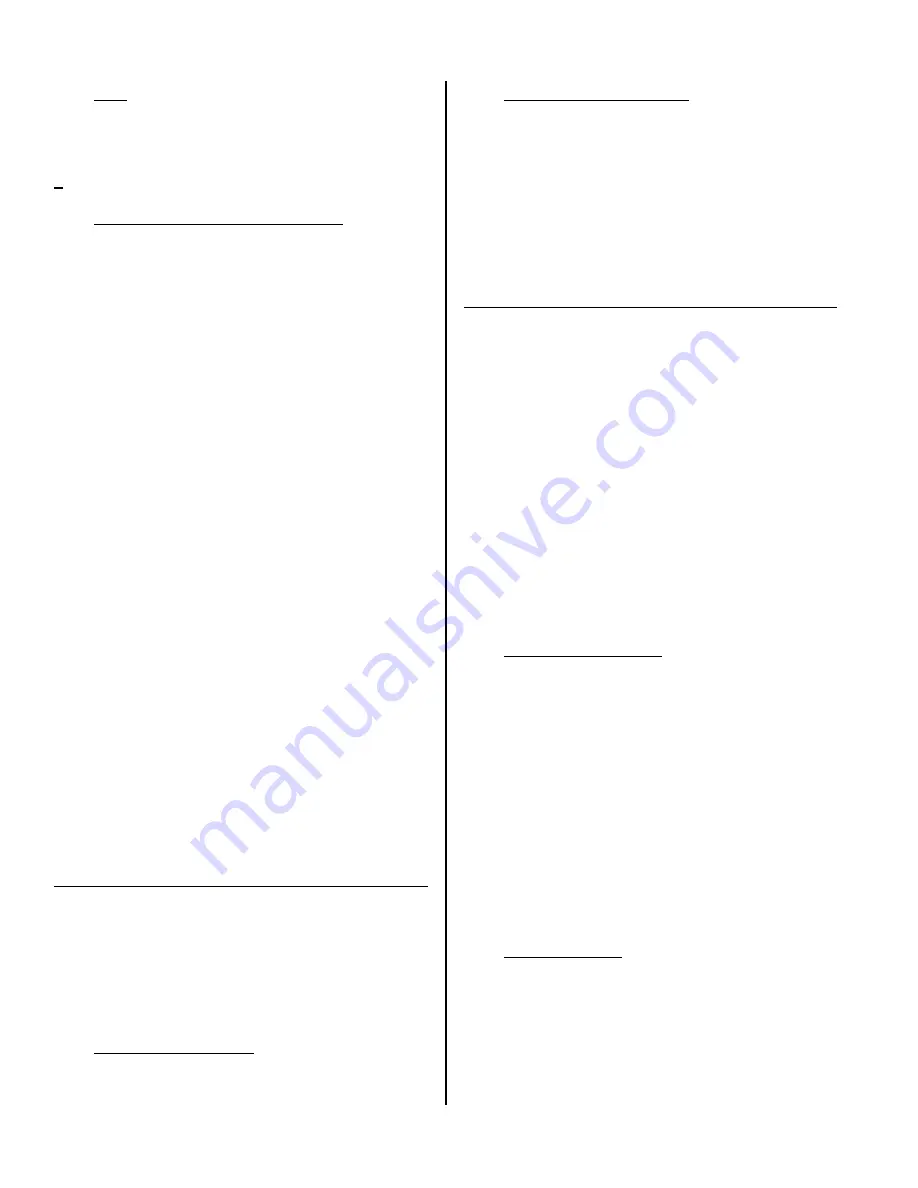
4.5.1
Fans
Four fans, B1 through B4, are used in the DX-25U for transmit-
ter cooling. Each fan uses a 1/3 HP, dual voltage 3-phase motor,
powered when T1 is energized. T1 primary taps also function as
an auto transformer when the line feed is greater or less than the
+10% tolerance of the motor.
4.5.2
Air Flow and Temperature Sensing
Air flow reduction or loss and over temperature conditions are
sensed by circuitry located on the Driver Encoder/Temperature
Sense Board. The two separate and independent circuits are
detailed in SECTION S. A brief description of their system
operation is as follows:
4.5.2.1
Air Flow Sensing
Circuitry on the Driver Encoder/Temp Sense Board will cause
the AIR INTERLOCK LED on the ColorStat™ panel to illumi-
nate AMBER if one fan has failed, or if the air flow is reduced
to that level. A “Blower Fault” status output is generated by the
External Interface for remote monitoring. Solid state air flow
device U17 on the Driver Encoder/Temp Sense Board sends an
active LOW signal to the LED Board if two fans fail or if air
flow is further reduced. The AIR INTERLOCK LED on the
ColorStat™ panel indicator will illuminate RED and the trans-
mitter will turn OFF. An “Air Fault” status output is generated
by the External Interface for remote monitoring.
4.5.2.2
Temperature Sensing
Two temperature probes are attached to the heat sinks of PA
Modules RF1 and RF2. The temperature is sensed by circuitry
on the Driver Encoder/Temp Sense Board which sends a
“LOWER” power command signal to the LED Board if the
temperature rises above a preset threshold. The amount of power
reduction is determined by the severity of the over dissipation.
As the power is stepped down, the heat sink temperature will
decrease until it is under the threshold of the sensing circuit, at
which time the LOWER command will stop. The POWER must
be increased to the original level by an operator induced RAISE
command. A “Temperature Caution” or “Over Temperature”
condition will illuminate LED’s on the Driver Encoder/Temp
Sense Board. A DC temperature sample voltage from the RF1
sensor is available at TB1-10 for remote temperature monitor-
ing.
4.6
Interlocks
The interlock circuits protect personnel and external equipment
from dangerous or unsafe conditions. For a description of inter-
lock circuits and logic, refer to SECTION P, Controller. The
interlock circuitry is detailed on the DC Regulator schematic,
839-7855-163, and the DX-25U Overall Schematic, 839-7855-
151, in the Drawing Package.
4.6.1
Door Interlock Circuit
The door interlock circuit turns the transmitter OFF if any of the
three interlocked RF Amp Compartment doors are opened. The
DOOR interlock LED on the ColorStat™ panel will illuminate RED.
4.6.2
External Interlock Circuit
The external interlock circuit turns the transmitter OFF if any
external interlock interrupts the normally closed connection
between TB1-1 and TB1-2. The EXTERNAL interlock LED on
the ColorStat™ panel will illuminate RED.
The EXTERNAL interlock circuit includes relay K3, 1 Amp
fuse F24, pull up/pull down resistors on the DC Regulator and
interlock logic on the Controller. External Interlock connections
are detailed in SECTION II, Installation/Initial Turn-On.
4.7
RF Circuits
Refer to Sheet three of the DX-25U Overall Schematic, 839-
7855-151, for the following circuit information.
Most of the RF drive circuits are detailed in their own sections.
The Block Diagram Description has already explained how each
section contributes to the drive system in the DX-25U, therefore
no further information is necessary in this section.
Refer to the following sections for more information:
Oscillator
Buffer
Predriver
Driver
Driver Combiner
Driver Supply Regulator
Driver Encoder/Temp Sense
Section S
RF Multimeter
4.7.1
RF Drive Splitter, A15
The combined RF output from the Driver stage feeds the RF
Drive Splitter. The splitter has provision for 256 outputs, two
for each of the 128 PA Modules in a DX-50, however, only 128
are utilyzed in the DX-25U. An additional connector (J17) on
the splitter assembly provides three RF sample signals to other
parts of the transmitter, as follows:
a. To the Driver Supply Regulator and Driver Encoder/Temp
Sense Board: An RF sample for the RF drive Automatic
Gain Control (AGC) loop.
b. To the Analog to Digital Converter: A synchronizing
signal for the analog to digital conversion process.
c. To the LED Board: An RF drive sample, for Overdrive and
Underdrive Fault sensor circuits and for “Relative RF
Drive” Metering.
4.7.2
RF Drive Cables
The RF drive splitter outputs, at connectors J1 through J16, are
very low impedance, and the 128 separate RF drive cables to the
PA Module inputs provide additional isolation so that a fault at
one module input will have little or no effect on other RF drive
signals.
The 16 connectors from the splitter provide connections for two
sets of eight coaxial cables. Each group of eight cables from each
connector form a cable bundle which goes to an input connector
DX-25U
4-6
888-2297-002
Rev. AA: 8-9-00
WARNING: Disconnect primary power prior to servicing.