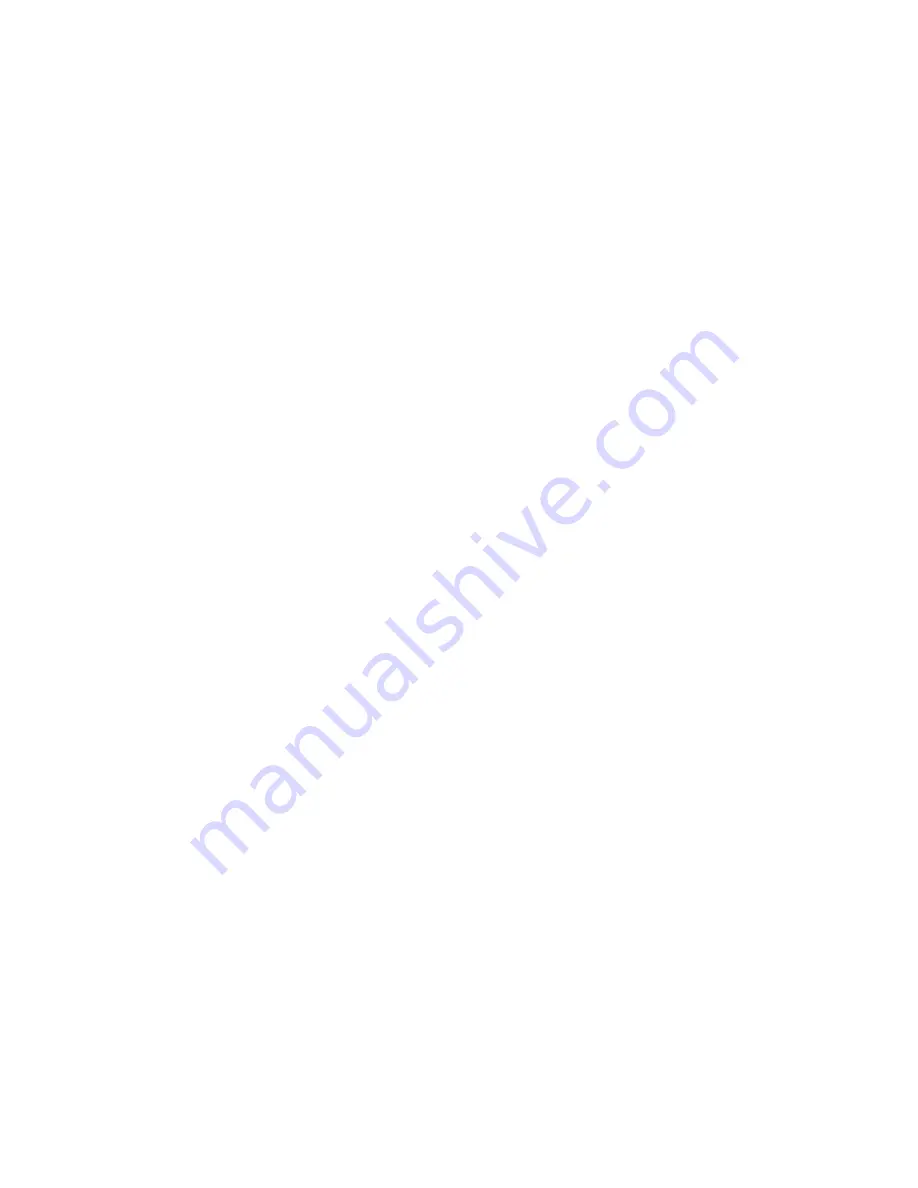
tor output is inhibited from registering a fault. After approxi-
mately 0.3 seconds, the Underdrive “Inhibit” is released. If RF
drive is correct, the RF drive sample voltage will be greater than
the reference voltage by this time. If RF drive is low, an Under-
drive Fault will cycle the transmitter OFF, the “Underdrive”
LED on the ColorStat™ panel will turn AMBER, and the
transmitter will recycle back ON. If RF drive is still low on the
second try, the transmitter will turn OFF and the “Underdrive”
LED will turn RED.
Q.5.3.4.4
“Underdrive Inhibit A” and “Underdrive Inhibit B”
Logic Signals
When the transmitter is turned “ON”, the step-start circuit
applies AC to the PA Power Supply and supply voltage begins
coming up. If there are no faults, step-start contactor K1 auxil-
iary contact provides a “K1 has closed” LOW-to-HIGH transi-
tion on the “Underdrive Inhibit B” signal line. After a 0.3 second
delay, the “Underdrive Inhibit A” line also goes HIGH.
Q.5.3.4.5
Underdrive Reference Voltage Ramp
Capacitor C50 charges through resistor R72 to provide a refer-
ence voltage “ramp” for the underdrive threshold comparator.
The “Underdrive Inhibit B” LOW-to-HIGH transition resets the
ramp as follows: The “Underdrive Inhibit B” LOW-to-HIGH
transition is differentiated by capacitor C151 and resistor R177
to provide a current pulse which turns Q1 ON and discharges
ramp capacitor C50.
Q.5.3.4.6
“Underdrive Inhibit A” and Inhibit Gate U9-8
During first part of the step-start cycle, the “Underdrive Inhibit
A” line is LOW. This logic LOW signal at U9-9 holds the output
LOW, even if the comparator output goes HIGH. Approximately
0.3 seconds after step-start contactor K1 closes, “Underdrive
Inhibit A” goes HIGH so that if RF drive is low a Type 2 Fault
is generated.
Q.5.3.4.7
“RF Drive Relative/Estimate”: U57-8
The RF Drive Relative/Estimate provides a RELATIVE (UN-
CALIBRATED) indication of RF drive level.
The “RF Drive Estimate” analog voltage goes to the Switch
Board/Meter Panel, for the “Relative RF Drive” reading on the
front panel multimeter. An “RF Drive Estimate” analog voltage
is also available at TB1-7 for a remote “RF drive estimate”
output.
The RF Drive Estimate uses a DC voltage from the “RF Under-
drive” sample circuit, and provides an uncalibrated indication
of RF level at the RF splitter. Buffer U57-8 provides two analog
output signals. Refer to sheet 4 of the LED Board schematic
diagram; U57-8 is shown at location D5.
Q.5.3.5
Supply Current Overload
Supply Current Overload circuits are shown on Sheet 3 of the
LED Board schematic diagram at grid location E7. Either a
PEAK CURRENT OVERLOAD or an AVERAGE CURRENT
OVERLOAD will cause a Supply Current Overload.
The voltage drop across current shunt SH1 is amplified by
U57-7. The current shunt is between the negative side of the PA
Power Supply and ground and is also the shunt for the 100
Ampere “supply current” meter. Voltages at the differential
amplifier input are small; 50 millivolts across the shunt corre-
sponds to 100 Amperes of supply current.
Q.5.3.5.1
Peak Current Overload
Comparator U2-14 senses peak current overloads. The compa-
rator voltage reference is set by “Peak Current Threshold”
control R68. Normally the comparator output is LOW but if
peak supply current exceeds the preset threshold, the compara-
tor output goes HIGH.
Q.5.3.5.2
Average Current Overload, And Remote Supply Current
Metering Output
Resistor R155 and capacitor C125 form a low-pass filter to
remove audio frequency components from the supply current
sample, so that only the average supply current remains at the
input of voltage follower U57-1. The voltage follower provides
an Average Supply Current output to the External Interface, for
remote “Supply Current” metering.
The voltage follower also goes to the noninverting input of
comparator U2-13. The inverting input is a reference voltage set
by R42, the Average Current Threshold control. If average
current exceeds the preset threshold, the comparator output goes
HIGH.
Average current limiting is accomplished by feeding the com-
parator output to the Analog Input Board at J9-37. The output
pulses of comparator U2-13 are integrated and produce a feed-
back signal that reduces the power output if PA current increases
to an unsafe level.
The Peak and Average overload detector outputs are fed to “OR”
gate U19-6. If either a peak current overload or an average
current overload is detected, the output of OR gate U19-6 goes
HIGH, triggering one-shot U11 in the Type 2 Fault Logic.
Q.5.3.6
Type 2 Fault Logic: Circuit Description
Figure Q-4(a) is a simplified diagram of Type 2 Fault Logic,
which is the same for RF Overdrive, RF Underdrive, and Supply
Current Overload faults. Type 2 Fault logic includes two one-
shots, an AND gate for repeated faults, and a fault latch circuit.
Type 2 Fault logic for each of the three Type 2 Faults include the
following IC sections:
a. RF Overdrive: One-Shots U10A (1 sec) and U30A (2.4
sec), AND gate U16-8, gate U31-6, and fault latch U52A.
b. RF Underdrive: One-Shots U10B (1 sec) and U30B (2.4
sec), AND gate U16-3, gate U31-3, and fault latch circuit
U51B.
c. Supply Current Overload: One-Shots U11A (1 sec) and
U11B (2.4 sec), AND gate U16-11, gate U31-8, and fault
latch circuit U52B.
Q.5.3.6.1
First One-Shot (1 second)
When a Fault is detected, a LOW-to-HIGH transition at the first
One-Shot input triggers the one-shot. A one-second logic HIGH
pulse is generated at the Q output and a one-second logic LOW
pulse is generated at the NOT-Q output.
The logic HIGH pulses from all three one-shot “Q” outputs
provide a “Type 2 Fault-H” input to the turn-on/turn-off logic
Section Q - LED Board (A32)
Rev. R: 11-11-96
888-2297-002
Q-11
WARNING: Disconnect primary power prior to servicing.