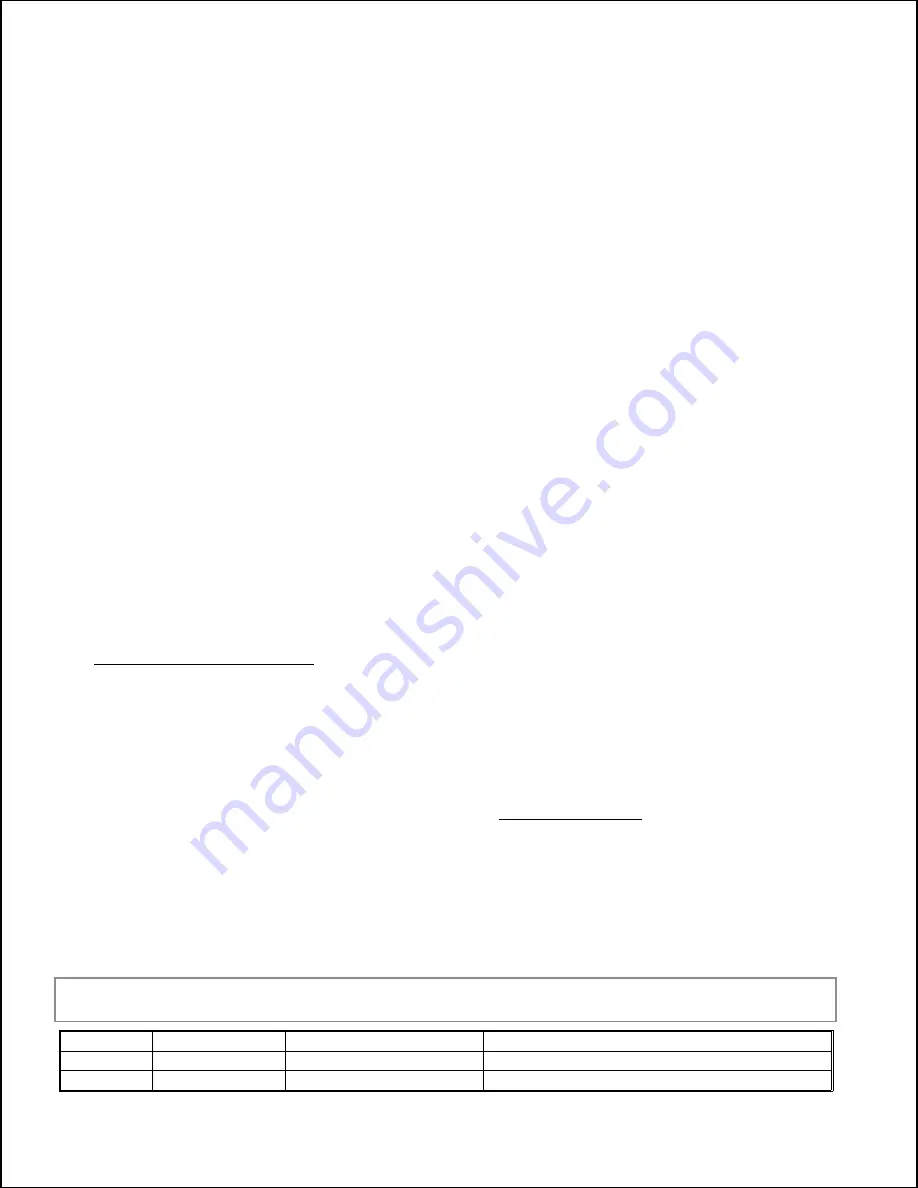
d. To set the output frequency of crystal Y2, turn off the low
voltage and move jumpers J1 and J6 to positions 1-3.
Repeat the above procedure by adjusting C3.
5.6.3.2
Oscillator Sync Adjustment: S1/L4
The Oscillator Sync adjustment is critical to the proper operation
of the VSWR circuitry. If the circuit is not adjusted properly,
damage to the RF amplifiers could result during a VSWR condi-
tion.
a. Using a dual trace scope connect channel one to TP5 and
channel two to TP4 on the Oscillator. Sync the scope to
channel one.
b. Operate the transmitter at full power and note a 5.0 Vp-p
square wave at the carrier frequency on channel one.
Channel two will also have a 5.0 Vp-p square wave dis-
played.
c. Adjust the scope to display one or two cycles of RF. If the
positive going edges of the two waveforms are lined up,
no further adjustments are required. Refer to Figures 5-9
and 5-10, Oscillator Sync waveforms.
d. If the two waveforms are not in phase and adjusting L4
does not line up the positive going edges, then different
combinations of capacitance can be switched in by S1.
e. When switching in different values of capacitance use the
least amount necessary to achieve phase alignment of the
two signals. If too much capacitance is used there may not
be enough signal input at TP4.
f. Operate the transmitter at 5.0 kW and make sure there is
still a signal present at TP4. The two signals may not be as
well aligned as at full power.
5.6.4
Driver Supply Regulator (A22)
The Driver Supply Regulator sets the proper voltage to Driver
8A and 8B. Two controls and one switch must be set properly for
correct transmitter operation. If the Regulator is not operational,
note DRIVER 8A voltage on the Factory Test Data sheet and the
normal transmitter log reading.
5.6.4.1
Removing The Driver Supply Regulator Assembly
a. Turn off the primary AC power at the main disconnect.
b. Remove the clear plastic safety cover over the Driver
Supply Regulator.
c. Disconnect all cables from the assembly. Remove the bolts
holding the assembly to the transmitter wall.
5.6.4.1.1
Removing Printed Circuit Board From The Heat Sink
The printed circuit board is mounted on the heat sink, using six
screws and spacers. The seven MOSFET’s are soldered to the
printed circuit board, and are mounted on the heat sink using
screws, compression washers, and insulator pads.
To remove the printed circuit board, the seal between the transis-
tors and the insulator pads will have to be broken. Use a long
knife or ice pick to slide underneath the pc board to pry the
MOSFET off the pad. The pad may tear or peel when the seal is
broken. Always replace damaged pads.
5.6.4.2
Preset Adjustments
To prevent drive overloads, it is recommended that the two
adjustments be preset by measuring the resistance of the controls
on the board to be replaced. The most convenient measurement
locations are shown in Table 5-3.
NOTE
Before proceeding with any adjustments, determine that the AC
line voltage is at normal voltage levels. If the voltage is either
higher or lower than normal, recheck your adjustments when the
AC line has returned to normal.
5.6.4.2.1
Open Loop Adjust: R2
a. Set S1 on the Driver Supply Regulator to the OPEN LOOP
position.
b. On the Controller, switch PA TURN-OFF switch S2 to the
OFF (up) position.
c. Turn on Low Voltage at CB1 and CB2 and depress the
LOW power button. The +230 VDC supply should be
energized but there should be no RF output.
d. Note DRIVER D8A voltage. If the voltage is close to the
normal voltage or to the recorded voltage on the Factory
Test Data sheet, then no further adjustment of the Open
Loop control is necessary.
e. If adjustment is necessary, use an insulated tuning tool to
adjust R2 for normal operating voltage on D8A.
5.6.4.2.2
Closed Loop Adjust: R12
a. Switch S1 to the CLOSED LOOP position.
b. Adjust R12 (Closed Loop Adjust) so that DRIVER D8A
voltage is the same as the Open Loop voltage.
c. Return the PA TURN-OFF switch to the PA-ON position
and readjust R12 for the correct reading at normal power
output.
5.6.5
DC Regulator (A30)
The DC Regulator has two adjustments which should be preset
before the transmitter PA Power supply is turned on. Refer to the
Factory Test data sheet for the LCD Multimeter readings on the
DC Regulator.
a. Place P1 in the TEST position.
b. Turn on the Low Voltage supply with CB1 and CB2 and
monitor TP8 with an external meter. Adjust for +2 VDC
with R1.
CONTROL
FUNCTION
MEASUREMENT POINTS
MEASURED RESISTANCE
A22R2
OPEN LOOP ADJ
U2-2 to ground
A22R12
CLOSED LOOP
R14(Left side) to R13(Left)
Table 5-3. Driver Supply Measurements
DX-25U
5-8
888-2297-002
Rev. Z1: 06-02-00 Additional info to ECN 46105
WARNING: Disconnect primary power prior to servicing.