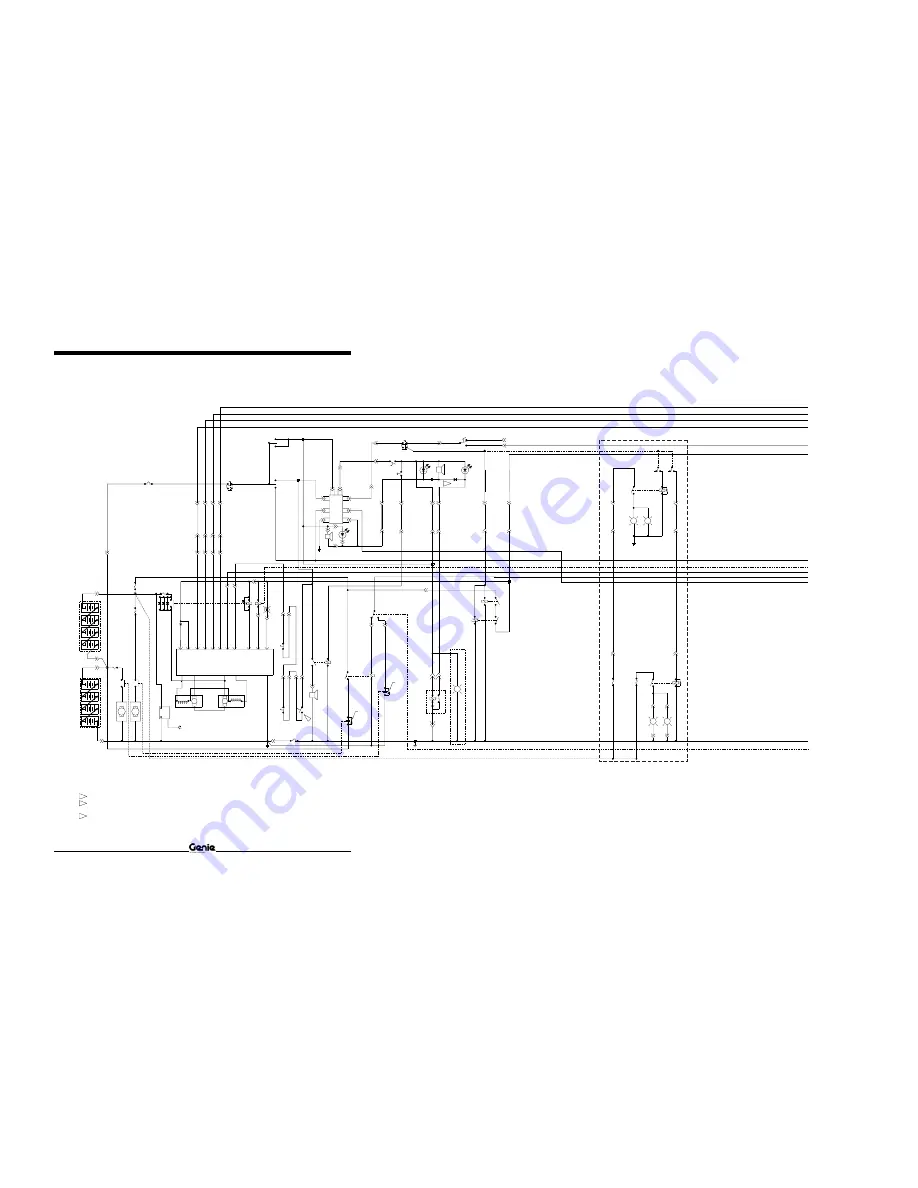
Section 6 • Schematics
June 2011
1
2
3
4
5
6
7
8
A
B
C
D
E
F
G
H
I
J
K
L
M
N
6 - 16
Z-30/20N • Z-30/20N RJ • Z-34/22 • Z-34/22N
Part No. 139378
Electrical Schematic, (CE)
(before serial numbers Z30N10-12119, Z34N10-8857 and Z3410-7774)
REV B
LS4-SEC. UP/DWN
LS2-PRI. UP/DWN
LS1-EXT/RET
C48-3
TB52
C9HRN BK/RD
C19LPE GR/WH
P42BAT OR/RD
85
86
PRIMAR
Y
L
IFT
PUMP
PR2
33
W
R19LPE GR/WH
PR2
CR20
30
87
AUXILIAR
Y
LIFT
PUMP
PR3
PRIMAR
Y
L
IFT
PUMP
CONT
ACT
OR RELA
Y
33
W
PR3
C49-1
1
C19LPE GR/WH
C49-1 R27AUX RD
87a
CR3
87
30
P42BAT OR/RD C48-2
C7B-2
P23BA
T
W
H
C7P-2
C48-1 P182BA
T
R
D
P22BA
T
B
K
RD
C134BAT RD
TB134
R42BAT OR/RD
C12FTS
10A
CB3
C133PLA
BL/RD
C2P-1
C2B-1
D39
L4
H6
L45
U33
U6A
MOTOR CONTROLLER
F4
500A
ADD D40 ONLY IF UNIT HAS L4 AND L48.
C3B-9
C1B-12
H2
GR/BK
RD
TB134
C1P-12
C132PLI BL/WH
C7B-1
LS18
D40
1
3
4
6
7
5
12
8
C40LS
C49-9
C29JSH RD/WH
C32JSL WH/RD
C30FWD WH
C31REV WH/BK
BK 2 GA
CHASSIS GROUND
J2-BK
RD
P26BAT
13
LS1
(EXT)
14
2
P22BA
T
B
K
C7P-1
HORN
B
A
C
P42BAT OR/RD
C49-7 C178CSL
BK
C49-10
C49-8
BK
C1
1-3 BK-6
C1
1-4 WH-6
C10-2 WH-7
C10-1 BK-7
P22LS BK
C52-1 BK-8
C52-2 WH-8
J1-WH
C49-3
C49-6
C49-5
C49-4
C2B-4
C3B-3
C1B-2
C1B-3
C1B-4
C1B-5
C1B-6
C9P-2
C9P-3
R42BA
T
OR/RD
C2P-4
C3BA
T
RD/WH
C3P-3
C28TT
A
RD/BK
C1P-2
C9HRN BK/RD
C3P-9
C29JSH RD/WH
C1P-3
C32JSL
WH/RD
C1P-6
C31REV WH/BK
C1P-5
CR5
P182BAT BK
C19LPE GR/WH
R42BAT OR/RD
P24BAT WH
RD
C12DRE BL/WH
CR3
GND BR
TILT
ALARM
RD
WH-(FS)
FS1
H1
RD-(FS)
PLATFORM
GROUND
P1
KS1
TB22
P3
HORN
P2
RD
C9P-1 BK
+
RD
P182BAT RD
BK-(FS)
OR/RD
CR1
CR2
TB42
RD/WH
30
87
85
86
87
30
86
85
BRN
BRN
PR1
OFF-LIMT
SPD INP
INTERLOCK
L3
5
3
17
C182PWR GR
LS4
(SEC)
OR/RD
LS2
(PRI)
RD/BK
OR/RD
C49-2 C48BRK RD/BK
OR/RD
20
CR5
22
21
22
21
86
85
CB2
10 A
C1P-4
RD 20
AP2
24 V
FOR
W
ARD
POT
. LOW
DIODE RETURN
+48V INPUT
POT
. HI
REVERSE
10
1
9
11
16
14
PR1
AP2
48V
R42BA
T
OR/RD
WH
WH/BK
WH/RD
RD/WH
F3
100A
F5
10A
F2
100A
+
+
+
+
LEFT
BOX
-
-
-
-
48V
C30FWD WH
2
48V POWER
RELA
Y
CR1
FLASHING BEACON
OPTION
48V POWER
RELA
Y
CR2
FB
+
HORN
RELA
Y
BASE CONTROL
BOX GROUND
CR4
TIL
T
SENSOR
RD
WH
BK
BRN
F1
+
86
85
30
87
BRN
BRAKE RELEASE
RELA
Y
CR5
PR1 DRIVE
CONT
ACT
OR
AP1
AUXILIAR
Y
LIFT
PUMP
PRIMAR
Y
LIFT
PUMP
PR3
PR2
WH
BK
AC POWER
F2
F1
A2
A1
A2
A1
+
-
PUMP
+
+
+
+
CHARGER
LEFT
MOTOR
RIGHT
BOX
-
-
-
-
GROUND
24V
SWITCH SHOWN WITH BOOM EXTENDED.
NOTES:
1. ALL LIMIT SWITCHES SHOWN WITH BOOM IN STOWED POSITION EXCEPT AS NOTED.
SWITCH SHOWN WITH BOOM ROTATED PAST EITHER NON-STEER WHEEL.
4. ALL SOLENOID AND RELAY COILS ARE 24VDC EXCEPT WHERE NOTED.
F2
F2
F1
B+
M-
AP1
B-
PUMP
RIGHT
MOTOR
2
3
5
5
BL/WH
L48
ES34DCT
OR
OR
TS48
DRIVE
LIGHTS
TS49
WORK
LIGHTS
CR45
N.O.
87
30
86
85
L30
+
L30
+
PLATFORM BOX
GROUND
C1B-9
R42BA
T
OR/RD
P48LPS WH/RD C1P-9
F18
7A
WH/RD C2B-9
WH (16/2)
C1B-8
DLITE BK/WH
C1P-8
F19
7A
BK/WH C2B-12
WH (16/2)
CR23
N.O.
87
30
86
85
L29
+
L29
+
WH
WH
WH
BK
BK
L30 WORK LIGHTS
(OPTION)
L29 DRIVE LIGHT
(OPTION)
WH
Summary of Contents for Z-30/20N
Page 1: ......
Page 148: ...6 46 June2011 Section 6 Schematics 6 45 Power Cable Wiring Diagram...
Page 149: ...6 47 Section 6 Schematics June2011 6 48 Drive Contactor Panel Wiring Diagram...
Page 152: ...6 50 June2011 Section 6 Schematics Manifold and Limit Switch Wiring Diagram 6 49...
Page 153: ...6 51 Section 6 Schematics June2011 6 52 LVI BCI Option Wiring Diagram...
Page 156: ...6 54 June2011 Section 6 Schematics 6 53 Charger Interlock Option...
Page 157: ...6 55 Section 6 Schematics June2011 6 56 CTE Option CE Models...
Page 160: ...6 58 June2011 Section 6 Schematics Hydraulic Schematic 6 57...