8A
voltage reaches zero.
h. Adjust R19 on the Driver Encoder/Temp Sense Board until
the AUTO DRIVER LED DS1 turns OFF.
i. Adjust R2 on the Drive Supply Regulator so the D8A and
D8B voltages are the same as recorded at the beginning of
the procedure.
j. Return S1 on the Driver Supply Regulator to the CLOSED
LOOP position.
Section V - Maintenance
Rev. Z1: 06-02-00 Additional info to ECN 46105
888-2297-002
5-13
WARNING: Disconnect primary power prior to servicing.