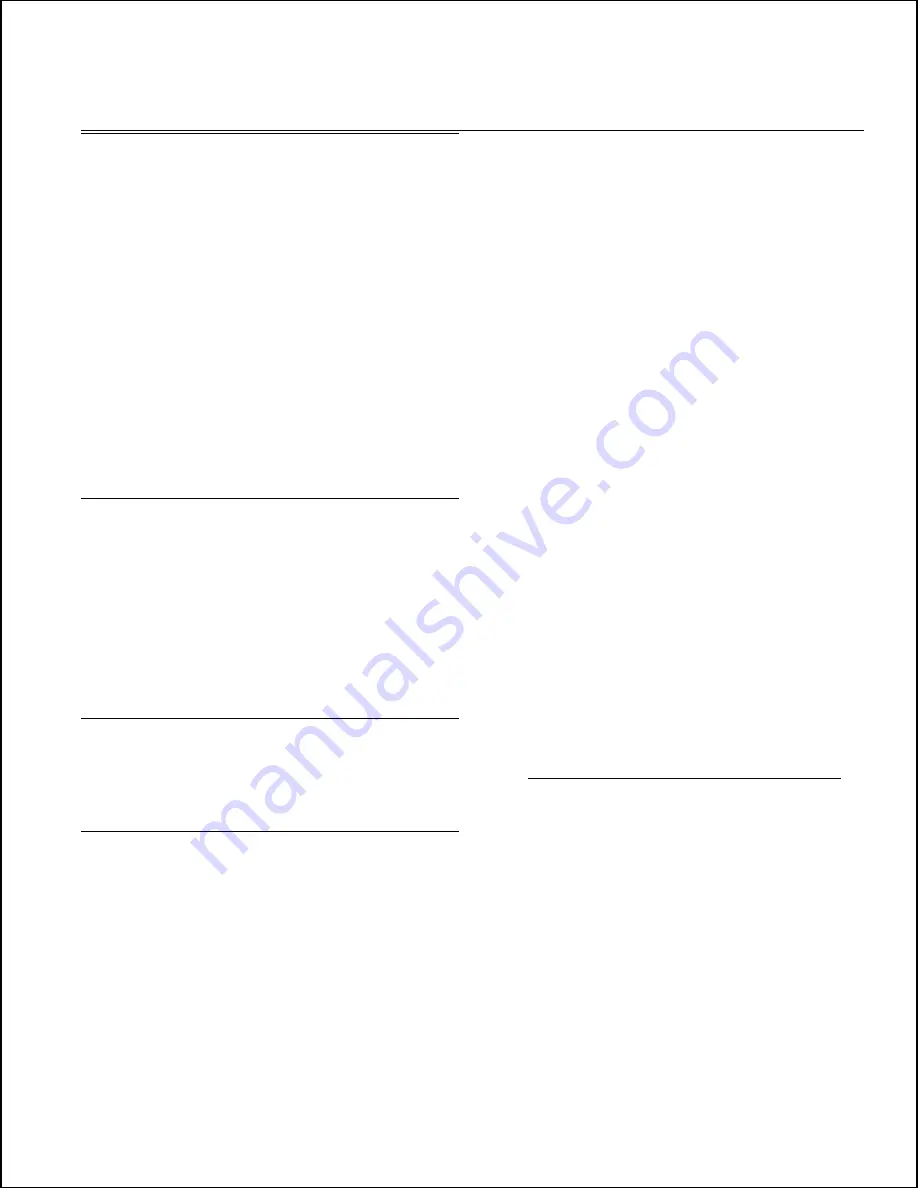
Section P
Controller (A38)
P.1
Introduction
This section describes the Controller. Topics include Function,
Location, Block Diagram Description and Circuit Descriptions.
The description is divided into functional groups of circuits, as
follows:
a. Turn-on/Turn-off Control Logic.
b. Power Control Logic.
c. Interlock Status Fault Logic.
d. +5B Reset Circuit.
e. Power Supplies (+5, +15, -15 Volt regulators).
f. Supply Fault Logic.
g. Analog Metering Buffer/Drivers.
h. AC Power Recycle.
Refer to the Controller schematic, 843-5400-091, in the Drawing
Package.
P.2
Function
The Controller has two primary functions: Local/Remote control
of the transmitter ON/OFF sequence and power adjustment.
Overload and Fault detection circuits on the LED Board generate
inputs to these circuits to provide transmitter protection. Low
voltage regulators 5 Vdc, +15 Vdc and -15 Vdc for
circuits on the Controller and LED Board. Additional circuits
include meter drivers for Forward Power, VSWR and Supply
Voltage.
P.3
Location
The Controller is located on the back of the Center Control
Compartment door.
P.4
Block Diagram Description
Refer to Figure P-1, “Block Diagram, Turn-On/Turn-Off Control
Logic” and Figure P-3, “Power Control Section, Block Dia-
gram”, for the following discussion.
The power control logic circuits accept Command Inputs and
generate a “TURN-ON REQUEST” to the turn-on/turn-off con-
trol logic circuits. The power control logic also provides a 3-digit
BCD (Binary Coded Decimal) power control output to the Ana-
log Input Board.
Command inputs are OFF, HIGH, MEDIUM, LOW, RAISE and
LOWER. Command inputs can be LOCAL, REMOTE, or
FAULT-INDUCED. The front panel controls are LOCAL com-
mand inputs. Inputs from remote control equipment or extended
control panels to the External Interface terminal board (TB1) are
REMOTE inputs. The transmitter’s fault and overload sections
can generate OFF commands, VSWR induced LOWER com-
mands, or temperature induced LOWER Power commands.
The transmitter turn-on/turn-off control logic provides drive
signals for step-start relays K1 and K2 and also provides logic
signals to inhibit various overload functions during the step-start
sequence and when the transmitter is OFF.
The transmitter has no filaments to warm up, so a “TURN ON
REQUEST” from the power control logic immediately energizes
K1 to start the PA Power Supply step-start sequence. Primary AC
is initially applied to the transformer through surge limiting
resistors. The Power Amplifier stage is held off during this time,
so that the PA Power Supply is not loaded down as the filter
capacitors charge. The operation of K1 is checked; if it has
closed, the turn-on sequence continues. After a short time delay,
rf drive level is checked. If drive is not correct, the transmitter is
turned off immediately.
If rf drive level is correct, contactor K2 closes to bypass the
limiting resistors and power control circuits become completely
operational. After an additional short time delay, the “PA OFF”
logic signal is released so that the transmitter begins operating at
the selected power level (High, Medium or Low power).
If a fault occurs during the turn-on sequence, turn-on may either
be aborted immediately or may time-out without completing the
turn-on sequence.
An “OFF” input, also from the power control logic, immediately
de-energizes high voltage supply contactors and generates logic
signals to inhibit other transmitter functions. A Type 1 or Type 2
Fault input logic signal from the LED Board has the same effect
as an “OFF” input. If an “OFF” or Type 1 or Type 2 fault signal
occurs during the step-start (turn-on) sequence, the sequence is
immediately stopped or aborted.
P.4.1
Transmitter Turn-on/Turn-off Control Logic
Refer to Figure P-1, Block Diagram “Turn-On/Turn-Off Control
Logic.”
P.4.1.1
Transmitter Turn-on Sequence
When the HIGH, MEDIUM, or LOW switch is pressed, the
button illuminates and contactor K1 energizes. After approxi-
mately 1.1 seconds, contactor K2 energizes and power output
comes up to the preset level. After approximately one-half sec-
ond, contactor K1 de-energizes.
a. COMMAND INPUT. When a HIGH, MEDIUM, or LOW
power command is given (either a LOCAL or a REMOTE
input), a “TURN-ON REQUEST” is generated by the
Power Control logic.
b. TURN-ON REQUEST. The Turn-On Request (low-to-
high transition) triggers the “B” input (pin 2) of U56A.
c. TURN-ON PULSE. When U56A is triggered, a 1.6 second
logic HIGH “Turn-On Pulse” is generated at the Q output
and drives step-start contactor K1 . A 1.6 second logic
Rev. S: 05-02-97
888-2297-002
P-1
WARNING: Disconnect primary power prior to servicing.