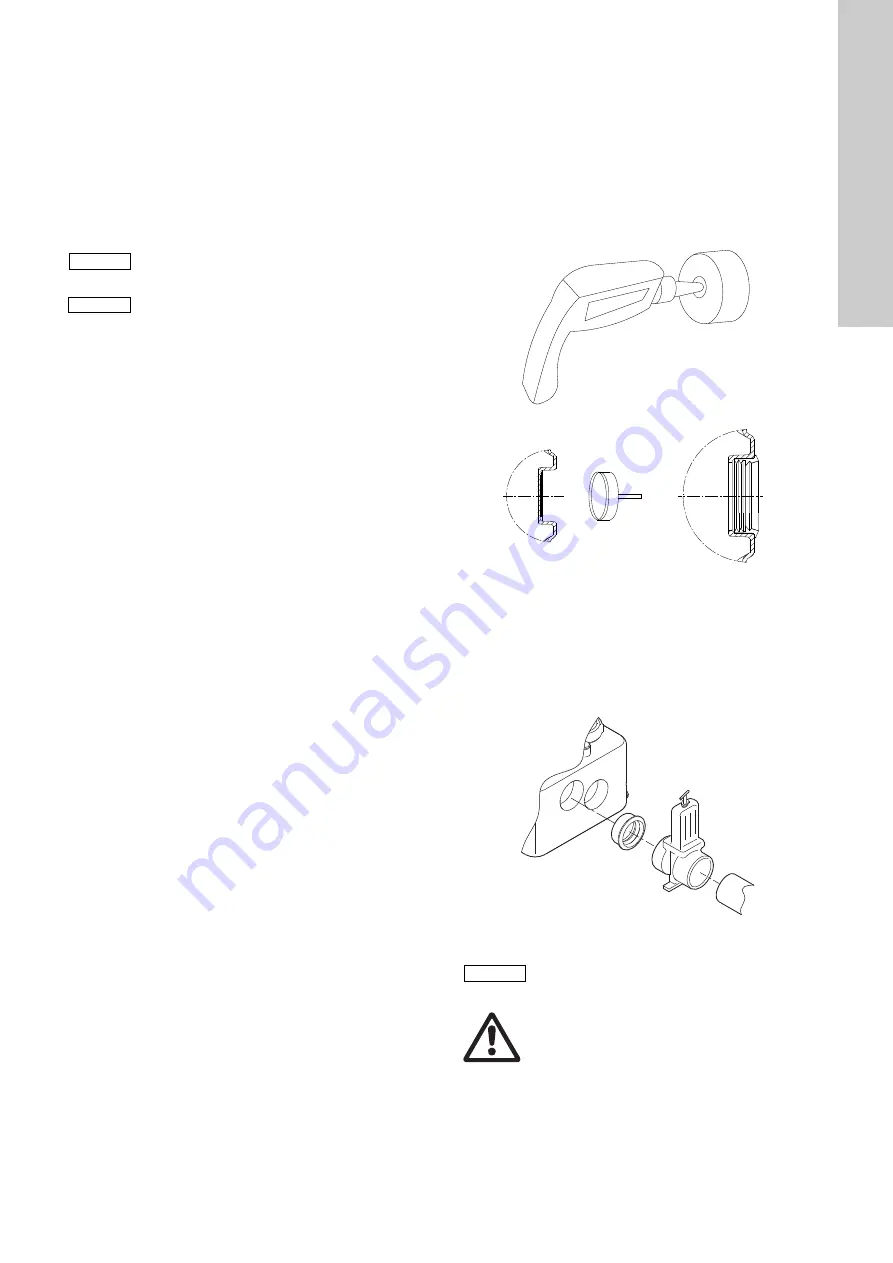
English (GB)
13
6.2 Guidelines for installation of lifting station
Guidelines for correct mechanical installation of lifting
station according to EN 12056-4
See section
.
• Install the lifting station in a properly lit and vented room with
60 cm free space around all parts to be serviced and operated.
• Provide a pump sump below the floor level. If a lifting station is
installed in a basement with the risk of penetrating
groundwater, it is advisable (in certain countries required) to
install a drainage pump in a separate pump sump below floor
level in order to drain the room. See fig.
.
• All pipe connections must be flexible to reduce resonance.
• Lifting stations must be secured against uplift and twist.
• All outlet pipes (lifting station, diaphragm pump and drainage
pump) must have a loop above the local backwater level. The
highest point of the goose neck/reversed water seal must be
above street level.
• For outlet pipes, DN 80 and upwards, install an isolating valve
in the outlet pipe. Also provide an isolating valve in the inlet
line.
• Surface water must not be discharged into the lifting station
inside the building. It must have its own pumping station
outside the building.
• Lifting stations must be provided with an approved non-return
valve according to EN 12050-4.
• The volume of the outlet pipe above the non-return-valve up to
the backwater level must be smaller than the effective tank
volume.
• In general, a lifting station for black wastewater must be
vented above roof level. However, it is permitted to lead the
ventilation, as a secondary ventilation, into the main building
ventilation system.
• If the wastewater is discharged into a collecting line, this
collecting line must have a filling ratio of at least h/d = 0.7.
The collecting line must be at least one nominal diameter
bigger after the outlet pipe connection.
• Use a diaphragm pump for simple, manual draining of the
collecting tank in case of pump failure (not obligatory).
6.3 Recommended steps for mechanical installation of
lifting station
1. Checking the scope of delivery. For scope of delivery, see
section
2. Preparing the inlets by cutting out the required holes. Use cup
drills
∅
100 for DN 100 and
∅
43 for DN 50 inlets. The cutting
line is recessed. To avoid sharp cutting edges, the holes must
be deburred. The socket seals are provided with collars.
3. Preparing the connection for diaphragm pump (optional). Use
cup drill,
∅
43, for DN 50 connection socket. To avoid sharp
cutting edges, the hole must be deburred.
Fig. 11
Cutting or drilling of connection holes
4. Connecting the inlet pipe to the tank. Install an isolating valve
between inlet pipe and lifting station to avoid inflow during
maintenance and service. We recommend an easy-to-handle
PVC isolating valve.
Fig. 12
Installation of isolating valve
Note
The collecting tank, pump and cables may be flooded
(max. 2 m for 7 days).
Caution
The controller must be installed in a dry and well
ventilated place.
TM0
5
124
2
2
5
11
TM
0
3
3
614
0
406
Caution
Make sure that weight from inlet, outlet and vent
pipes does not rest on the tank. Long pipe sections,
valves, etc. must be supported.
Warning
Never step on the lifting station.
DN 50 -
∅
43
DN 100 -
∅
100
DN 150 -
∅
150
Summary of Contents for Multilift MSS
Page 2: ...2...
Page 4: ...Table of contents 4 Multilift MSS UA 366 CN 381 Appendix 396...
Page 25: ...BG 25 5 2 2 8 ON OFF AUTO I O AUTO 8 1000 mm DIP EN 12056 4 TM05 3455 0616...
Page 145: ...GR 145 5 2 2 8 ON OFF AUTO AUTO LED 8 1000 mm DIP H EN 12056 4 TM05 3455 0616...
Page 371: ...UA 371 5 2 2 8 ON OFF AUTO I O AUTO 8 1000 DIP EN 12056 4 TM05 3455 0616...
Page 386: ...CN 386 5 2 1 LC 220 4 5 2 2 8 ON OFF AUTO I O AUTO LED 8 1000 mm DIP EN 12056 4 TM05 3455 0616...
Page 397: ...397...
Page 398: ...398...