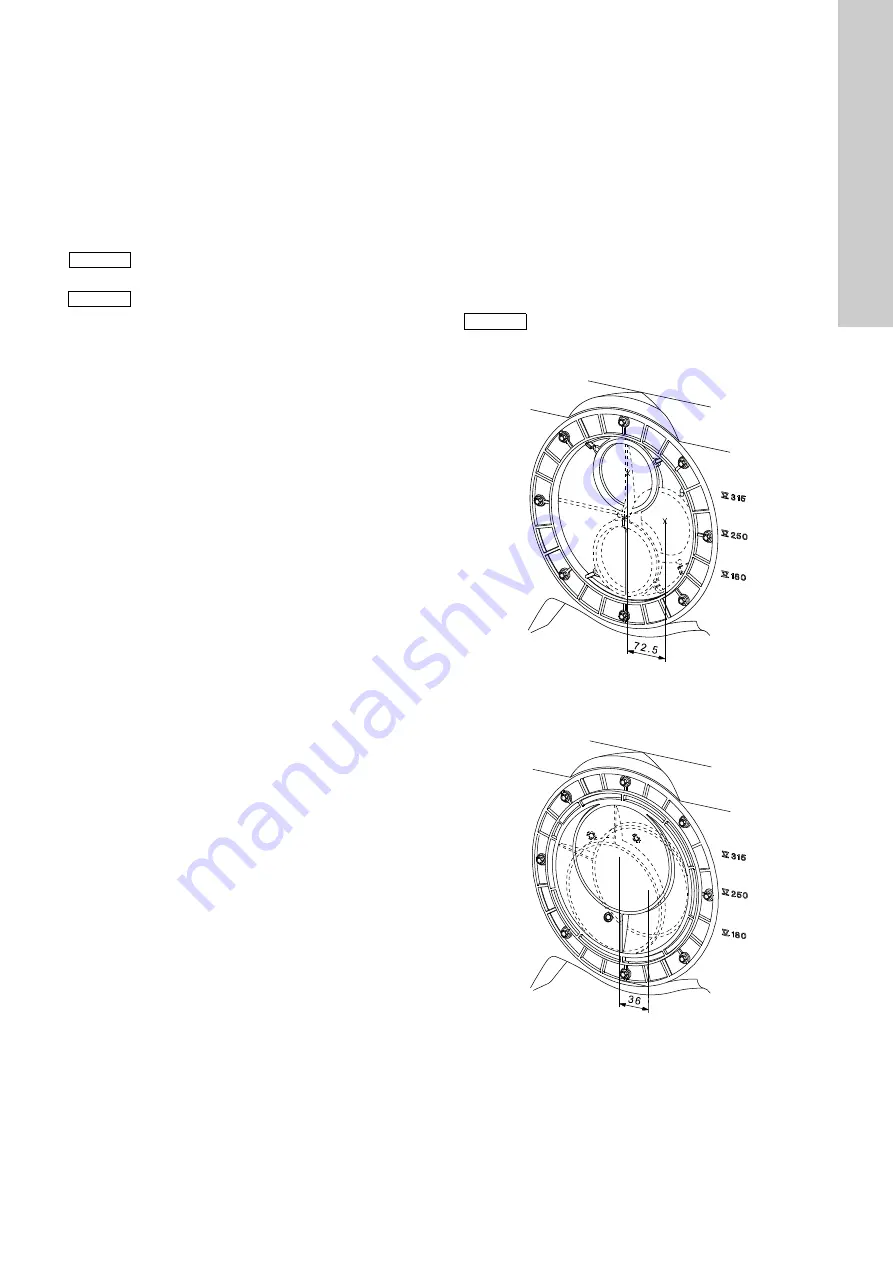
English (GB)
25
7.2 Guidelines for installation of lifting station
The guidelines for correct mechanical installation of lifting station
are according to EN 12056-4.
See section
.
• Install the lifting station in a properly lit and vented room with
60 cm free space around all parts to be serviced and operated.
• Provide a pump sump below the floor level. If a lifting station is
installed in a basement with the risk of penetrating
groundwater, it is advisable (in certain countries required) to
install a drainage pump in a separate pump sump below floor
level in order to drain the room. See fig. 15.
• All pipe connections must be flexible to reduce resonance.
• Lifting stations must be secured against uplift and twist.
• All discharge pipes from lifting station, diaphragm pump and
drainage pump must have a bend above the local backwater
level. The highest point of the bend/reversed water seal must
be above street level. See fig. 15.
• For discharge pipes, DN 80 and upwards, install an isolating
valve in the discharge pipe. Also provide an isolating valve in
the inlet line.
• Surface water must not be discharged into the lifting station
inside the building. It should have its own pumping station
outside the building.
• Lifting stations must be provided with an approved non-return
valve according to EN 12050-4.
• The volume of the discharge pipe above the non-return-valve
up to the backwater level must be smaller than the effective
tank volume.
• In general, a lifting station for black wastewater must be
vented above roof level. However, it is permitted to lead the
ventilation, as a secondary ventilation, into the main building
ventilation system. Special venting valves (accessory) should
be placed outside the building.
• If the wastewater is discharged into a collecting line, this
collecting line must have a filling ratio of at least h/d = 0.7.
The collecting line must be at least one nominal diameter
bigger after the discharge pipe connection.
• The controller must be placed in a flood safe place and be
equipped with an alarm.
• Use a diaphragm pump for simple, manual draining of the
collecting tank in case of pump failure (not obligatory).
7.3 Procedure for installation of lifting station
1. Check the scope of delivery.
For scope of delivery, see section
.
2. Prepare the adjustable inlet on the back of Multilift M.
The turnable disk has a DN 100 inlet and allows the inlet
height to be adjusted to any height between 180 and 315 mm
above floor level. The most common heights, 180, 250 and
315 mm, are marked beside the inlet. See fig. 16. An inlet disk
with a DN 150 inlet is available as an accessory.
See fig. 17. The screws around the outer ring of the inlet disk
are not fully tightened, allowing the inlet disk to be turned.
This will allow the inlet to be adjusted to the desired inlet
height. When the desired inlet height has been set, tighten all
screws. All screws must be tightened to max. 9 Nm.
Fig. 16
DN 100 inlet disk, adjustable from 180 to 315 mm
above the floor to the middle of the inlet pipe
Fig. 17
Optional DN 150 inlet disk, adjustable from 207 to
279 mm above the floor to the middle of the inlet pipe
Note
The collecting tank, pump and cables may be
flooded (max. 2 m for 7 days).
Caution
The controller must be installed in a dry and well
ventilated place.
Note
Before connecting Multilift M, consider that when
turning the inlet disk to fit to the height of the
inlet pipe, the lifting station and the discharge
will move sideways accordingly (max. 72.5 mm)
.
See fig. 16.
T
M
05
03
5
1
28
11
TM0
5
166
9
3
4
11
Summary of Contents for Multilift M Series
Page 1: ...GRUNDFOS INSTRUCTIONS Multilift M Installation and operating instructions...
Page 2: ...2...
Page 43: ...BG 43 7 LC 221 7 1 LC 221 11 11 LC 221 TM05 1807 3811 1234 AUTO 7 3 7 2...
Page 44: ...BG 44 7 4...
Page 48: ...BG 48 LED Man Auto LED ON OFF AUTO OFF LED ON OFF AUTO OFF 30 14 TM05 3455 0412...
Page 168: ...GR 168 6 LC 221 6 1 LC 221 11 11 LC 221 TM05 1807 3811 1234 AUTO 6 3 6 2...
Page 169: ...GR 169 6 4...
Page 292: ...KZ 292 5 2 2 9 1 6 1 Description of display 2 3 4 TM05 1805 3811 1 2 3 4 1 2 3 4 I 3 20 O...
Page 294: ...KZ 294 6 LC 221 6 1 Description of display LC 221 11 11 LC 221 TM05 1807 3811 1234 6 3 6 2...
Page 295: ...KZ 295 6 4...
Page 299: ...KZ 299 30 14 TM05 3455 0412...
Page 308: ...KZ 308 11 LC 221 1 a 5 2 LC 221 b 6 LC 221 c d F018 e f F005 10 4 Grundfos g...
Page 309: ...KZ 309 2 a 10 4 b F011 3 3 20 31 c F007 LC 221 8 4 LC 221 S3 12 10 4 3 a 24...
Page 420: ...UA 420 6 LC 221 6 1 LC 221 11 11 LC 221 TM05 1807 3811 1234 AUTO 6 3 6 2 Setup...
Page 421: ...UA 421 6 4...
Page 425: ...UA 425 Man Auto ON OFF AUTO OFF ON OFF AUTO 30 14 TM05 3455 0412...
Page 496: ...RU 496 8 LC 221 8 1 LC 221 11 11 LC 221 TM05 1807 3811 1234 8 3 8 2...
Page 497: ...RU 497 8 4...
Page 510: ...RU 510 13 LC 221 1 a 7 2 LC 221 b 8 LC 221 c d RELAY F018 e f SENSOR F005 12 4 Grundfos g...
Page 511: ...RU 511 2 a 12 4 b F011 3 3 20 31 c TEMP F007 LC 221 10 4 LC 221 S3 14 12 4 3 a 24...
Page 514: ...RU 514 15 1 2 Grundfos 16 24 Grundfos...
Page 699: ...CN 699 6 LC 221 6 1 LC 221 11 11 LC 221 TM05 1807 3811 1234 AUTO 6 3 6 2...
Page 700: ...CN 700 6 4...
Page 704: ...CN 704 Man Auto ON OFF AUTO OFF ON OFF AUTO OFF 30 14 TM05 3455 0412...
Page 716: ...Appendix 716 Appendix 1 Fig A Dimensional sketches M TM05 0440 1011...
Page 717: ...717...
Page 718: ...718...