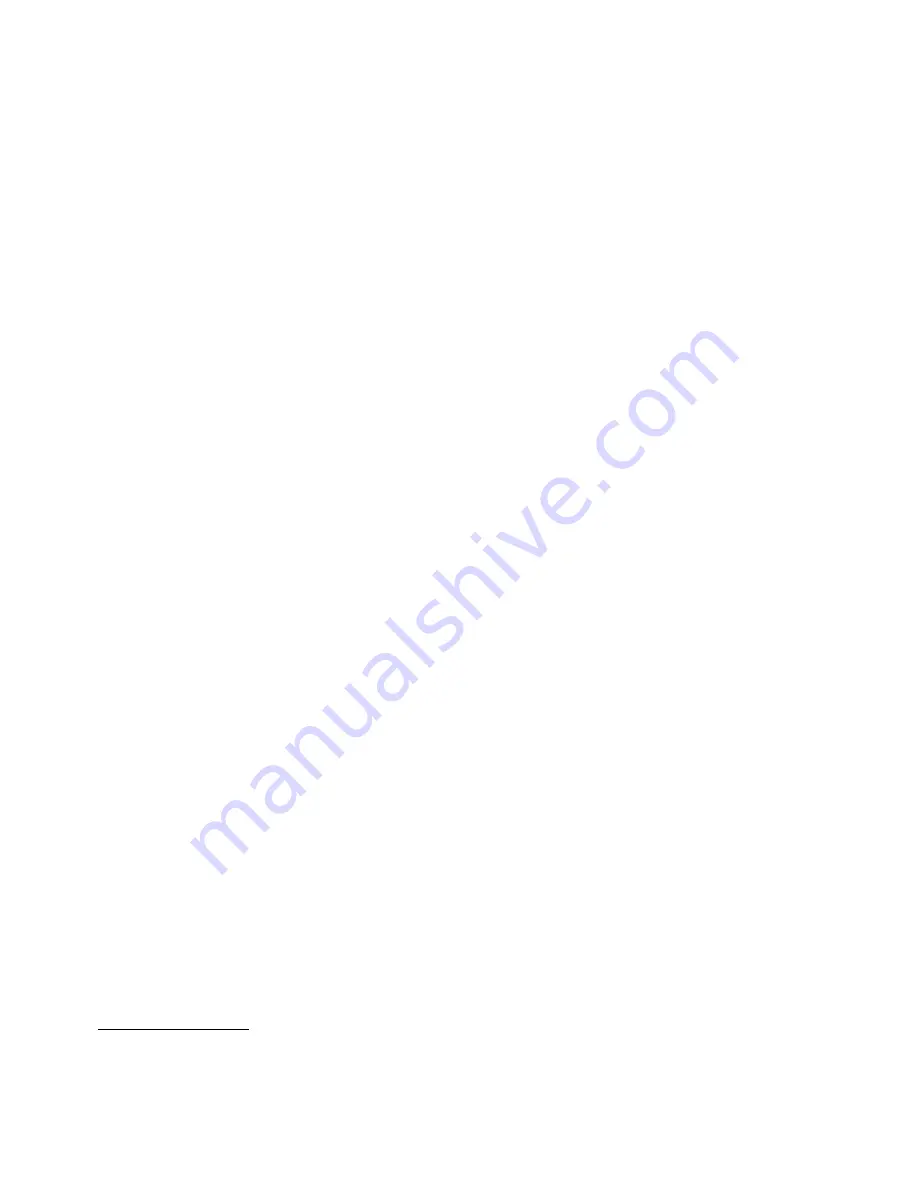
Q.5.2.7.1
Regulator Fault Alert Outputs
For a description of regulator IC operation and faults which
cause a “fault alert” refer to SECTION M, “DC Regulator.”
When there is no fault, the “Fault Alert” output is an open circuit.
When a voltage regulator senses a supply “fault,” the internal
“Fault Alert” transistor conducts, effectively connecting the
Fault Alert output to the regulator internal ground. For POSI-
TIVE supplies, this is the transmitter ground. For NEGATIVE
supplies, the internal regulator “ground” goes to the unregulated
negative input voltage through a small resistance.
Q.5.2.7.2
Output M5 VDC Fault
The “Fault Alert” input from the +5 VDC regulator on the
Output Monitor is applied to J3-21. If a +5 VDC fault is detected,
the input line will go LOW to trigger U61-2.
Q.5.2.7.3
Output Monitor -5 VDC Fault
The “ Fault Alert” input from the -5 VDC regulator on the Output
Monitor is applied to J3-19. If a -5 VDC fault is detected, the
input line will go LOW to trigger U61-1.
Q.5.2.7.4
DC Regulator B+ Fault Input
This input is driven by a TTL level logic driver which is part of
the Supply Fault circuit on the DC Regulator (refer to SECTION
M, DC Regulator, for more information). A B+ supply fault
causes the logic driver output to go LOW, and comparator
U61-13 generates a Type 1 Fault.
Q.5.2.7.5
DC Regulator Modulated B- Supply Fault
This negative supply input has a pull-up resistor on the DC
Regulator. The “no fault” input to the LED Board is positive and
the “sense” input circuit uses a voltage divider to ground on the
LED Board. A Modulated B- supply “Fault Alert” causes the
LED Board “fault” input to go negative, and Schottky diode
CR17 protects the comparator input by clamping it to ground.
Q.5.2.8
“Door Interlock” And “External Interlock” Status
Indication Circuits
These Status Indication circuits are shown in the upper right
section of Sheet 6 of the LED Board schematic diagram. Both
circuits are the same. Interlock Fault circuits are on the Control-
ler, and are described in SECTION P, Controller.
When no interlock faults are present, the “Interlock Status”
input to the LED Board is logic HIGH. Buffer/Driver U55-10/12
output goes HIGH and illuminates the GREEN section of the
bicolor status LED. U46 invertor output pins 2,4, 6, and 8 go
LOW, the RED section of the LED is off, and a logic LOW signal
goes to the External Interface.
When an interlock FAULT is present, the “Interlock Status”
input is logic LOW. The Buffer/Driver output goes LOW and
the GREEN LED section is OFF. Both invertor outputs go
HIGH, illuminating the RED LED section and sending a “Fault-
H” signal to the External Interface.
Q.5.3
Type 2 Fault Circuits
Type 2 Faults include RF Overdrive, RF Underdrive, and Supply
Current Overloads.
Type 2 Faults are usually temporary or transient conditions, such
as current overloads caused by overmodulation. Turning the PA
Power Supply OFF may correct the condition, so Type 2 Faults
cycle the transmitter OFF, then back ON.
Q.5.3.1
Type 2 Fault Action
A Type 2 fault executes the following steps:
a. Turns the PA Power Supply OFF.
b. After 1 second, turns the PA Power Supply ON again and
starts another timer (a second time-out).
c. For 2.4 seconds after starting the turn-on sequence,
watches for a repeated fault condition.
1. IF THE FAULT CONDITION REPEATS WITHIN
THE 2.4 SECOND TIME-OUT: Initiate a Type 1 Fault
which turns the transmitter OFF.
2. IF THE FAULT DOES NOT REPEAT WITHIN THE
2.4 SECOND TIME-OUT: All status indications and
transmitter operation return to normal.
Q.5.3.2
Type 2 Fault Status Indications
When a Type 2 Fault occurs, the ColorStat™ panel “Overload
Indicator” will latch in a RED condition until it is manually
reset.
Q.5.3.3
Type 2 Fault Detection: Circuit Description
Type 2 Fault Detection circuits are shown on Sheet 3 and 4 of
the LED Board schematic diagram. The following paragraphs
describe RF OVERDRIVE, RF UNDERDRIVE, and SUPPLY
CURRENT OVERLOAD fault sensing circuits. Following the
descriptions, “Type 2 Fault” logic and status indication circuits
are described.
Q.5.3.4
RF Drive Detection Circuits
An RF Drive sample from the RF Splitter is applied to the
primary of transformer T1. A resistor-inductor network across
the primary provides loading and broad-banding, and capacitors
across the two secondaries also provide loading. The two sec-
ondary windings, CR5 and CR6 and an R-C filter each provide
a DC sample for the associated fault detector comparator.
Q.5.3.4.1
RF Overdrive Fault Detector: U2B
The DC RF drive sample is applied to the non-inverting input
of U2-2. A reference voltage at U2-4 is set with Overdrive
Threshold control R41. Under normal operation, the reference
voltage is greater than the “rf drive sample” and the comparator
output is LOW. If the “RF drive sample” voltage is greater than
the reference voltage, the output is pulled HIGH by R44.
Q.5.3.4.2
RF Underdrive Fault Detector: U2-1
The DC RF drive sample is applied to the inverting input, U2-6.
The reference voltage is adjusted by R67 and is applied to the
non-inverting input, U2-7. During normal operation, the RF
drive sample voltage is greater than the reference voltage and
the comparator output is LOW. If the RF drive sample voltage
drops below the reference voltage, U2-1 is pulled HIGH by R56.
This provides a logic “Fault-HIGH” input to U10-2 through
Inhibit Gate U9-11.
Q.5.3.4.3
Comparator Voltage Ramp, “Underdrive Inhibit A,” and
“Underdrive Inhibit B”
When the transmitter is first turned ON, the Underdrive Thresh-
old reference voltage is zero, and begins increasing as capacitor
C50 charges. RF drive also begins increasing, but the compara-
DX-25U
Q-10
888-2297-002
Rev. R: 11-11-96
WARNING: Disconnect primary power prior to servicing.