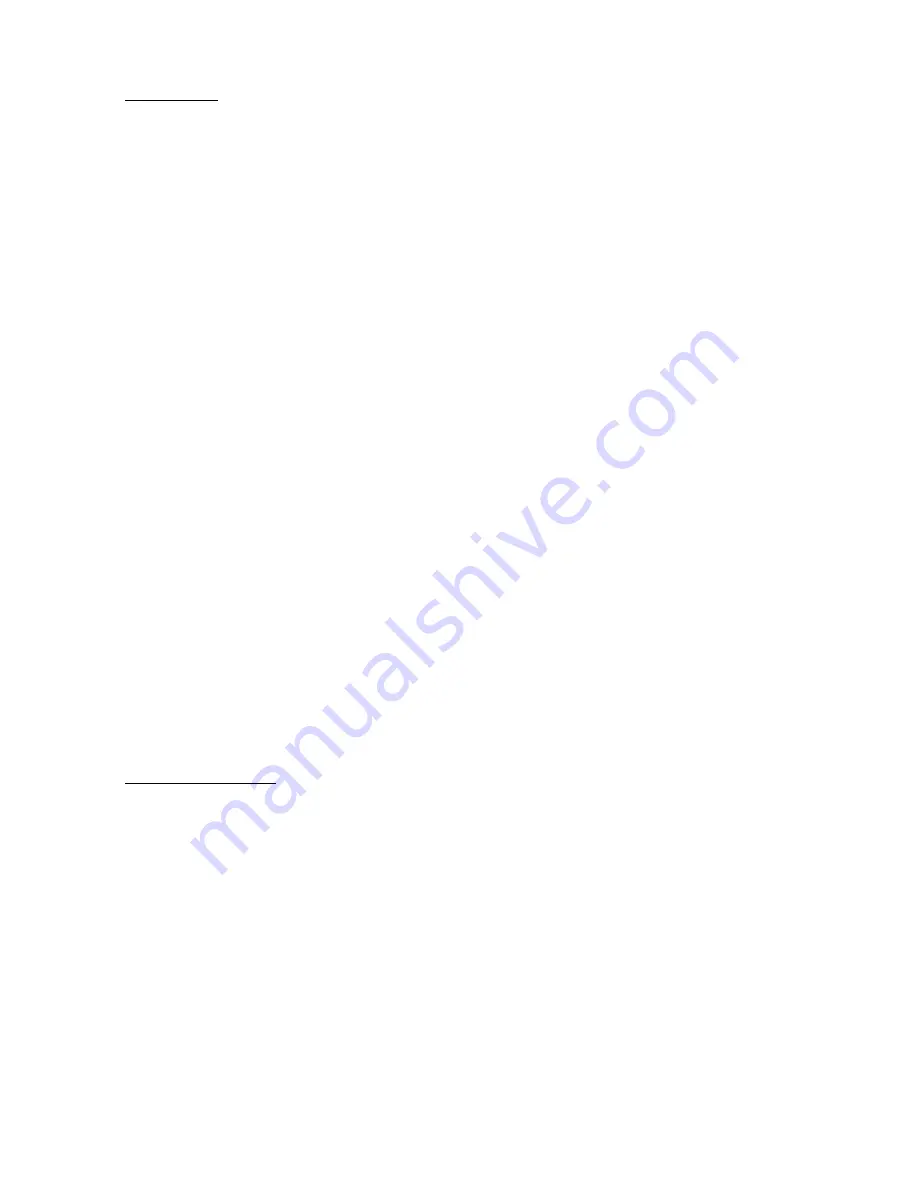
Q.5.1
Reset Circuit
The reset circuit is on sheet 1 of the LED Board schematic
diagram, 839-7855-184, in the Drawing Package. The circuit
includes gates U63, U64, and U65, and two U66 inverting
Schmitt triggers.
Q.5.1.1
External Reset/+5B Reset
Either an “EXT RESET” or a “+5B RESET” logic LOW input
will cause U64-11 to go LOW. The EXT RESET input is from
an opto-isolator on the External Interface. This will pull the
input of the buffer and one input to U64 LOW when a remote
“Reset” command is given. The “+5B RESET” is a logic LOW
signal from the +5B Reset circuit on the Controller.
When U64-11 goes LOW, U64-3 is forced LOW, and U63-11 is
forced HIGH. This is the “RESET-H” logic signal when either
an “EXT” reset or a “+5B Reset” occur.
Q.5.1.2
“Reset” Switch
The RESET switch is on the ColorStat™ panel. Depressing the
RESET switch also generates a RESET-H logic signal at U63-
11.
Q.5.1.3
Switch De-bounce
A switch de-bounce function is performed by U63 pins 8 and
11 for the RESET inputs.
Q.5.1.4
Inhibit Gate
Inhibit gate U63-6 blocks any “Resets” during the transmitter’s
step-start cycle. When the turn-on/turn-off logic on the Control-
ler provides a “K1 Drive” pulse for step-start contactor K1, the
logic LOW “K1 NOT-pulse” holds U63-6 HIGH.
Q.5.1.5
Reset A
U63-6 is the “Reset A-L” signal which clears the status indicator
latches.
Q.5.1.6
Reset B
The “Reset A-L” signal is delayed approximately 60 nanosec-
onds plus the gate propagation delay through U65-6. The de-
layed “Reset B” retriggers the fault indicator latch if a fault is
still present after a “Reset”.
Q.5.2
Type 1 Fault Circuits
Type 1 Faults turn the transmitter OFF, by providing a Type 1
Fault logic HIGH signal to the turn-on/turn-off logic on Con-
troller. The following paragraphs will first describe Type 1 Fault
logic, from fault detection circuit outputs, and then will describe
fault detection circuits for each Type 1 fault.
Type 1 Fault circuits described in this section include:
a. Air Flow Fault.
b. PA Power Supply Fault
c. PA Power Supply Overvoltage.
d. Cable Interlock Fault
e. Output Monitor, +5 Volt Supply Fault.
f. Output Monitor, -5 Volt Supply Fault.
g. DC Regulator, B+ Supply Fault.
h. DC Regulator, B- Supply Fault.
Additional Type 1 Fault circuits described in other parts of this
Technical Manual include:
a. Door Interlock logic: Refer to SECTION P, Controller.
b. External Interlock logic: Refer to SECTION P, Controller.
c. Repeated Type 2 Faults become Type 1 Faults, and are
described later in this section, as “Type 2 Faults.”
Q.5.2.1
Type 1 Fault Logic
Type 1 Fault logic on the LED Board is shown on sheet 1 of the
LED Board schematic, 839-7855-184, at grid locations C1 through
C3.
Type 1 Fault logic includes OR gate U32, OR gate U19-8, “pulse
stretcher” U42-9, and OR gate U50-3. The “Type 1 Fault-H”
output from U50-3 goes to the Controller.
Eight-input OR gate U32 has inputs from eight fault detection
circuits. If any Type 1 fault occurs, a logic HIGH signal at an
input causes U32 output to go HIGH. The “Type 1 Fault” output
goes to pin 9 of two-input OR gate U19. The second input is a
logic HIGH signal if a “repeated Type 2 Fault” occurs.
Pulse stretcher U42-9 and OR gate U50-3 ensure that any Type 1
Fault will generate at least a 2.4 second transmitter turn-off pulse.
Q.5.2.1.1
Pulse Stretcher U42-9
During normal transmitter operation, the Q output of U42-9 is
LOW, and the NOT-Q output is HIGH so that capacitor C103 is
charged and holds the CLEAR input HIGH. The “D” and “PR”
inputs are always held HIGH, so that a LOW-to-HIGH transition
at the Clock input will trigger the latch. When a Type 1 Fault is
detected, the LOW-to-HIGH transition at the U42-11 CLOCK
input triggers the latch. The Q output goes HIGH and the NOT-Q
output goes LOW. Capacitor C103 discharges through resistor
R125. When the voltage across C103 goes low enough, U42
“CLEARS.” When U42 clears, the Q output goes LOW again
and the NOT-Q output goes HIGH. The output of U50-3 will be
HIGH if the Q output is HIGH, if a “Type 1 Fault-H” is present,
or if both inputs are HIGH. The LED Board “Type 1 Fault”
output will be high for 2.4 seconds, or as long as the Type 1 Fault
is present, whichever condition lasts longest.
Q.5.2.2
Air Flow Fault Sensing
The Air Flow Fault circuit includes an air flow sensing unit, U62
on the Driver Encoder/Temp Sense Board, and logic on the LED
Board. A “Reduced air flow” fault occurs if one fan fails or if the
air flow is reduced to the level caused by the failure of one of the
four fans. The AIR LED on the ColorStat™ panel will turn
AMBER and the transmitter will continue to operate normally.
An “Air Flow Fault” occurs if two fans fail or there is insufficient
air flow to properly cool the RF Amplifier modules. The AIR
LED on the ColorStat™ panel will turn RED and the transmitter
will turn OFF. Causes of insufficient air flow include fan failure,
incorrect blower motor phase, missing or loose panels on the
back of the transmitter.
Q.5.2.3
“Air Flow Fault” Logic
Air Flow Logic includes:
a. INHIBIT gate U20-6. The Inhibit Gate output is the “Air Flow
Fault,” logic HIGH signal to Type 1 Fault OR gate U32.
Section Q - LED Board (A32)
Rev. R: 11-11-96
888-2297-002
Q-7
WARNING: Disconnect primary power prior to servicing.